AUTOMOTIVE
2023.12.19 | Updated: 2023-12.29
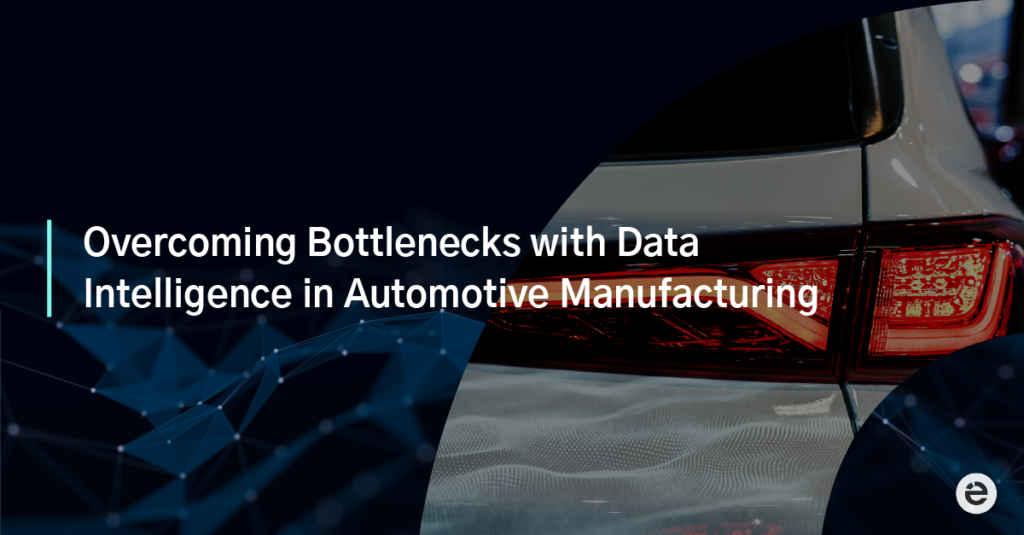
One truth remains clear: the automotive industry is always on the move. While this dynamism is exhilarating, it brings its own set of challenges, notably the infamous production bottlenecks. These have been accentuated by factors ranging from lack of automation to equipment downtime. Recent global events, such as the Covid-19 pandemic and the volatility of raw material and energy costs, further exacerbate these challenges. Amid these challenges, the untapped potential of outsourced tooling data emerges as a silver lining. By tapping into this data and leveraging analytics, managers can identify issues earlier and refine their production processes, paving the way for more efficient manufacturing operations.
Harnessing Automation and Digitalization
Only 12% of firms act upon their data-driven insights automatically.
The automotive industry’s efficiency often gets hampered when it leans heavily on manual processes. A prime example is the transfer of data from one system to another. Reliance on human intervention can lead to errors and slow down essential functions, creating holdups in production. Here’s where modern tooling digitalization platforms come into play, propelling automotive enterprises into the age of automation and digitalization. Such platforms prioritize real-time, automated data collection and processing. Their value becomes evident when they bring underutilized data into the spotlight – like real-time tooling performance metrics, production figures from specific shifts, and indicators for predictive maintenance. These insights, once standardized, can be transformative for Original Equipment Manufacturers (OEMs), providing them with actionable strategies to:
- Optimize production schedules.
- Enhance equipment lifespan.
- Improve quality control.
- Ensure efficient resource allocation.
Navigating the Data Deluge: From Raw Data to Actionable Insights
A BCG-WEF survey shows that only 17% of executives claim they capture the full value of data.
