Imagine the strategic risk of neglecting an asset as crucial as your outsourced tooling —one that underpins the production of critical components in your supply chain. Just as your luxury car requires regular maintenance to avoid costly breakdowns, shouldn’t your toolings, scattered across global supplier sites, demand the same vigilance?
Yet, many OEMs overlook this need, relying on their suppliers who often deprioritize maintenance because the toolings are not theirs. This reactive tooling maintenance approach is a ticking time bomb with far-reaching consequences.
For OEMs, the consequences of poor tooling maintenance ripple across the organization. When a tooling fails unexpectedly, the financial impact is immediate:
- Escalating Operational Costs: A single day of production downtime can cost millions of dollars, as entire assembly lines grind to a halt. The costs multiply when considering the overtime needed to compensate for lost production and expedited shipping fees for delayed parts.
- Revenue Shortfalls: Delays in product launches due to tooling failures can lead to significant revenue losses. Late product release means missed sales opportunities and diminished market share, as competitors seize the moment to capture your customers.
- Compromised Product Quality: Tooling failures can lead to defective parts, which, in turn, result in warranty claims, and damaged customer trust. A tarnished brand reputation can take years—and significant investment—to rebuild.
These setbacks can be the difference between leading and lagging behind.
The Case for Preventive Maintenance
Shifting from a reactive to a proactive maintenance strategy is key to enhancing operational efficiency and avoiding costly downtime. A robust tooling lifecycle management system is essential to achieve this. Such a system provides real-time data on every aspect of your tooling—from inventory and location tracking to usage patterns and performance metrics—allowing for informed decisions on when to repair, replace, or upgrade toolings.
Moreover, implementing a digital system that tracks maintenance based on the number of shots each tool undergoes is critical. This system includes comprehensive information on maintenance history, materials used, and other relevant details. By monitoring these factors, users can ensure that preventive maintenance is conducted on time, reducing the risk of unplanned downtime.
The importance of preventive maintenance lies in its ability to preempt issues before they lead to significant disruptions. By having real-time insights into tooling conditions, companies can schedule maintenance activities more effectively, preventing breakdowns that can halt production and incur substantial costs.
Data-Driven Success – The case of a consumer electronics company
In many organizations, maintenance is traditionally scheduled based on time intervals rather than actual tooling usage, leading to inefficiencies and frequent corrective maintenance—often exceeding 90 monthly incidents. However, companies have seen significant improvements by shifting to a data-driven approach where maintenance is scheduled based on real-time metrics like shots and tooling utilization.
For instance, eMoldino’s tooling lifecycle management solution leverages real-time data to minimize corrective maintenance by 44%, leading to substantial cost savings—$110,000 per month and $1.32 million annually. Considering that corrective maintenance costs can range from $500 to $5,000 per incident, the financial benefits of a preventive approach are undeniable.
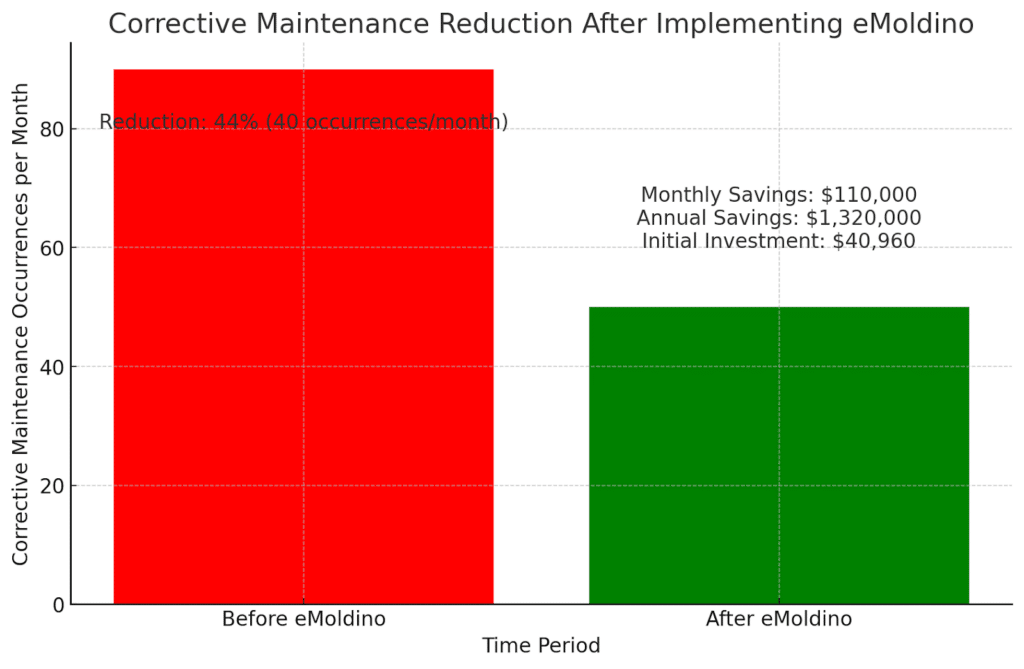
After implementing eMoldino, the company saw a significant reduction in corrective maintenance. Previously, they were conducting 90 corrective maintenance activities per month, but this number dropped to 50 per month with the new system in place. This represents a reduction of 40 occurrences each month, highlighting the effectiveness of eMoldino in streamlining maintenance processes.
