Managing supplier relationships becomes almost impossible because procurement teams waste 20% to 50% of their working hours looking for information . Everyone knows how frustrating it is to search for accurate supplier data. This issue goes beyond simple inconvenience. The numbers tell a compelling story – 93% of procurement and supply chain leaders have felt the negative impact of supplier misinformation . About half of them (47%) deal with these issues regularly .
Bad data quality in outsourced manufacturing creates serious problems. Teams lose precious time (63%) and face project holdups (47%). Sometimes relationships with suppliers end completely . Manufacturing companies now focus on tooling digitalization and supplier analytics as they move toward digital transformation. Organizations that use reliable data analytics solutions see impressive gains in supplier performance. This shift changes how companies handle their supply chain management in today’s data-focused environment.
Big Data Improves Supplier Visibility and Accuracy
The digital revolution in supply chain management has revealed a harsh reality: organizations operate with flawed supplier information. Studies show that 81% of procurement leaders doubt their supplier data’s accuracy. This doubt makes sense—60% of executives take four days to update outdated supplier information. The delays create a domino effect throughout operations.
Bad supplier data quality shows up in several harmful ways. Organizations face missed deadlines (51%), unhappy clients (42%), and direct financial losses (40%). Companies that lost money due to data misinformation did so within six months 67% of the time, which proves how common these problems are.
Old methods of supplier information management no longer work well enough. Many procurement teams still use basic research tools like online search engines (63%), industry conferences (63%), and publications (59%). Meanwhile, leading organizations reshape the scene with advanced big data applications to manage supplier relationships.
Big data analytics gives companies a clear view of tiny details that affect supplier performance. To name just one example, see how a dairy farm used RFID and IoT sensors to spot problems with cattle health, fodder quality, and temperature changes—factors that directly impact product quality. This better visibility helped them make more nutritious, uniform products.
Companies that use big data analytics throughout their supply chains see amazing results. UPS has cut gas consumption by 1.6 million gallons yearly in deliveries since 2016. They make use of information throughout their shipping process with sensors and radars to track items during transit and find the best delivery routes.
Manufacturing operations get vital planning insights from big data. Companies gather and analyze supply network data to predict demand accurately. Their statistical models look at past data, current information, industry trends, competitor data, and economic factors. This complete approach helps companies avoid running out of stock while keeping ideal inventory levels.
Yet trust remains the biggest problem—even for companies with advanced systems. More than half of companies (58%) with supplier portals don’t trust their suppliers to maintain current information. This shows that technology alone can’t fix supplier data problems without proper management processes.
Analytics Predict Late Deliveries and Lead Time Variations
Predictive analytics is changing the game for OEMs who want to solve one of their biggest headaches: late deliveries and lead time variations.
OEMs worldwide have always had trouble seeing their tooling asset data clearly, which leads to late parts and other problems. These days, knowing how to spot delays before they happen keeps production running smoothly. A newer study, published in, shows manufacturers need exact daily updates about when each part will arrive late. This helps them avoid having too much inventory or running out completely.
Smart machine learning algorithms now let OEMs predict how well their suppliers will perform with amazing accuracy. LSTM (Long Short-Term Memory) models work really well for time-series regression problems. They can forecast delivery changes with a median error of just 4.1 days in MAE (Mean Absolute Error). These smart models look at supply chain history and spot patterns that people might miss.
OEMs can switch from fixing problems after they happen to stopping them before they start with predictive analysis. This saves them money in the long run. The system looks at data from many sources:
-
Past delivery track records
-
Production logs and equipment sensor readings
-
Outside factors like weather, worker availability, and market changes
This detailed view helps companies spot bottlenecks before they turn into expensive problems. OEM managers use these tools to cut down on late-parts delivery risk by getting delivery projection reports.
Predictive analytics makes risk management better by warning about possible problems early. Companies can find risky suppliers by checking their performance and outside factors. Then they can vary their supplier options. This helps both OEMs and suppliers handle supply chain risks better.
In spite of that, making these systems work has its challenges, especially when you have data quality issues. Predictive models need good historical data, but many companies don’t deal very well with incomplete or old information across their systems. Companies that solve these problems get ahead of their competition. The proof? About 77% of logistics partners now put money into predictive analytics to make more profit.