Effective forecasting is the cornerstone of outsourced manufacturing. In the automotive realm, OEMs rely on suppliers for essential parts and components for vehicle assembly. Miscalculating demand creates a ripple effect: underestimation can lead to production bottlenecks, while overestimation can lead to excess inventory and missed orders. The resultant customer dissatisfaction and profitability impacts can be substantial. A recurrent challenge in the industry is a mismatch between parts ordered and actual output, a problem frequently rooted in inadequate insights into supplier capacities. Such misalignments culminate in production delays and challenges in meeting customer requirements.The solution? Predictive analytics. These modern platforms harness sophisticated algorithms, poring over historical and present data to pinpoint potential supply chain hiccups. By doing so, manufacturers can proactively address and avert capacity issues, ensuring that production aligns closely with genuine demand. With the digitization of tooling, OEMs gain a real-time window into supplier capacities. These insights garnered from advanced analytics, enable OEMs to finetune demand forecasts, detect production barriers, and judiciously distribute parts across suppliers. Real-time analytics sheds light on which suppliers have room to ramp up production and which ones are nearing their limits. By scrutinizing individual production assets and juxtaposing them against current and future demand metrics, OEMs can strategically navigate and react to abrupt demand shifts.
Drowning in Data, Starving for Insights
According to Forrester, between 60% and 73% of all data within an enterprise goes unused for analytics.
Tooling downtimes – often due to overuse or inadequate maintenance – represent a significant operational challenge in manufacturing. These unexpected halts, whether from tooling malfunctions or supply chain interruptions, have considerable financial implications. Recent metrics from the automotive sector underscore the severity of the issue, with the financial toll of an hour’s downtime estimated at an alarming $2 million.
The answer to this pressing challenge is predictive maintenance. This innovative system leverages tooling historical data to generate insights beyond the capabilities of traditional methods. Through advanced analytics, firms can discern patterns leading up to tooling failures and proactively intervene—averting the impending malfunction or promptly addressing it—thereby reducing downtime.
Continuous monitoring of toolings allows these systems to pinpoint performance anomalies. For instance, by monitoring vibration patterns, managers can discern potential faults early. Upon detecting deviations, the system swiftly alerts personnel through user-friendly dashboards, enabling swift intervention. With this real-time intelligence, maintenance teams can plan requisite repairs, maintenance, or corrective strategies to preclude further degradation or failure.
Notably, McKinsey’s research affirms the efficacy of this approach. According to their studies, predictive maintenance curtails machine downtime by a significant 30 to 50 percent while concurrently extending its lifespan by 20 to 40 percent.
The Imperative of Data Intelligence in Automotive Manufacturing
Today, the automotive sector is poised at the point of a transformative shift driven predominantly by the burgeoning data ecosystem. Daily data generation provides an unprecedented opportunity, awaiting harnessing, to refine operational processes, diagnose inefficiencies, and predict forthcoming impediments.
It’s crucial to note that the prevalent bottleneck challenges in outsourced automotive production are navigable. Advanced tooling digitalization solutions are pivotal allies, enabling manufacturers to tackle these issues with precision and confidence. As the automotive industry persists in its trajectory towards heightened interconnectivity, automation, and data reliance, pioneers in adaptation and innovation will unequivocally set the industry’s pace.
Read our case studies and articles to learn more about how our tooling digitalization technology revolutionizes the automotive industry.
