Introduction
The plastics manufacturing industry is a vital component of countless sectors, from automotive to consumer goods, and its market value is expected to exceed $640 billion by 2025. However, it faces unique challenges, including high material costs, precision requirements, and sustainability demands. eMoldino, a Tooling Digitalization Solutions company, is at the forefront of addressing these challenges. By offering an innovative solution that enhances efficiency, extends tooling life, and improves quality, eMoldino helps plastics manufacturers adapt to modern demands and achieve greater operational resilience.
Industry Challenges and eMoldino’s Solutions
1. Machine and Tooling Maintenance
Challenge: Mold and tool failures lead to downtime that costs the plastics industry an estimated $200 million annually.
One of the primary challenges in plastics manufacturing is managing tooling maintenance and lifecycle effectively. Mold and tooling failures can lead to significant downtime and production delays, impacting both profitability and customer satisfaction. eMoldino’s IoT-enabled sensors monitor mold conditions in real-time, providing valuable data on parameters like temperature, pressure, and wear. This data allows manufacturers to adopt predictive maintenance strategies, identifying and addressing potential issues before they lead to costly failures.
2. Quality Control and Scrap Reduction
Challenge: Defective parts, resulting in high scrap rates, can account for 5-10% of production costs in plastics manufacturing, representing $15 billion in annual losses globally.
In an industry where precision is paramount, maintaining high quality standards is crucial. Even minor deviations in molding conditions can lead to defects, resulting in high scrap rates and increased production costs. eMoldino’s analytics platform captures and analyzes production data, identifying patterns that contribute to defects. By optimizing process parameters and reducing scrap, manufacturers can improve product consistency and reduce material waste, contributing to both cost savings and sustainability goals.
3. Data Accessibility and Connectivity Across Sites
Challenge: Multi-site operations often lack real-time data visibility, leading to inconsistent quality and efficiency levels across facilities.
Plastics manufacturers often operate across multiple facilities, making it challenging to ensure consistent production quality and process optimization. eMoldino addresses this issue by providing centralized, cloud-based data access, allowing stakeholders to monitor operations across different sites in real time. This holistic view of production data enables better decision-making and ensures uniformity across the manufacturing network, reducing the variability that can arise from disparate data silos.
Use Cases: How eMoldino Drives Impact in Plastics Manufacturing
1. Automotive Plastics Production
The automotive sector relies heavily on high-quality plastic components that meet rigorous safety and durability standards. For automotive plastics manufacturers, eMoldino’s solutions offer enhanced control over mold performance and product quality. With preventive maintenance capabilities, manufacturers can prevent tooling breakdowns and ensure uninterrupted production schedules, a critical factor in meeting stringent automotive industry timelines.
Impact: By reducing tool breakdowns by 20%, automotive plastics manufacturers save an average of $300,000 annually per facility in reduced downtime costs.
2. Consumer Goods and Electronics
In industries such as consumer electronics, where plastic parts must meet high aesthetic and functional standards, any deviation can lead to product recalls or costly rework. eMoldino’s data-driven approach provides insights into optimal molding conditions, helping manufacturers achieve consistent quality and reduce scrap rates. For example, by analyzing temperature and pressure variations, eMoldino can help manufacturers fine-tune their processes to minimize defects, leading to improved yield and lower costs.
Impact: For manufacturers of high-standard plastic parts, eMoldino’s solutions help decrease defect rates by 25%, saving around $200,000 annually per production line.
3. Packaging Industry
In the packaging sector, plastics must meet standards of durability, weight, and recyclability. eMoldino’s solutions facilitate the optimization of material usage, helping manufacturers meet sustainability targets while minimizing production costs. With real-time monitoring and data analysis, manufacturers can identify process inefficiencies and reduce energy consumption, making the entire production process more eco-friendly.
Impact: eMoldino reduces energy costs by 15% and material waste by 20%, directly contributing to sustainability targets.
Cost Savings and ROI with eMoldino
One of the significant advantages of eMoldino’s solutions is the potential for cost savings. By minimizing downtime, reducing scrap, and optimizing energy consumption, eMoldino helps plastics manufacturers achieve substantial operational efficiencies. Preventive maintenance, in particular, extends the lifespan of molds and toolings, leading to reduced replacement costs. Additionally, real-time insights into production processes enable quicker adjustments, reducing the time and costs associated with defect resolution.
Studies have shown that by implementing preventive maintenance and process optimization, manufacturers can reduce maintenance costs by up to 20% and increase asset availability by 10%. For an industry facing tight profit margins, these improvements translate into measurable gains, making eMoldino’s solutions a valuable investment.
