Introduction
In outsourced manufacturing, managing scrap rates is essential for sustaining profitability and operational efficiency. High scrap rates escalate costs and highlight inefficiencies that compromise product quality, capacity, and profitability. How can digital technologies play a critical role in reducing scrap rates, enhancing operational visibility, and improving manufacturing efficiency?
The Role of Tooling Digitalization in Scrap Reduction
Digital tools are essential in reducing scrap rates across manufacturing sectors. eMoldino’s IoT sensors play a pivotal role by enabling real-time monitoring and adjustments of production toolings. This reduces variability and minimizes defects in production processes. Digital transformations enhance decision-making, streamline production, and bolster competitiveness through strategic technology integration. According to McKinsey & Company, such integrations can lead to cost reductions of 5 to 7 percent monthly by alleviating production bottlenecks and improving overall process efficiency. (McKinsey & Company).
Case in Point
In May 2022, a leading automotive company initiated a pilot project with tooling digitalization experts, targeting production inefficiencies at two key suppliers. The focus was on High- Pressure Aluminum Die Casting(HPDC)—a process critical to their manufacturing but plagued by a high scrap rate and operational discrepancies.
In HPDC, insufficient monitoring of mold warm-up temperatures led to excessive scrap rates and elevated production costs and loss of production capacity. The core challenges included:
- Insufficient Tooling Data: This meant early signs of tooling wear and impending failures went undetected.
- Low Visibility: There was a significant gap in monitoring production in real-time, making it challenging to identify when operations deviated from set parameters.
- Root Cause Analysis: The lack of detailed operational visibility hindered the ability to effectively diagnose and address the underlying causes of inefficiencies.
To address these challenges, the automotive company relied on an advanced tooling digitalization solution, with specialized sensors that monitor the exterior temperature of tooling, effectively tracking warm-up times and temperature deviations, providing:
- Enhanced Tooling Efficiency Visibility: Real-time data on tooling performance helped pinpoint efficiency losses and potential improvements.
- Capacity and Quality Monitoring: Continuous monitoring of production capacity and part quality ensured deviations were caught and corrected swiftly, reducing the possibility of scrap.
- Data-Driven Insights: The integration of comprehensive tooling data analytics facilitated proactive maintenance and operational adjustments, reducing downtime and enhancing output quality.
Implementing the advanced tooling digitalization solution revealed that daily temperature fluctuations cost 5 minutes of production daily. Although these fluctuations accounted for only 0.3% of the production cycle, they produced 4,181 defective parts per tool annually, from 1,200,000 parts. Financially, this translated into a significant cost, with each defective part costing $5, cumulatively amounting to $20,906 lost per tool each year due to defective parts. Across 3,000 tools, this issue culminated in a combined annual loss of $62,718,000.
The pilot achieved substantial cost savings by curtailing waste and reinforced the value of real-time data monitoring in streamlining manufacturing processes.
