AUTOMOTIVE
2023.12.19 | Updated: 2023-12.29
Convergence of Tooling Digitalization and Sustainable Manufacturing
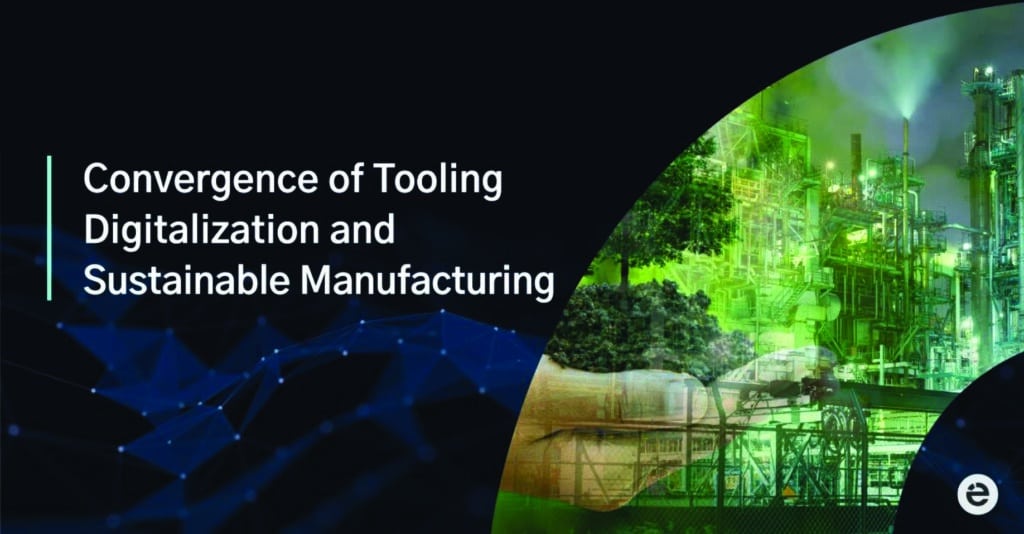
With the growing concerns over environmental issues, various industries, including the automotive sector, are now prioritizing sustainable manufacturing to reduce their carbon footprint and maintain competitiveness. A promising approach gaining momentum is the convergence of tooling digitalization with sustainable practices. This shift holds significant implications for an industry striving to enhance its sustainability initiatives. This article explores the transformative potential of such convergence by presenting a cutting-edge solution for the automotive industry, advancing towards operational excellence and a heightened commitment to environmental responsibility.
The Power of Convergence: Integrating Technology and Sustainability
Digitalization is an essential element in fostering a sustainable manufacturing environment
The convergence of tooling digitalization and sustainable manufacturing offers a transformative opportunity for the automotive industry. Incorporating advanced technology and digitalization has become crucial for achieving sustainability in manufacturing, fostering productivity improvement, waste management, and competitive advantage. Leveraging AI-driven analytics, processes can be streamlined, waste minimized, and resources optimized, all while gaining enhanced visibility into production operations. With this data, organizations can optimize production and improve predictive maintenance, reducing energy consumption.
For major Original Equipment Manufacturers (OEMs) that outsource their manufacturing to suppliers globally, the seamless integration of IoT sensors, artificial intelligence, and data analytics provides real-time insights into outsourced tooling performance and production efficiency. This data-driven approach boosts operational excellence and magnifies the impact of sustainability efforts, allowing waste reduction, precise material usage, and proactive maintenance.
Responsible Responsible sourcing also emerges as a critical element in promoting sustainable practices. Automotive executives gain valuable insights into supplier performance and compliance by employing tooling digitalization. Research by Capgemini indicates that 62% of automotive organizations now prioritize comprehensive sustainability strategies with well-defined goals and targets, underscoring the increasing importance of sustainable sourcing in the industry. Prioritizing partnerships with environmentally conscious suppliers enables automotive companies to align their sourcing practices with social responsibility initiatives and sustainability goals, fostering a greener and socially responsible future.