OEMs Report 40% Performance Boost from Big Data
Manufacturing has changed dramatically. New industry reports show that 53% of manufacturers now rely on big data analytics to stay competitive. Original Equipment Manufacturers (OEMs) who adopt detailed data analytics solutions have seen their performance improve by 40% across key metrics.
The market reflects this enthusiasm for big data in manufacturing. Experts predict the sector’s big data market will reach USD 9.11B by 2026. These numbers show how essential intelligent technology has become in modern manufacturing business models.
Procurement specialists highlight how big data analytics offers unmatched advantages in managing supplier relationships through:
-
Real-time visibility into supplier metrics including on-time delivery, quality control, and pricing fluctuations
-
Predictive capabilities that anticipate potential disruptions in the supply chain
-
Better collaboration through shared data and performance metrics
Companies see real benefits when they put big data solutions to work. A manufacturer worked with an analytics provider to set up Supplier Performance Management (SPM). This created a central platform to collect and analyze data from multiple sources. The analysis of historical on-time delivery data revealed a bottleneck in their supplier’s production process—something they couldn’t have found without advanced analytics.
The financial results are impressive. Companies that use big data report lower costs through better negotiation power, reduced inventory expenses, and fewer disruptions. Some have cut machinery downtime—a common problem in outsourced manufacturing—by 20%.
Manufacturing companies focusing on digital transformation find that digital tools backed by data analytics create measurable improvements in workflow efficiency. Executives can make smarter decisions and improve supply chain flow by understanding how processes, departments, and problems affect their operations.
The 40% boost in performance comes from moving away from reactive operations to proactive ones. You can learn how to improve your supplier relationship management with informed decisions that spot problems before they affect production. Talk to eMoldino experts to see this approach in action.
Conclusion
Big data analytics has changed how OEMs manage supplier relationships. Poor data quality used to create headaches for procurement teams and led to wasted time and delayed projects. But organizations that accept new ideas and use evidence-based approaches now see about 40% better supplier performance metrics.
The move from reactive to proactive operations is the most important benefit. Companies can now spot problems before they affect production instead of just reacting to supplier issues. This has turned adversarial supplier relationships into mutually beneficial alliances built on shared data and common goals.
The financial impact is remarkable. Companies using these solutions cut costs through stronger negotiation positions, reduced inventory expenses, and fewer disruptions in production. On top of that, the 20% drop in machinery downtime saves manufacturers millions in production costs.
These impressive results come with their share of challenges. Data quality remains a stumbling block, as 58% of organizations don’t trust their suppliers to keep information current. Technology alone can’t fix supplier management problems without better processes.
The manufacturing industry sees these benefits clearly, as the big data market is set to reach USD 9.11B by 2026. Companies that don’t adopt these methods risk falling behind competitors who can better predict and optimize their supplier relationships. Ready to join innovative manufacturers who use data analytics to boost supplier performance? Talk to eMoldino experts to see how it works and gain an edge in today’s complex manufacturing environment.
Key Takeaways
Manufacturing companies implementing big data analytics are revolutionizing supplier relationships and achieving unprecedented performance improvements that directly impact their bottom line.
• OEMs achieve 40% performance boost through big data analytics, transforming reactive operations into proactive supplier management systems.
• Predictive analytics prevent costly delays by forecasting delivery issues with 4.1-day median accuracy, enabling proactive inventory management.
• Poor supplier data costs companies significantly – 93% of leaders report adverse effects from misinformation, with 67% experiencing financial losses within six months.
• Real-time visibility drives collaboration by providing centralized platforms that track on-time delivery, quality metrics, and pricing fluctuations across supplier networks.
• Manufacturing digital transformation is accelerating with the big data market projected to reach $9.11B by 2026, making early adoption critical for competitive advantage.
The shift from traditional supplier management to data-driven approaches represents more than technological advancement—it’s a fundamental change in how manufacturers build collaborative partnerships. Companies that embrace these analytics solutions position themselves to reduce costs, minimize disruptions, and create sustainable competitive advantages in an increasingly complex global supply chain environment.