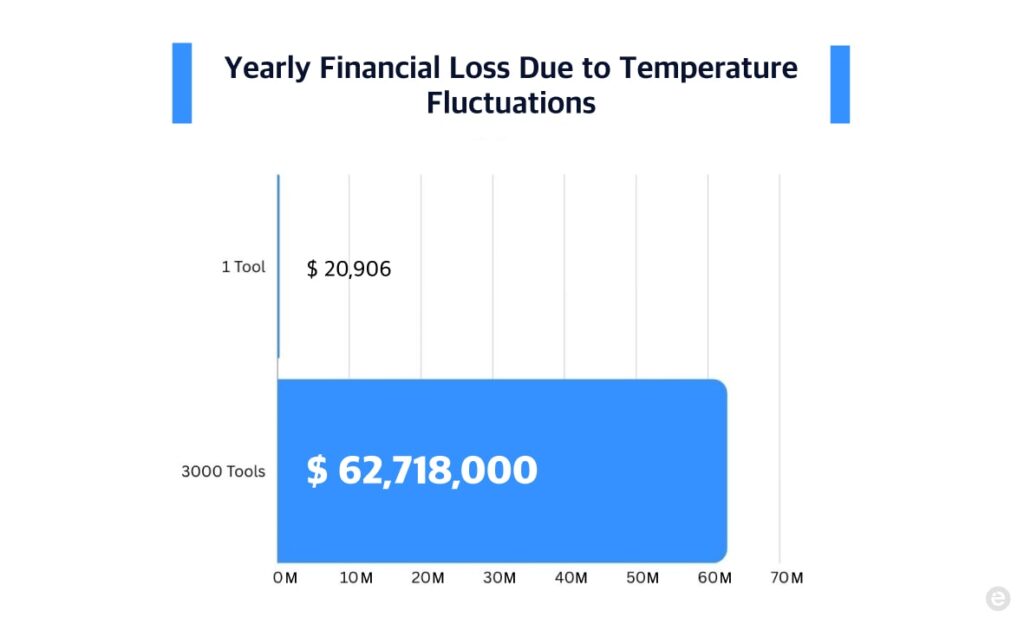
Conclusion
Forward-thinking manufacturing leaders do not merely see scrap rates and process inefficiencies as obstacles to be overcome; they view these challenges as opportunities for substantial enhancement and