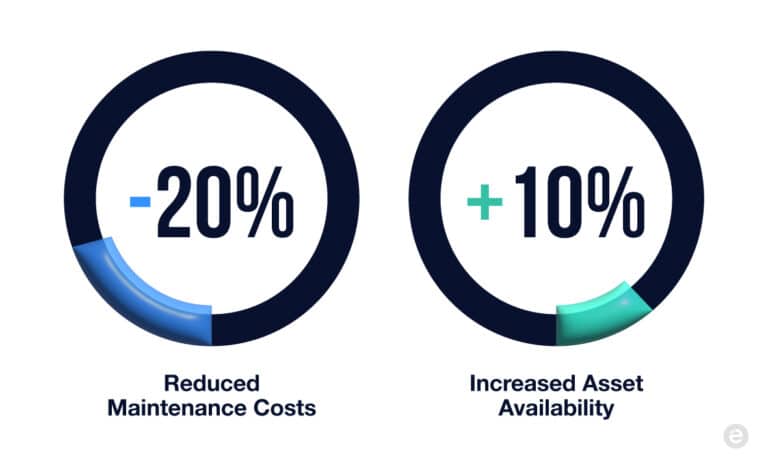
Adopting eMoldino’s solutions yields measurable financial gains:
- Maintenance Cost Reduction: Predictive maintenance cuts maintenance costs by 20% and improves tool availability by 10%.
- Scrap Rate Reduction: Scrap reduction translates to an average savings of $1 million annually per facility.