Explore Our Related Posts
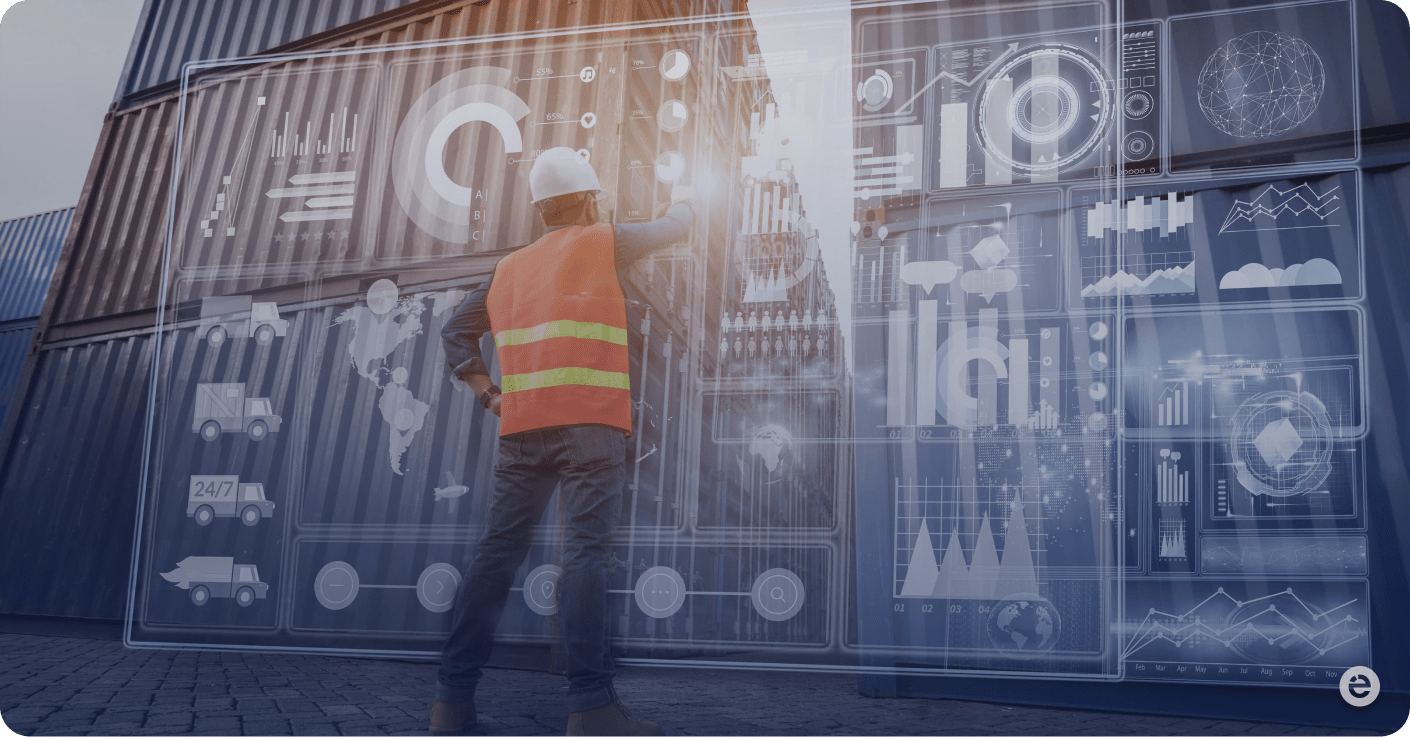
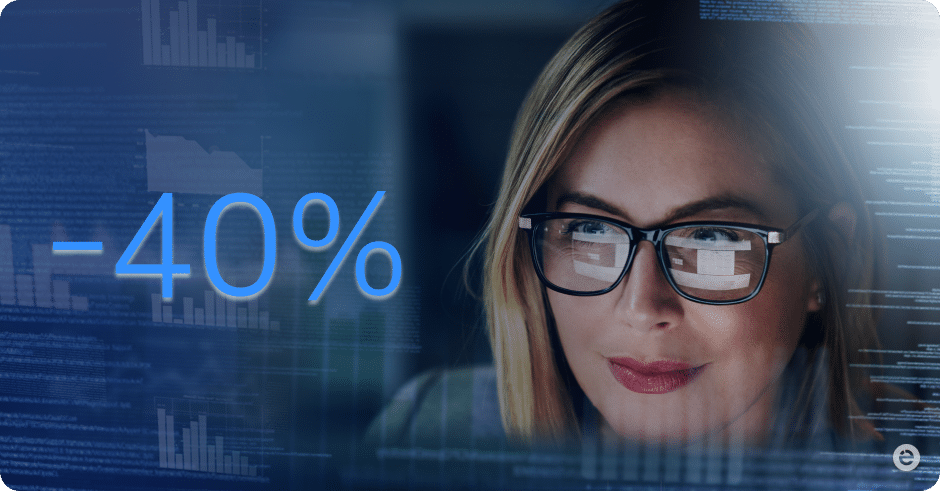