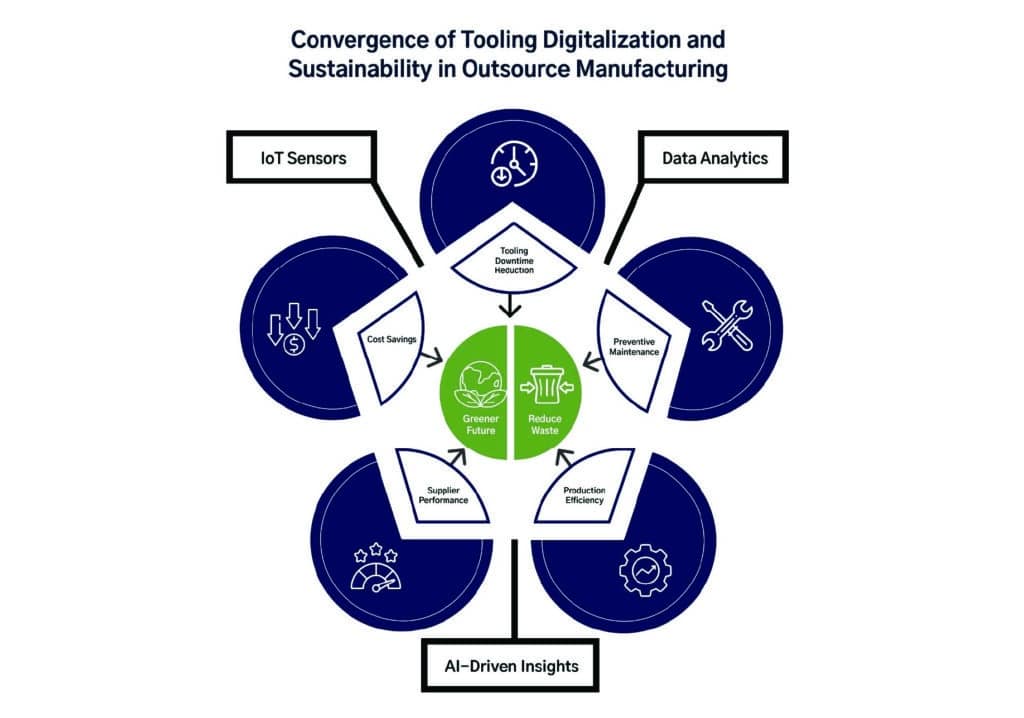
Real-World Success Story
Tooling Digitalization is Driving Sustainable Manufacturing in the Automotive Industry
Leading automotive companies that embrace this transformative approach have already witnessed measurable outcomes, affirming the viability of the synergy between tooling digitalization and sustainable manufacturing. One such company is a prominent German multinational automotive parts manufacturer, exemplifying this success with significant strides in tooling digitalization and sustainability. They achieved remarkable results by integrating advanced technologies and data- driven insights, optimizing operations, and driving toward a greener future.
Utilizing tooling digitalization, the company’s maintenance team gained unprecedented visibility into preventive maintenance, empowering them with real-time data and timely alerts for proactive measures. This approach substantially reduced tooling downtime, improving productivity and cost savings. Moreover, the company’s proactive maintenance approach led to substantial cost reductions related to quality issues, as timely interventions and preserved tooling integrity curtailed product defects and costly rework, elevating overall product quality. The company could refine its manufacturing processes by analyzing historical data and performance trends, reducing the likelihood of errors and defects in the production line. This data-driven maintenance approach optimized tooling performance and contributed to waste and resource reduction, aligning perfectly with responsible waste management and broader sustainability goals.
Furthermore, the company’s commitment to tooling digitalization resulted in enhanced energy efficiency during manufacturing processes. Thanks to the solution’s predictive maintenance capabilities, toolings are adequately maintained and serviced in advance, preventing breakdowns. This proactive approach minimizes unplanned downtime, which would otherwise lead to energy wastage during idle periods. As a result, the company achieved reduced energy consumption and lower associated carbon emissions, significantly contributing to its efforts to minimize its carbon footprint. By unlocking the full potential of its molds through digitalization, the company demonstrated steadfast dedication to reducing environmental impact and embracing transformative change, further solidifying its journey toward sustainable manufacturing.