- Overall ROI: eMoldino provides an estimated 200% return on investment within two years of implementation.
Conclusion
About the author
eMoldino
eMoldino aims to digitalize, streamline, and transform your manufacturing and supply chain operations. We help global manufacturers who want to drive corporate innovation while maintaining the core values of collaboration and sustainability. Talk with us to learn more →
Did you enjoy reading this article?
0 / 5. Vote count: 0
Explore Our Latest Posts
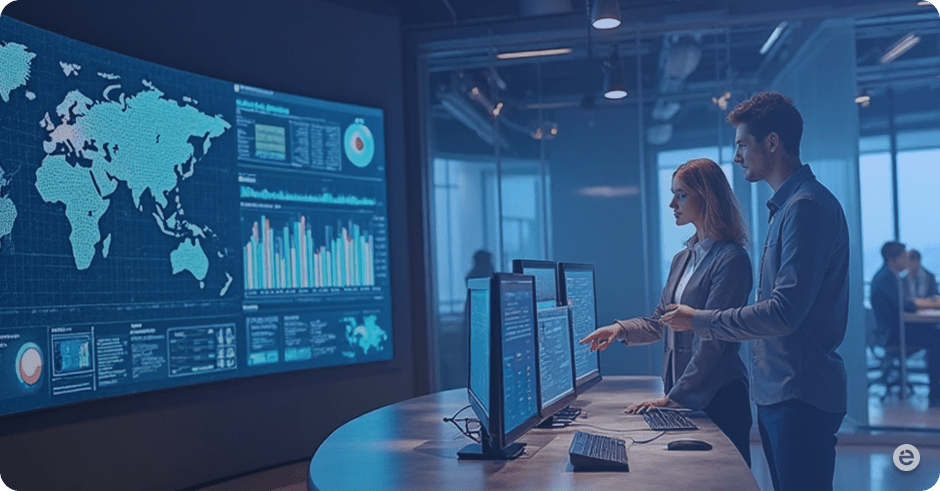

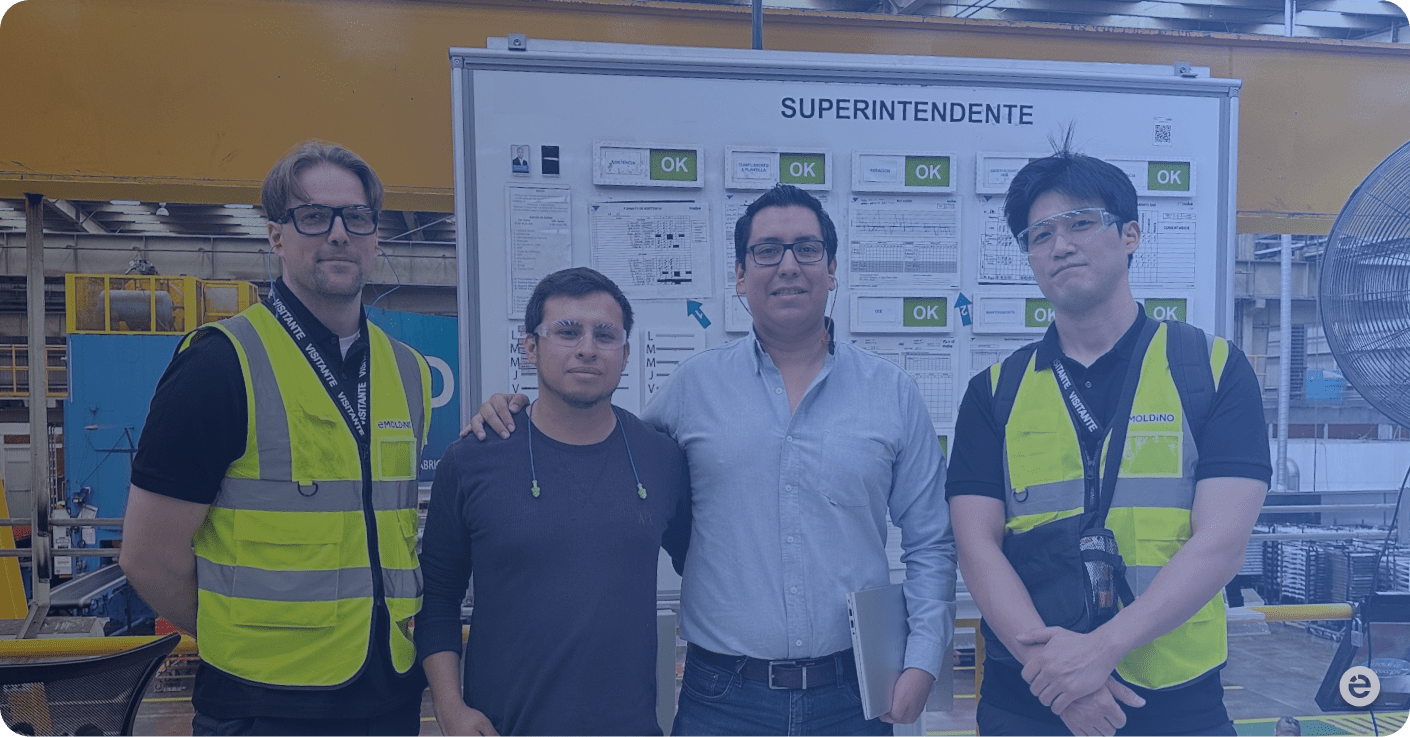