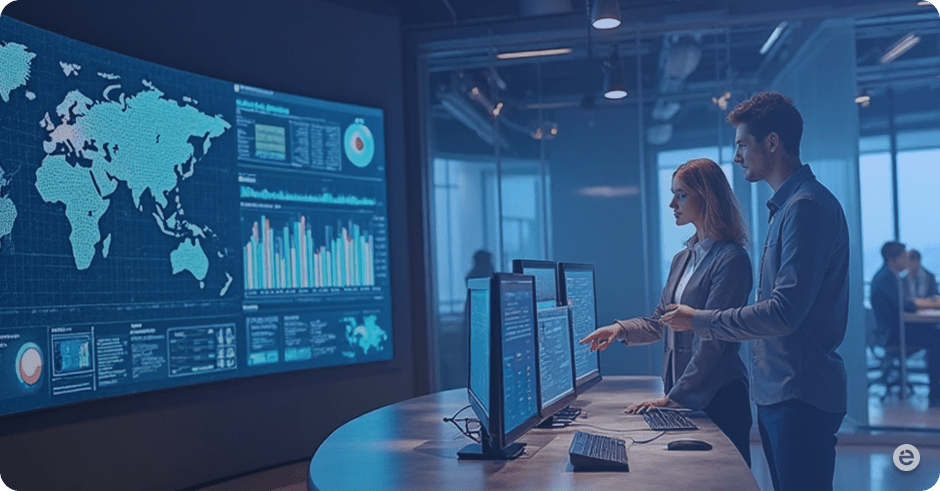

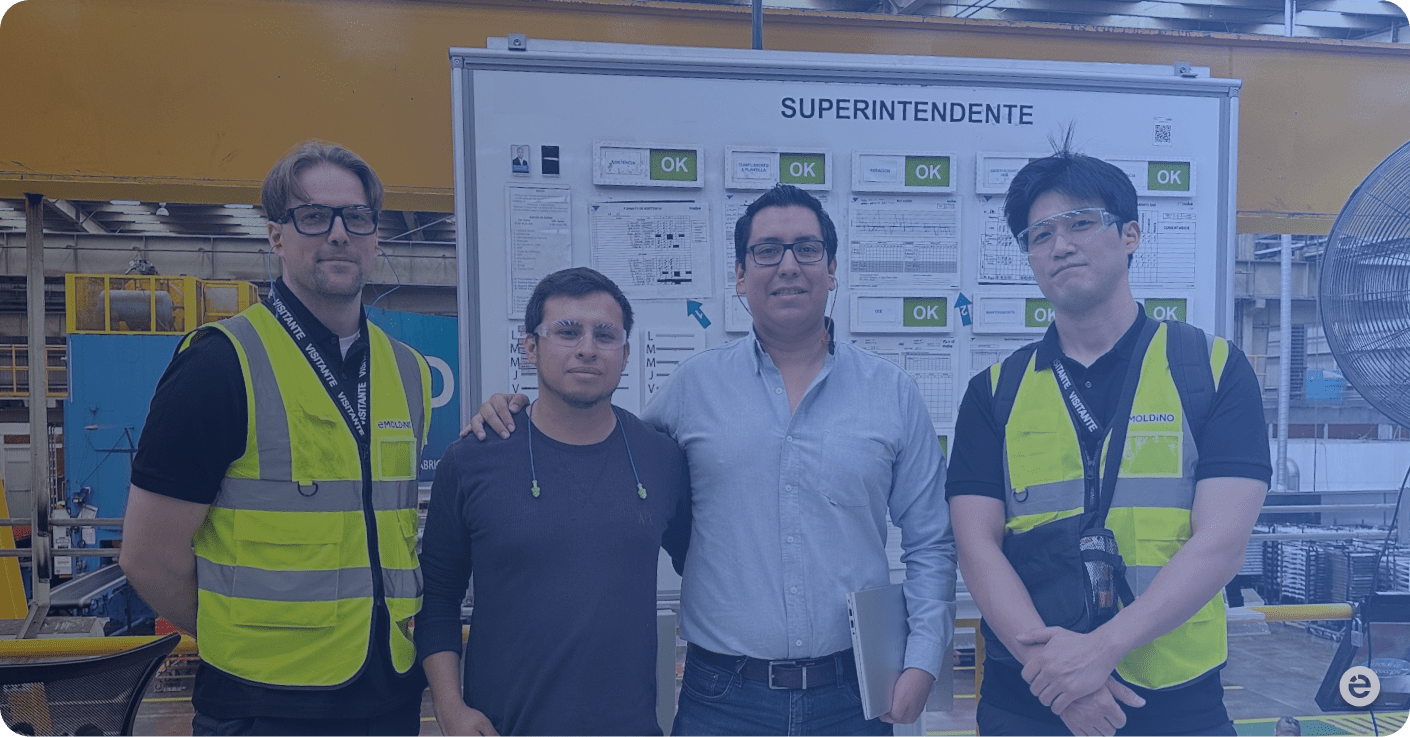