About the author
eMoldino
eMoldino aims to digitalize, streamline, and transform your manufacturing and supply chain operations. We help global manufacturers who want to drive corporate innovation while maintaining the core values of collaboration and sustainability. Talk with us to learn more →
Did you enjoy reading this article?
0 / 5. Vote count: 0
Explore Our Latest Posts
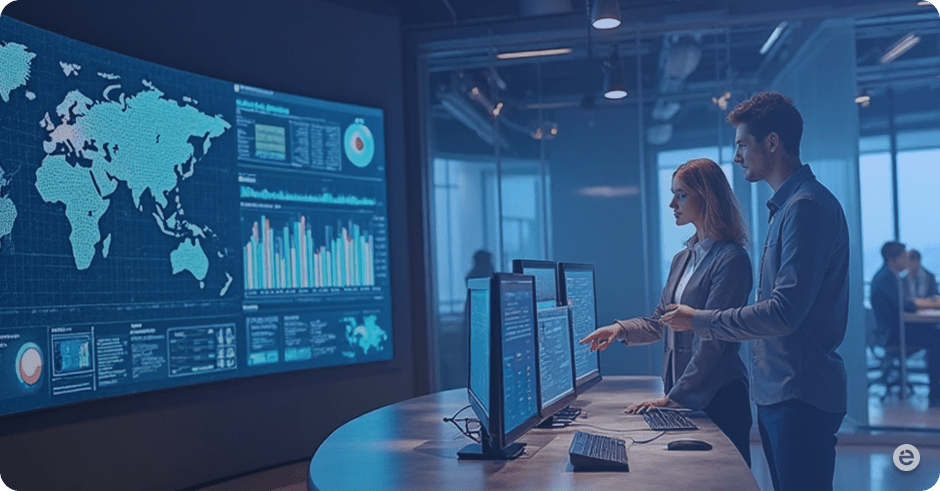

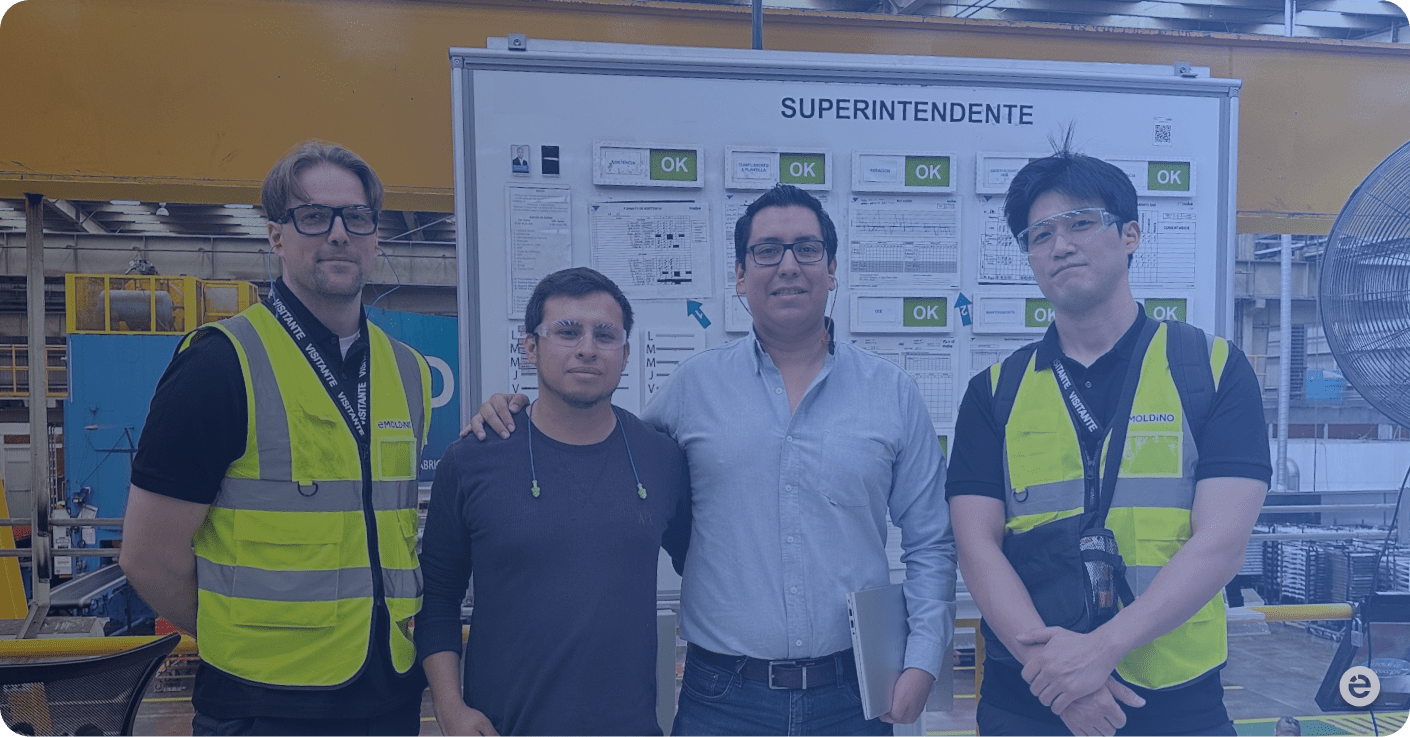
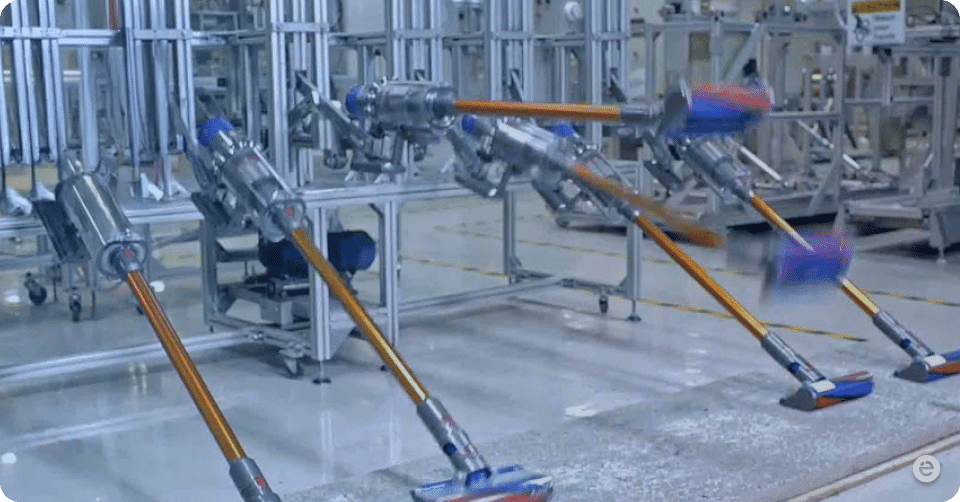
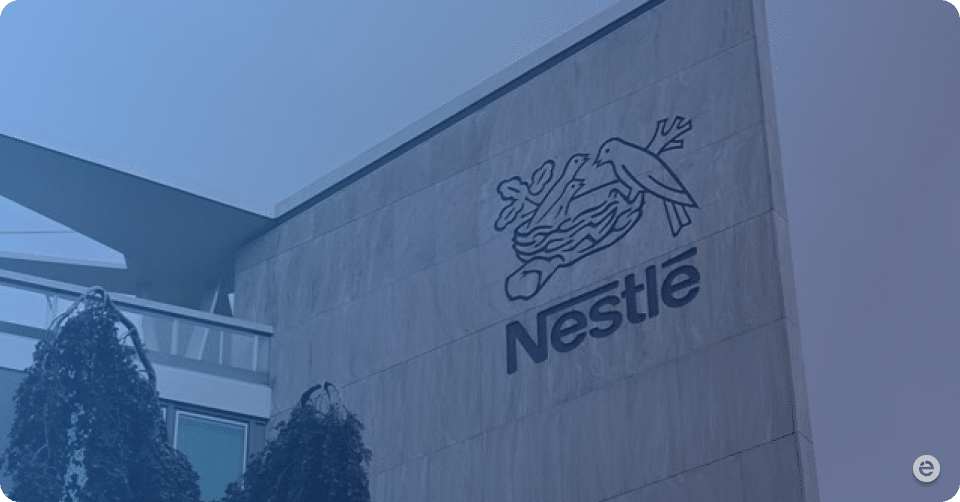