strategic differentiation. Rather than simply mitigating inefficiencies, visionary companies leverage these times to implement profound digital transformations. Is your company ready to embrace tooling digitalization and real-time data analytics to enhance its operational resilience?
About the author
eMoldino
eMoldino aims to digitalize, streamline, and transform your manufacturing and supply chain operations. We help global manufacturers who want to drive corporate innovation while maintaining the core values of collaboration and sustainability. Talk with us to learn more →
Did you enjoy reading this article?
4 / 5. Vote count: 1
Explore Our Latest Posts
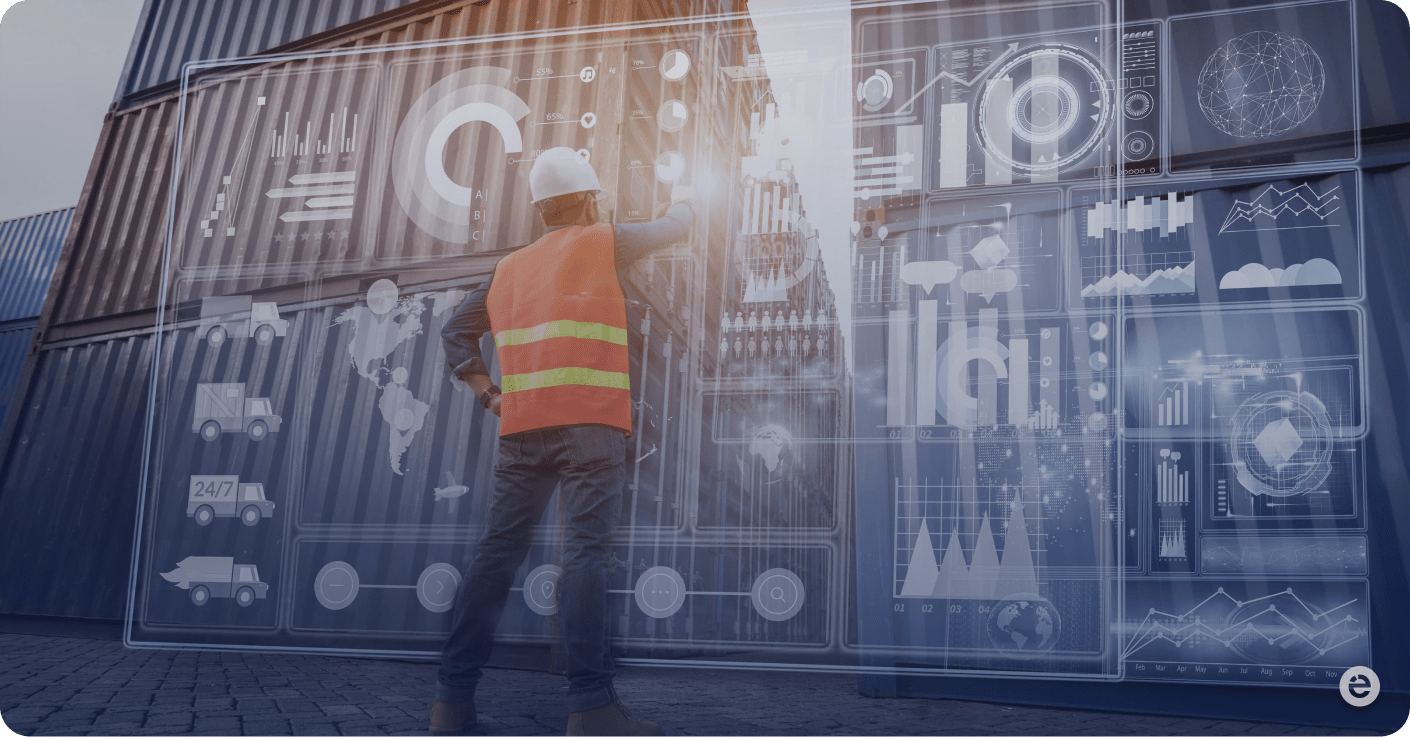
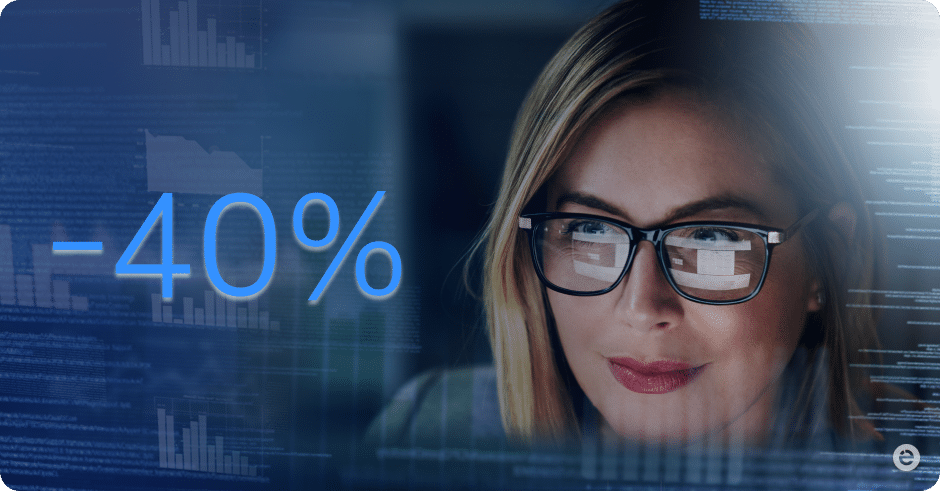
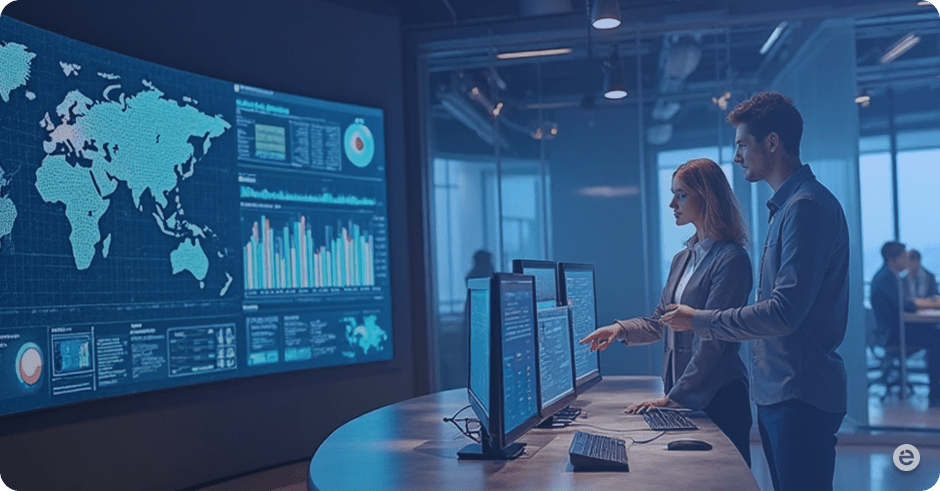