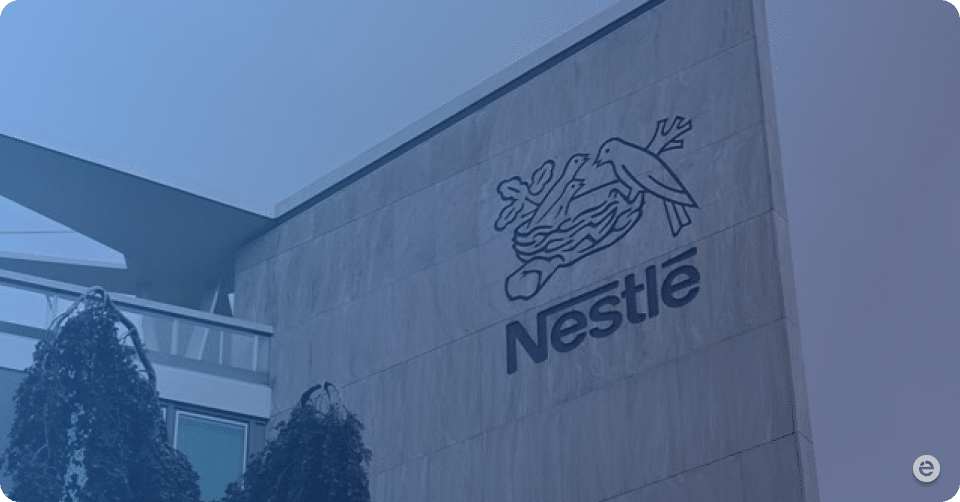
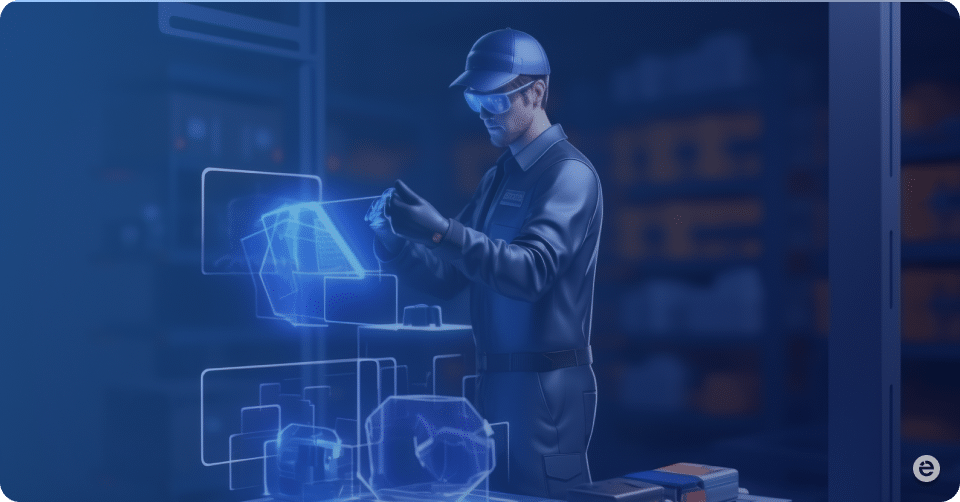
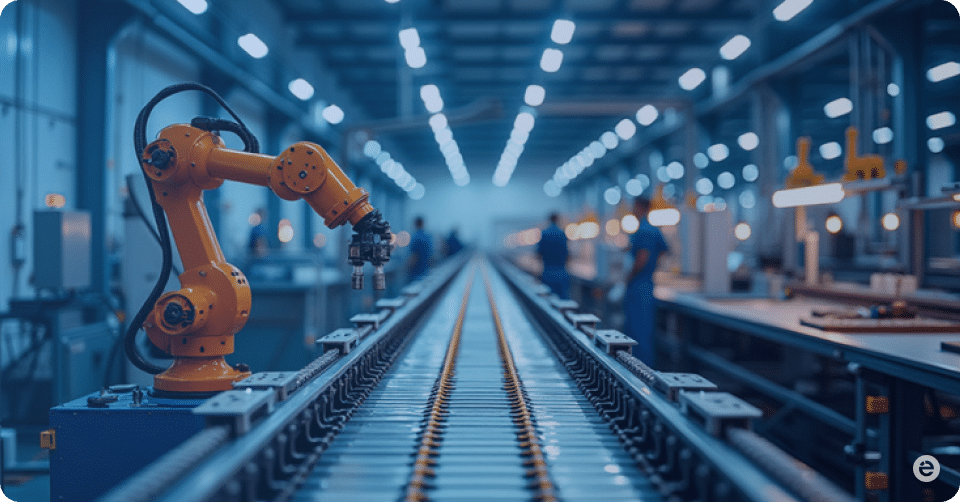