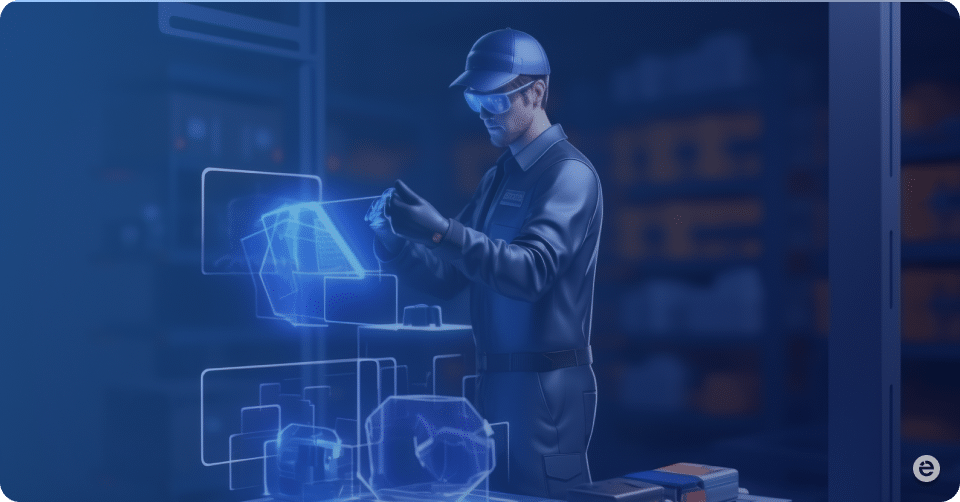
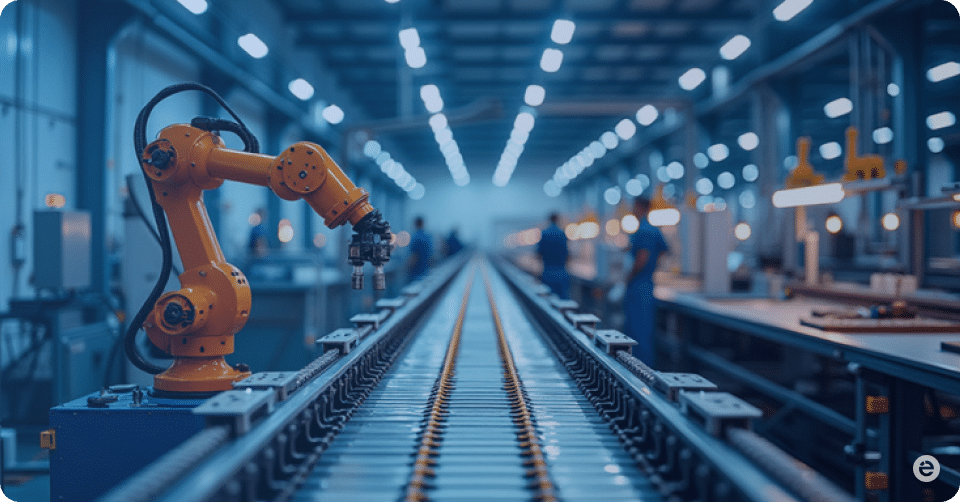
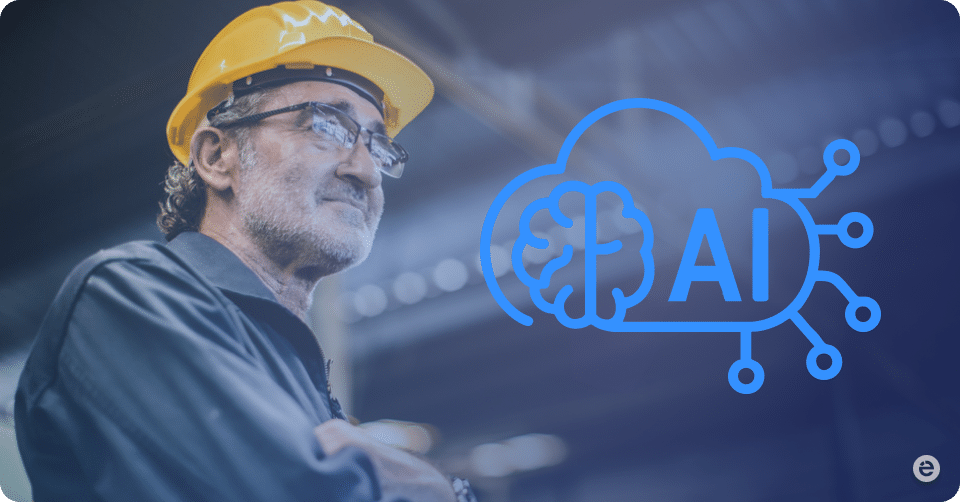
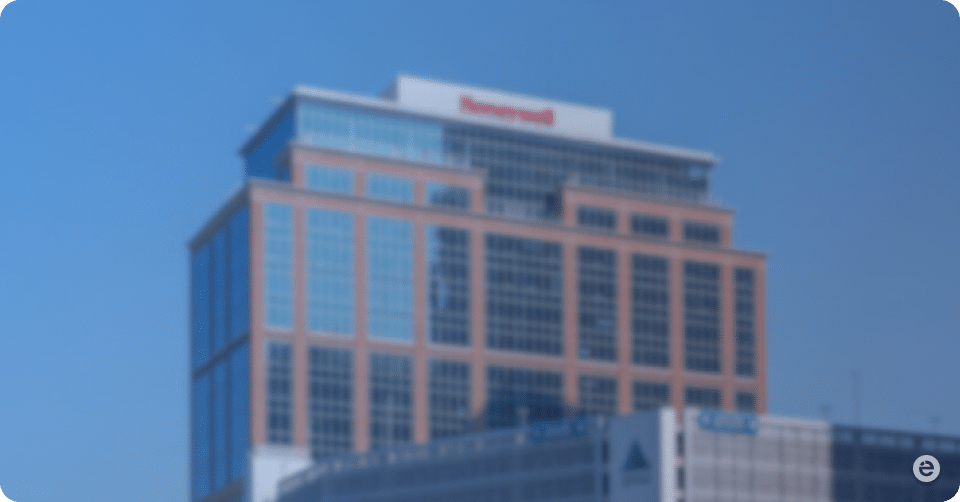
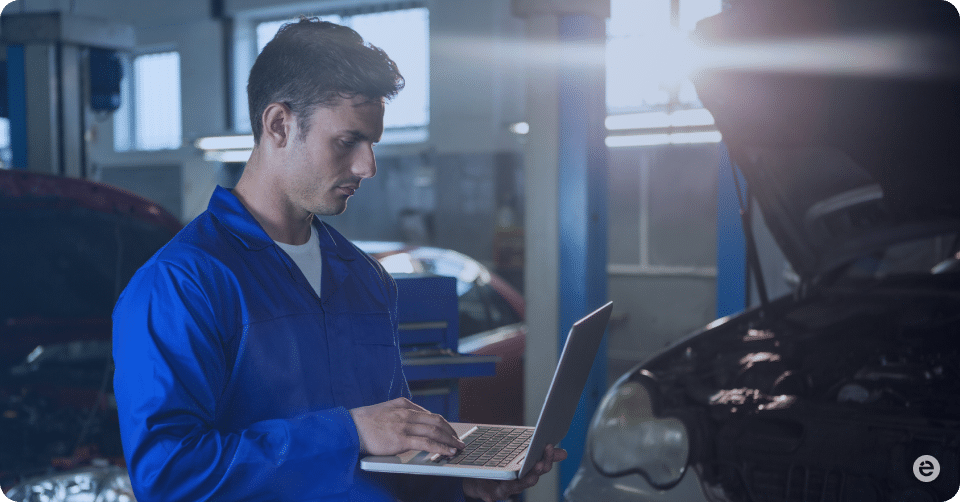