Explore Our Related Posts

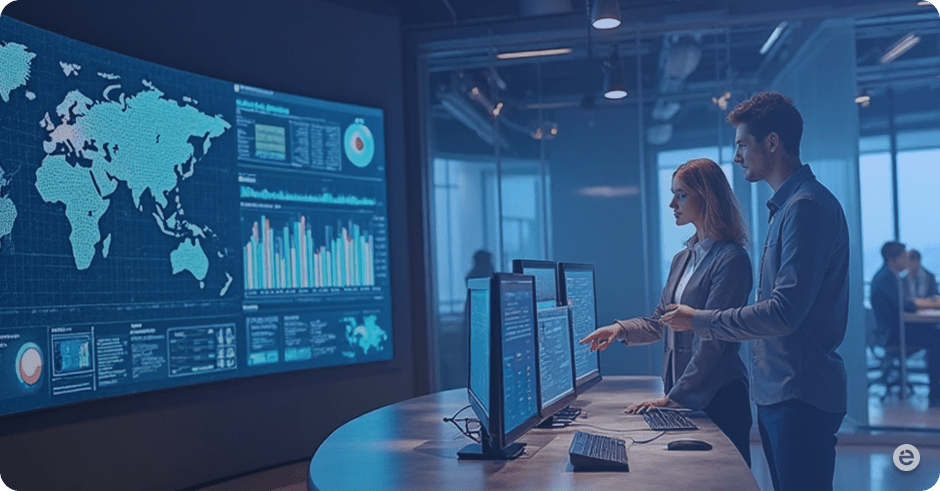

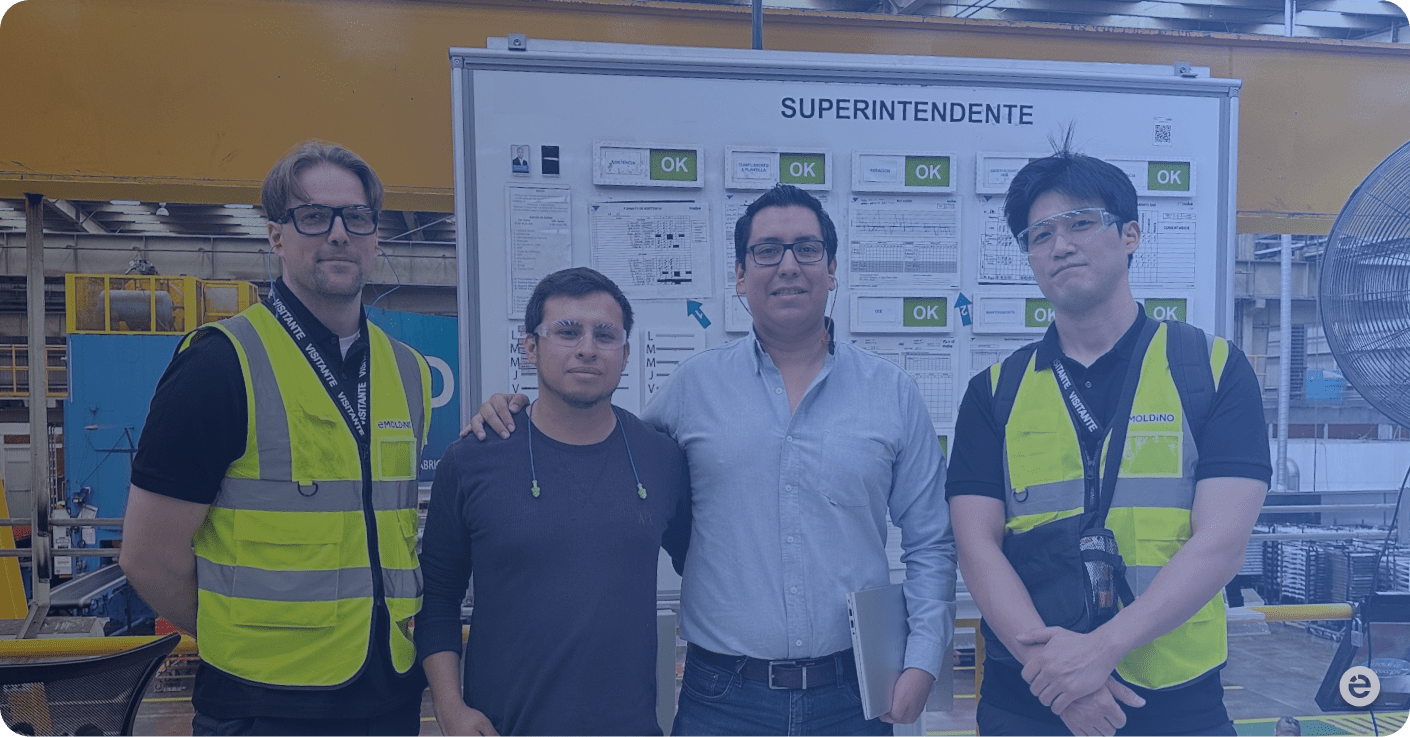