Strategic Leadership in Tooling Management
As senior executives, your role is not just about managing current operations but also about safeguarding and enhancing your company’s long-term strategic interests. While tooling maintenance might seem like a granular concern, its impact on your organization’s bottom line and market position is profound.
Consider the significant financial and operational benefits of a proactive maintenance strategy. Companies that have adopted comprehensive tooling lifecycle management systems have experienced substantial reductions in unplanned downtime and extended tooling lifespans. These companies save millions annually, which can be reinvested in strategic initiatives like R&D and product development, thereby accelerating their market competitiveness.
For instance, the consumer electronics giant that reduced corrective maintenance incidents by 44% using eMoldino’s solution didn’t just improve operational efficiency; they transformed those savings into opportunities for innovation, such as expanding their product lineup. This demonstrates how a strategic focus on proactive maintenance can directly contribute to long-term growth and market leadership.
The stakes are clear: investing in robust preventive maintenance and leveraging data-driven insights is not just about preventing downtime—it’s about positioning your company for continued success and long-term competitive advantage. Consider this: How do you elevate your tooling maintenance from a factory-floor concern to a boardroom priority? The cost of neglect is far too high, and the strategic implications are significant.
About the author
eMoldino
eMoldino aims to digitalize, streamline, and transform your manufacturing and supply chain operations. We help global manufacturers who want to drive corporate innovation while maintaining the core values of collaboration and sustainability. Talk with us to learn more →