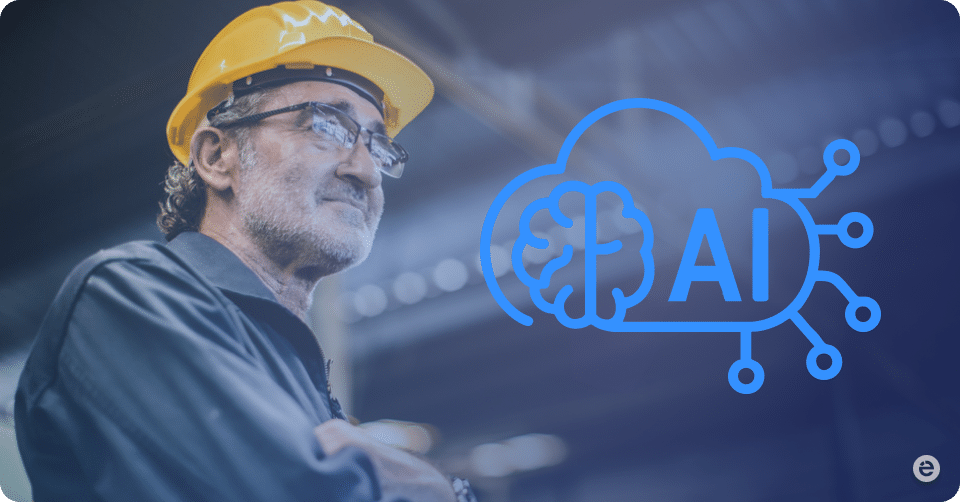
I couldn’t resist commenting. Very well written!