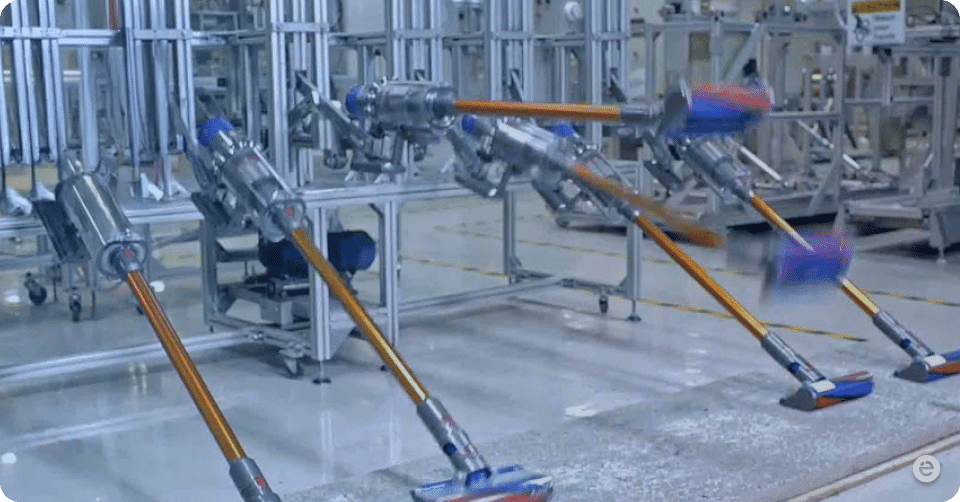
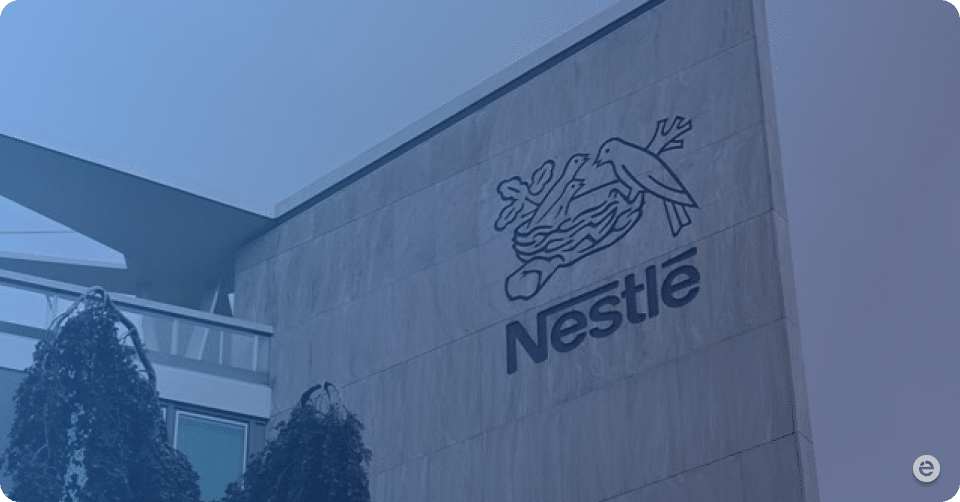
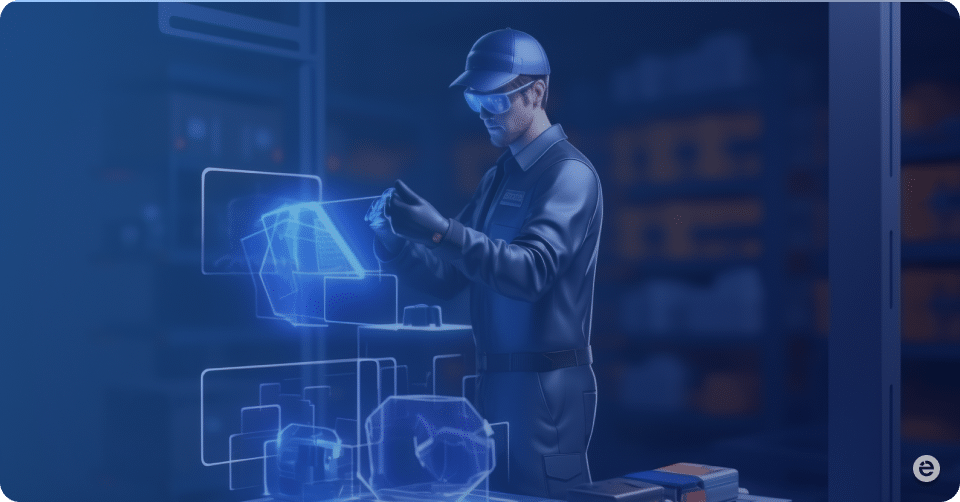