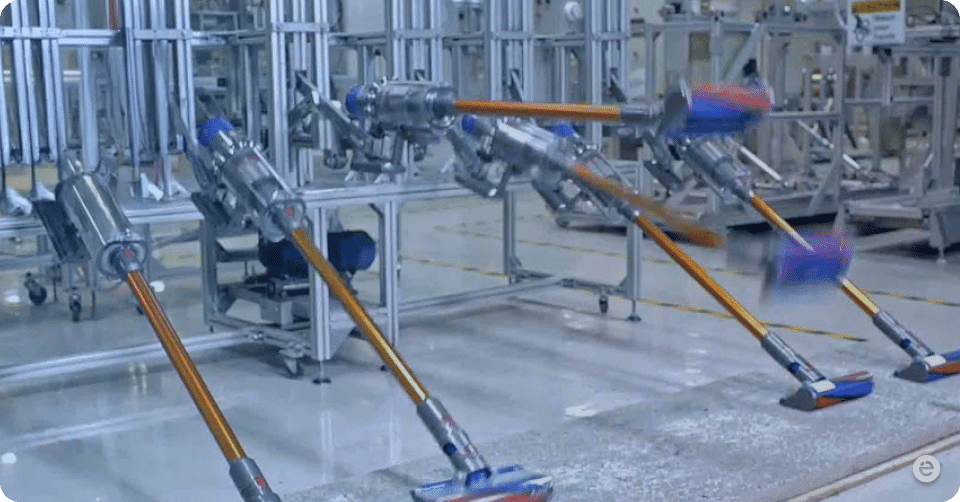
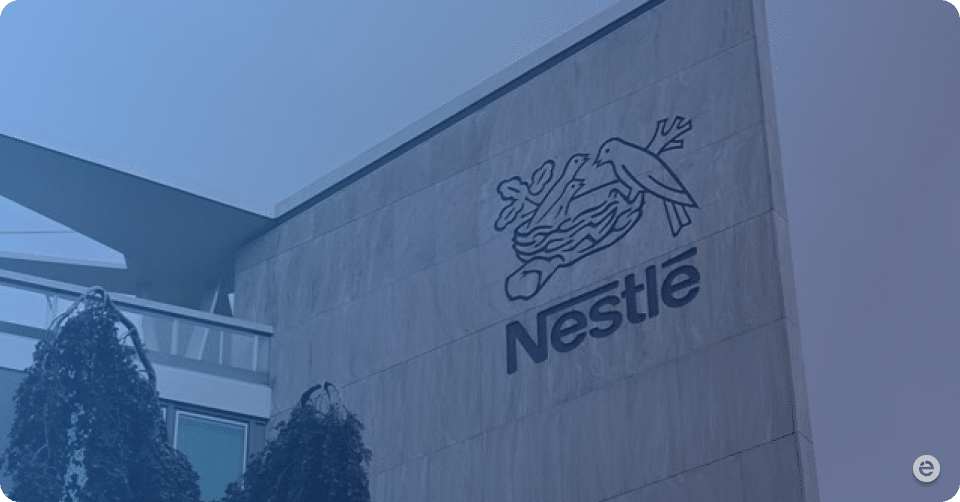
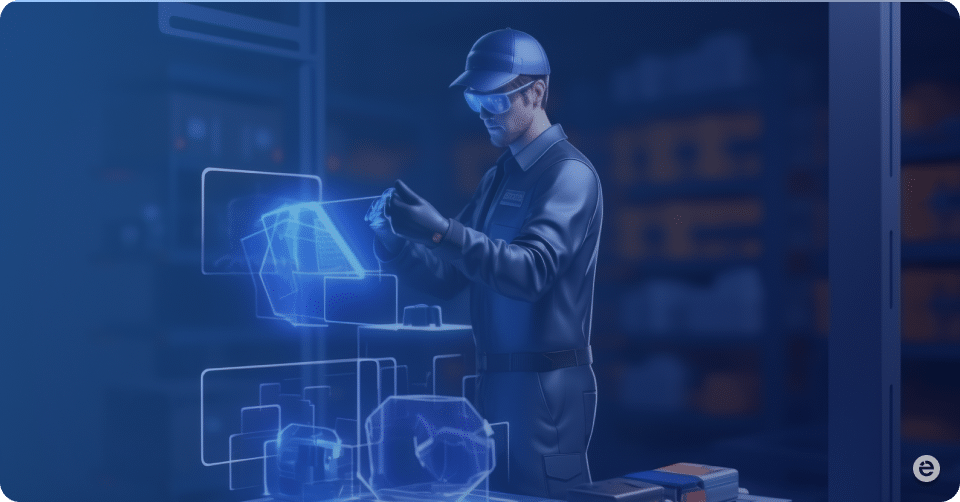
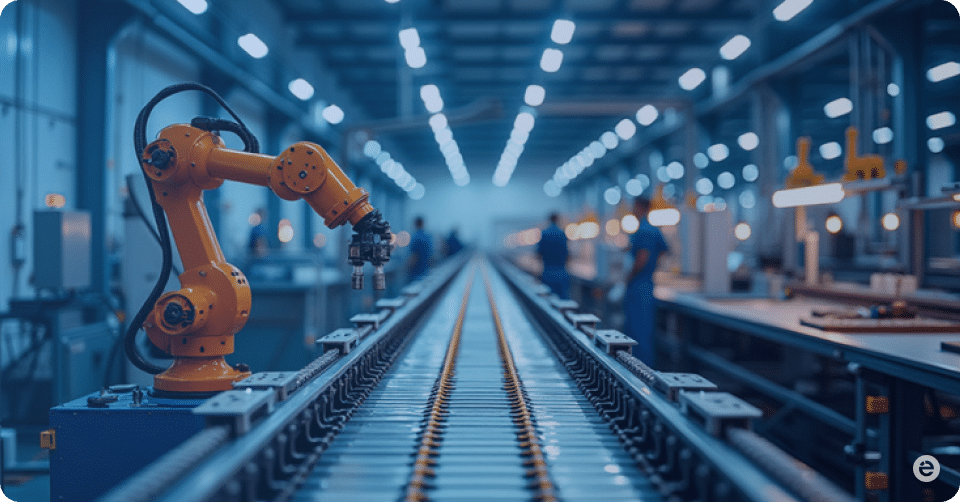
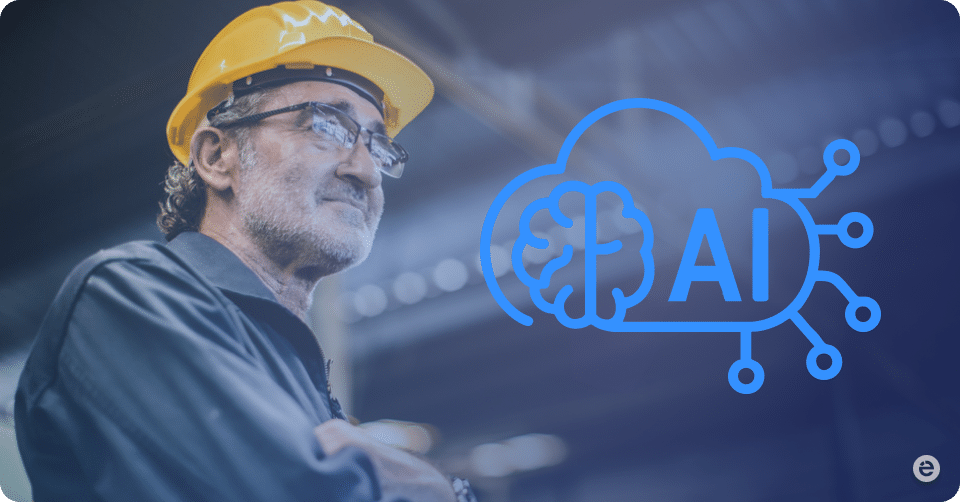
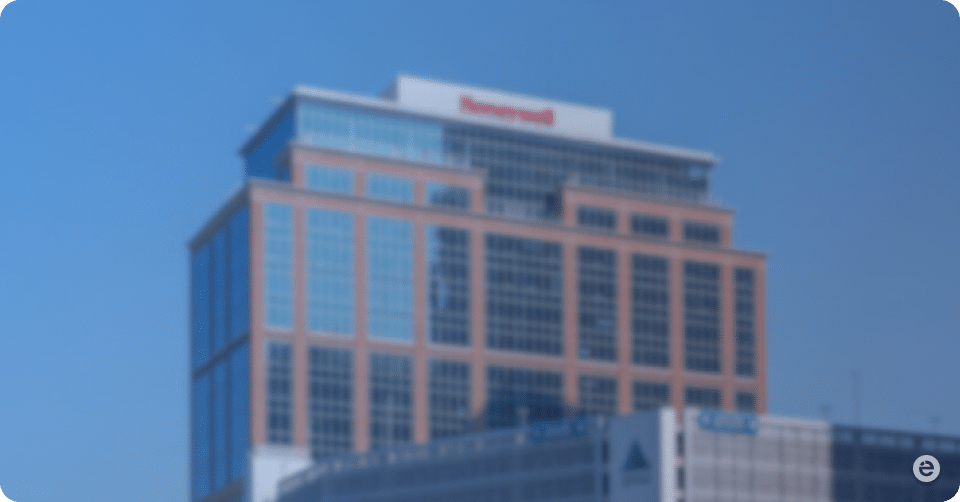
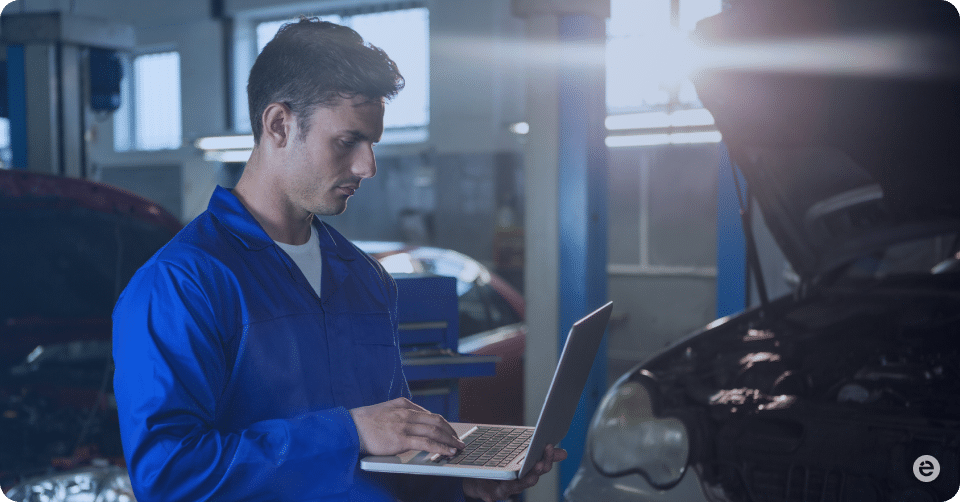