Did you enjoy reading this article?
3.8 / 5. Vote count: 4
Explore Our Latest Posts
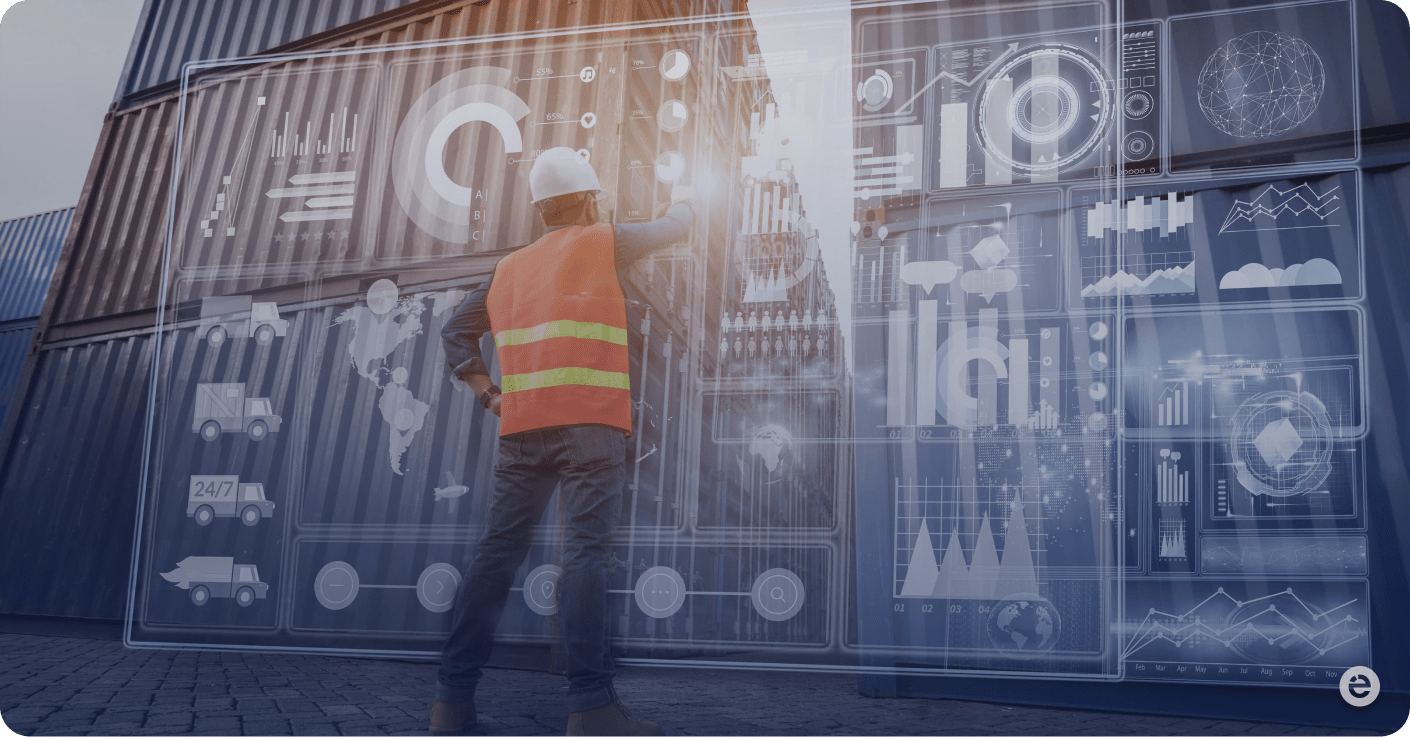
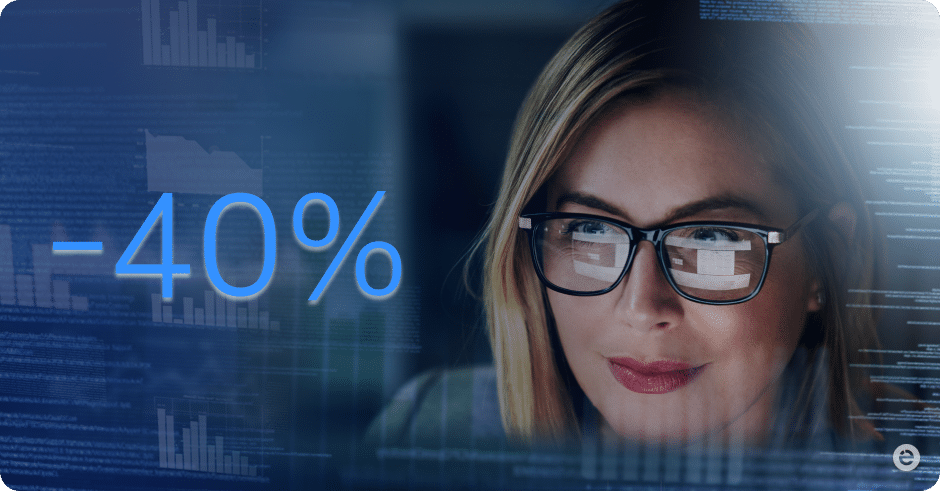
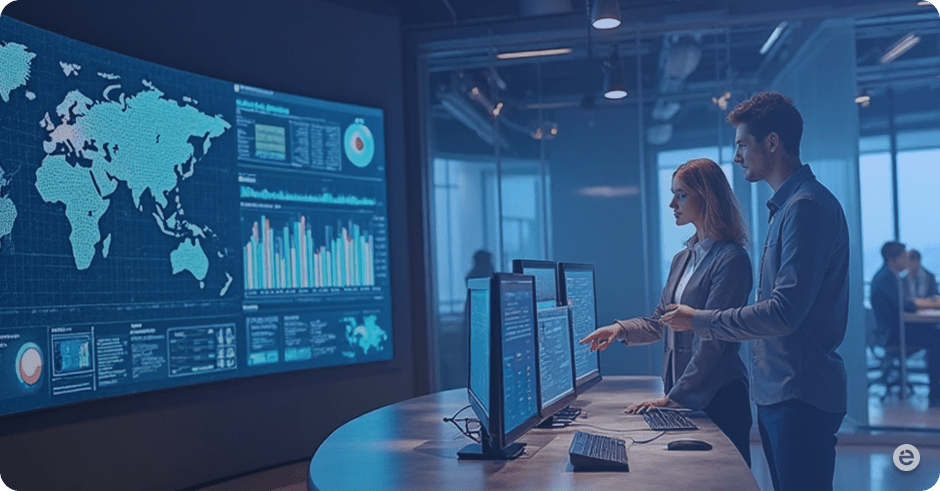

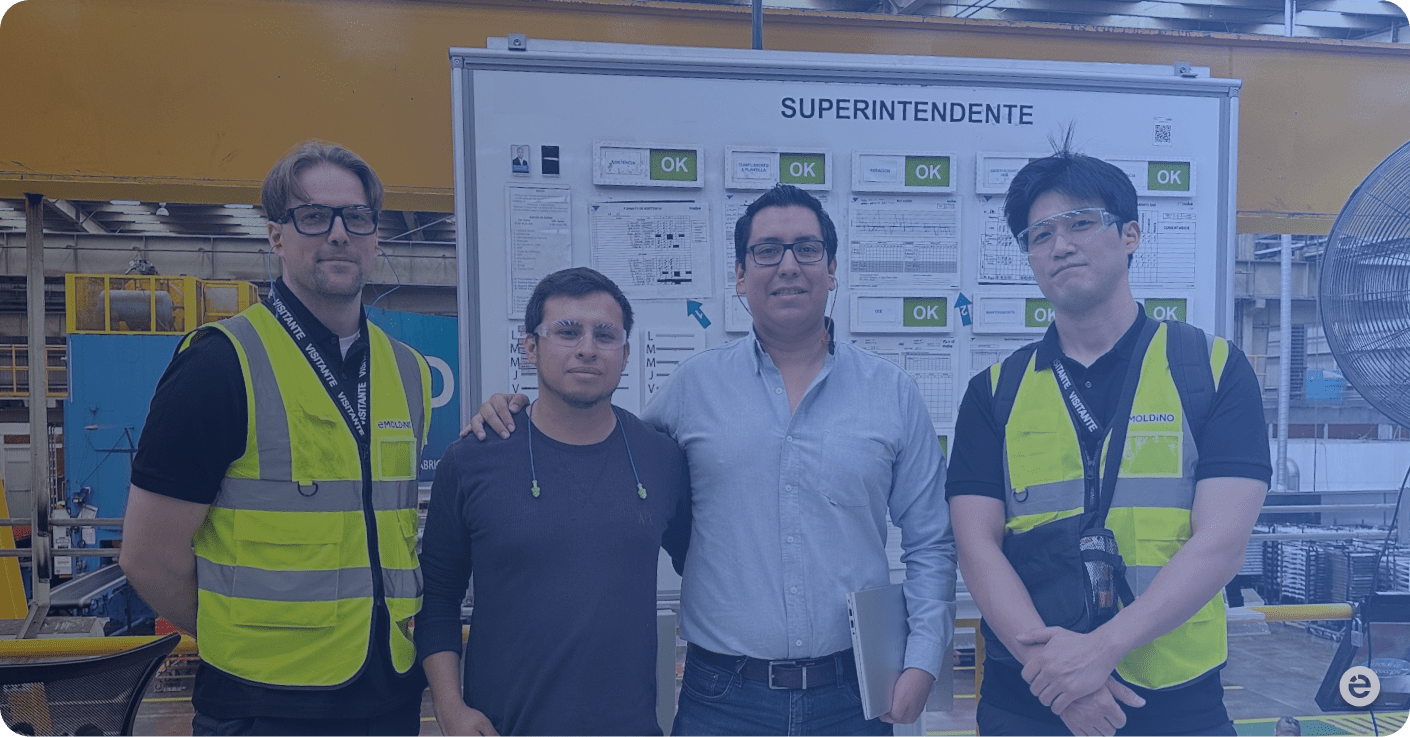
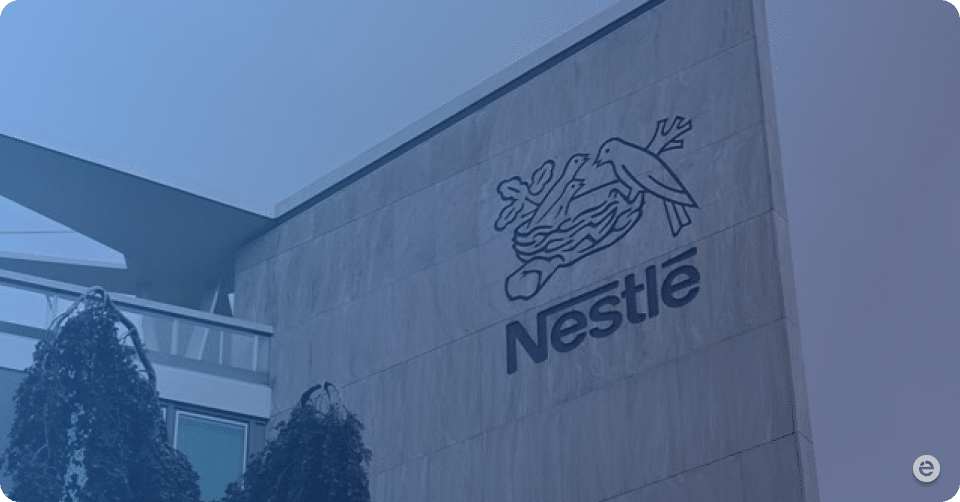
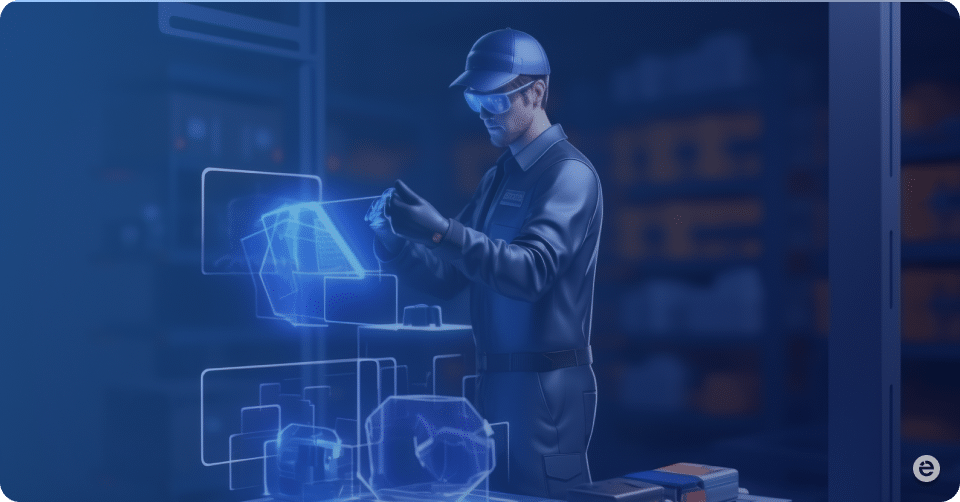
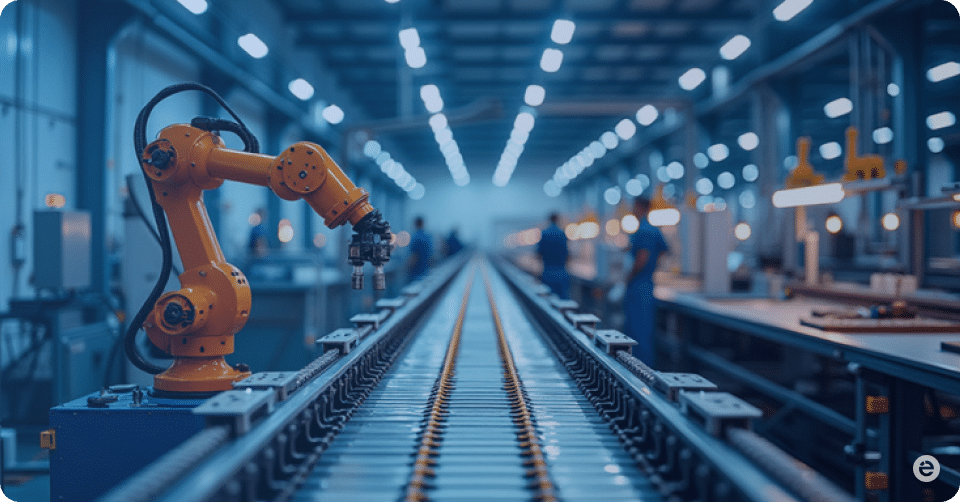
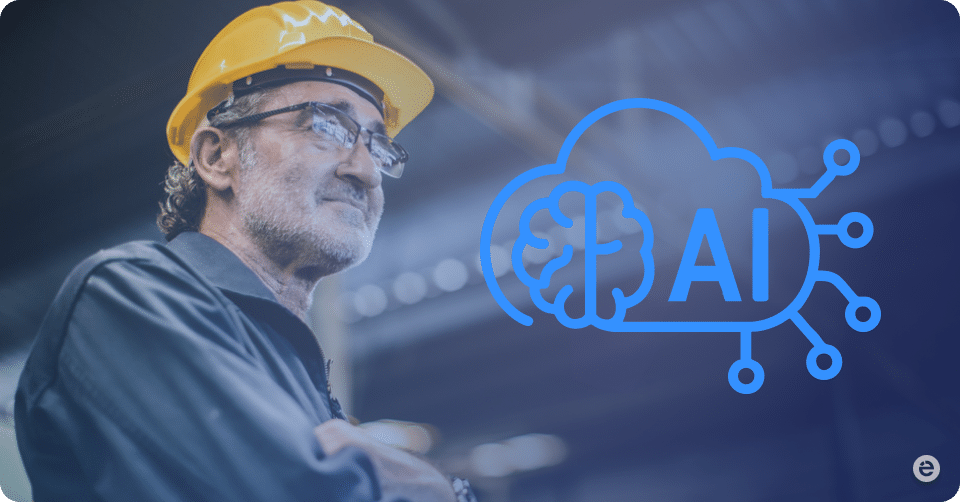
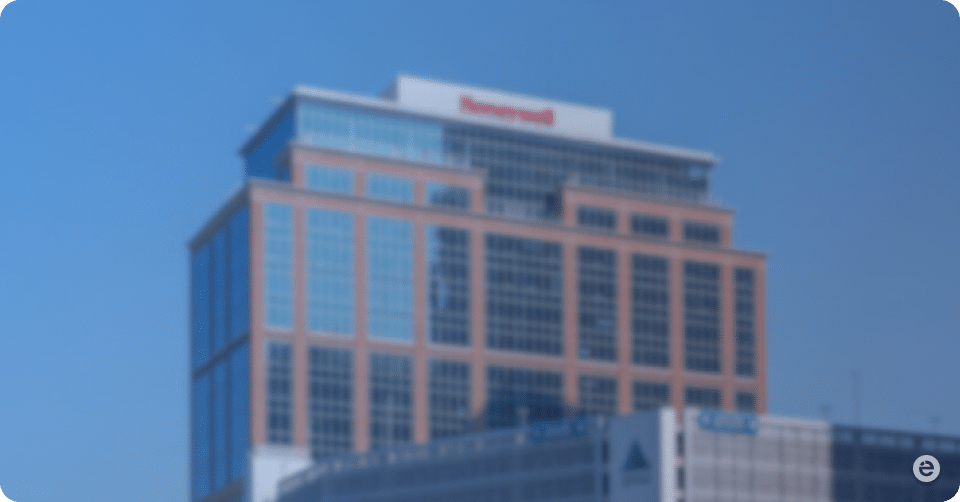
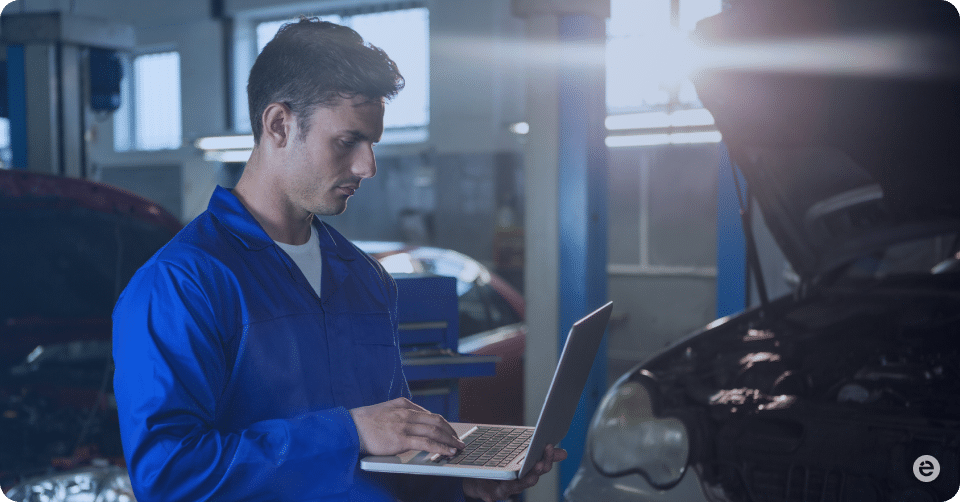