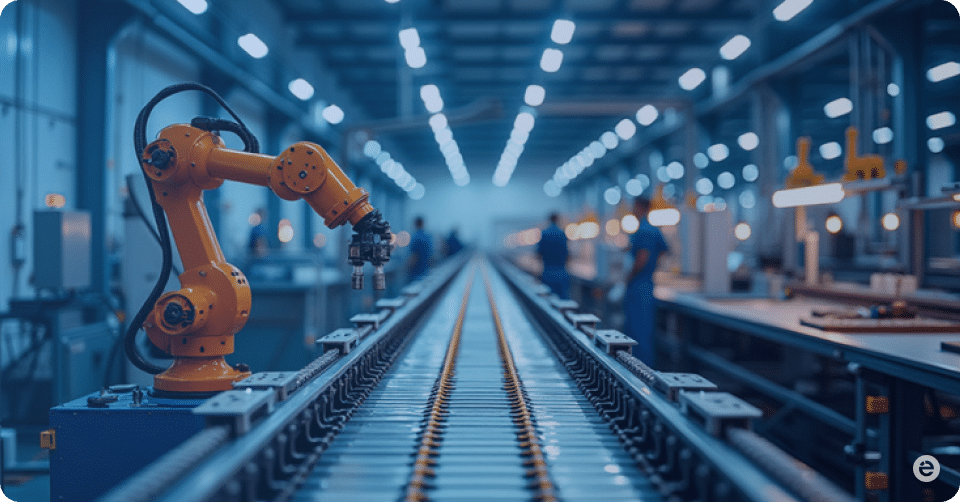
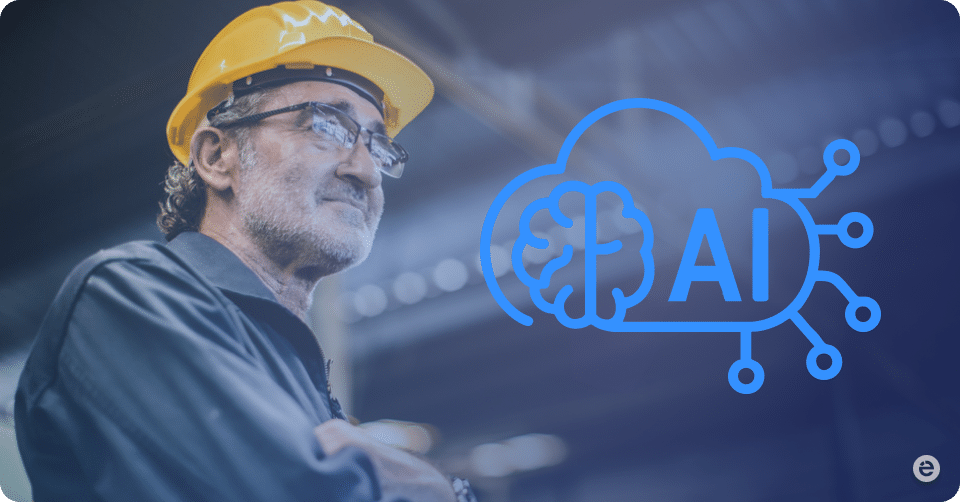
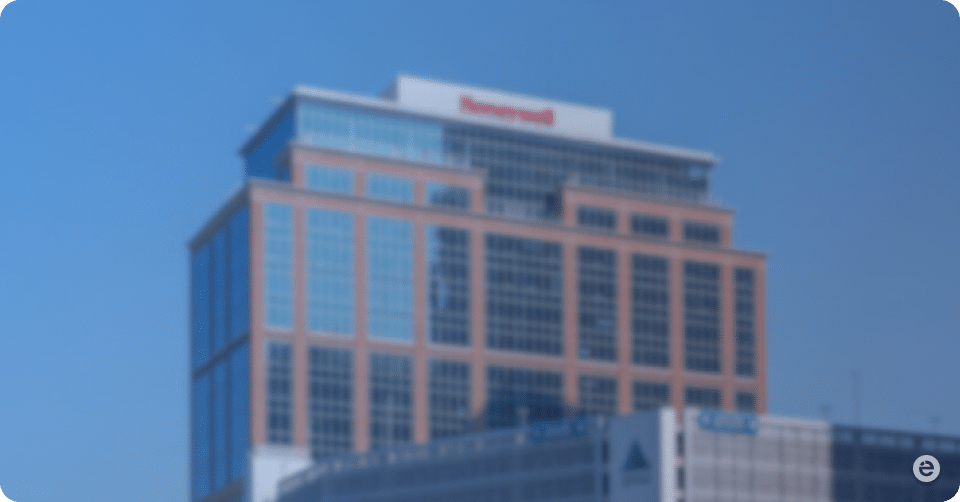