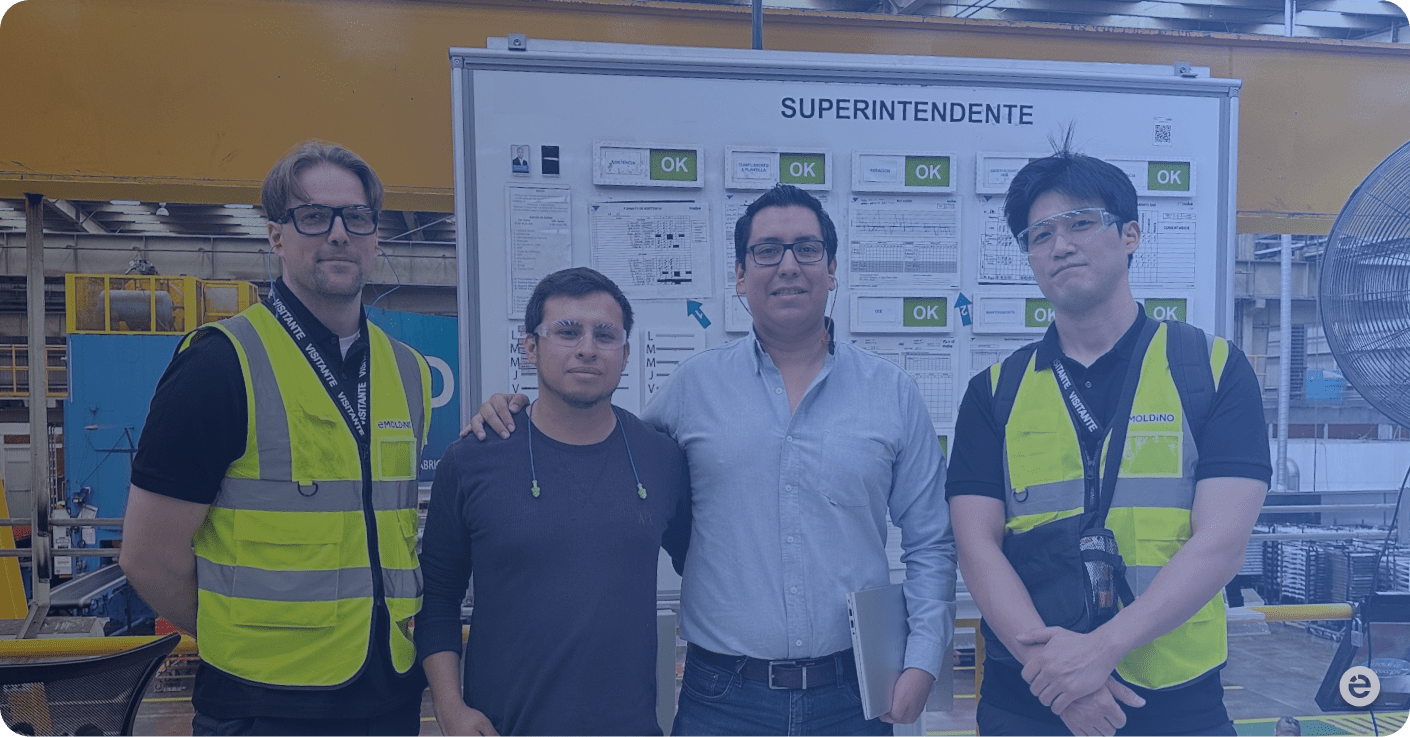
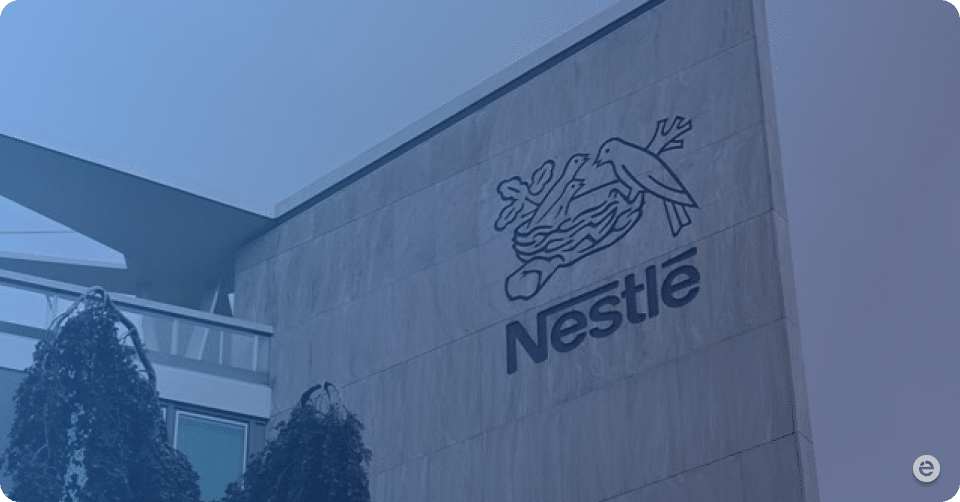
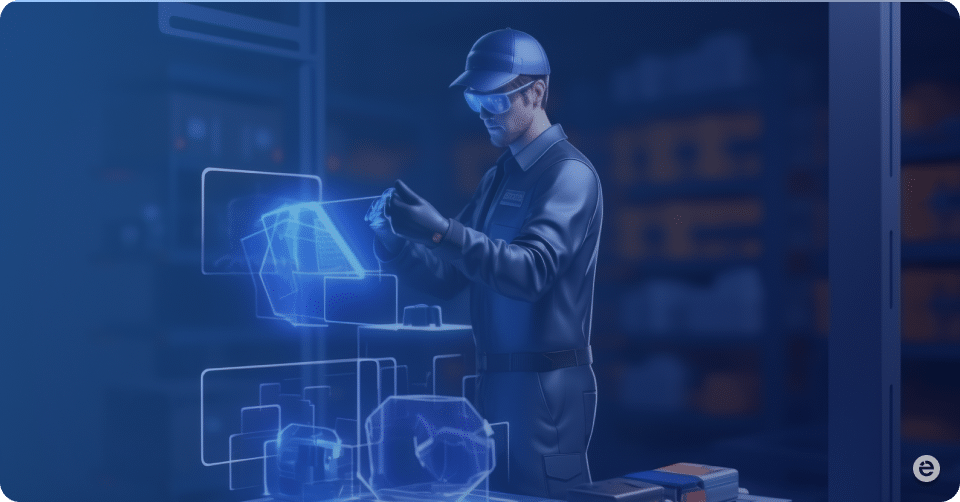
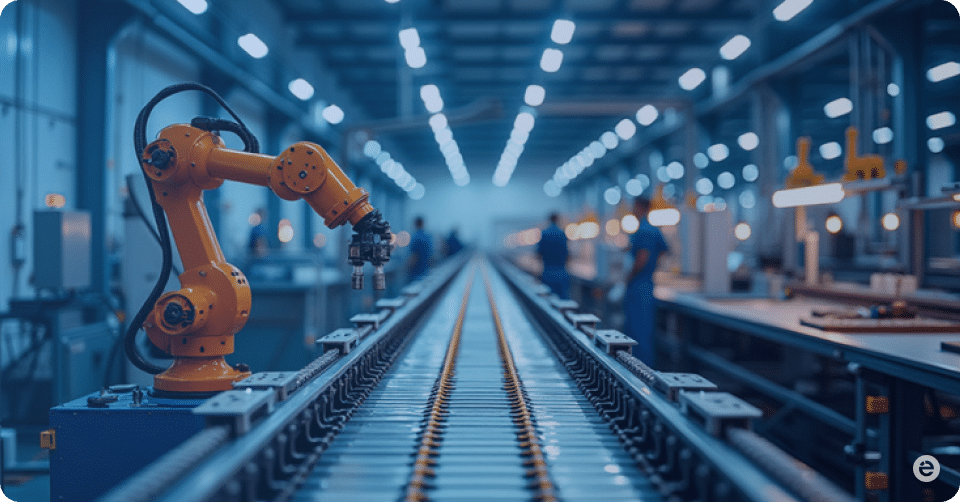
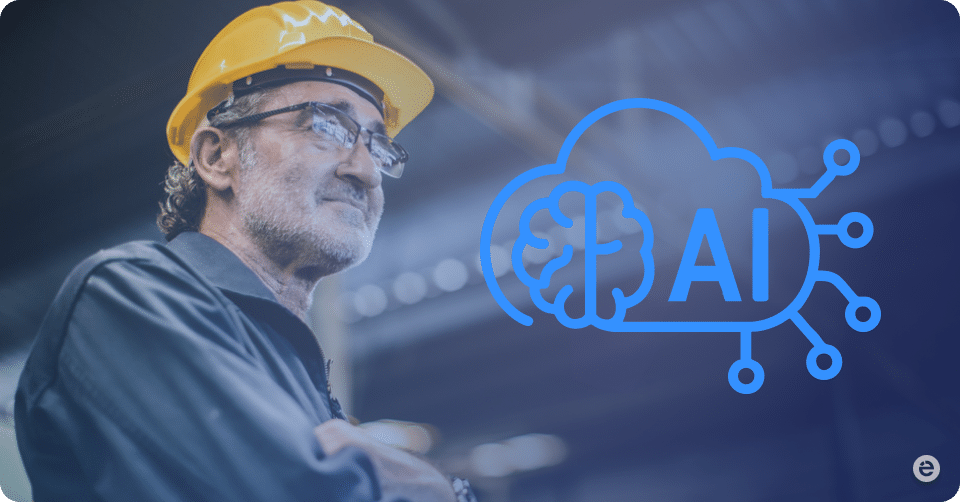
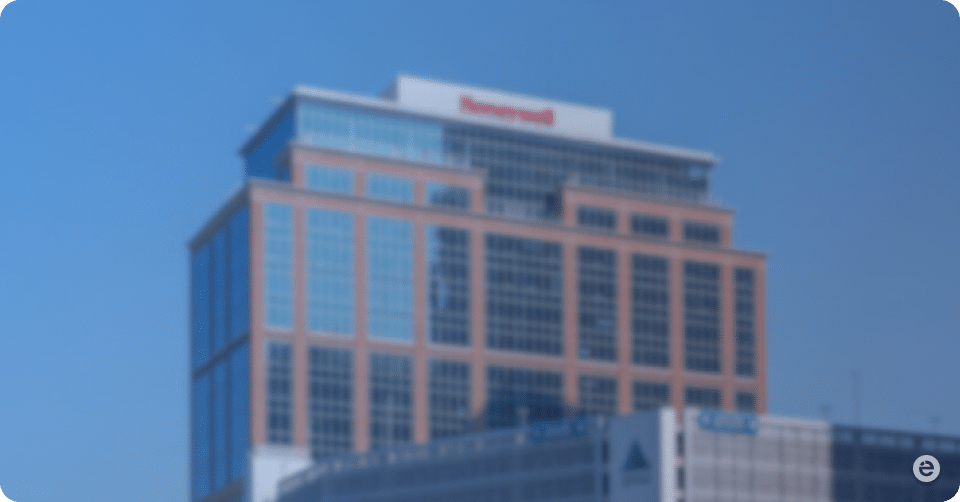
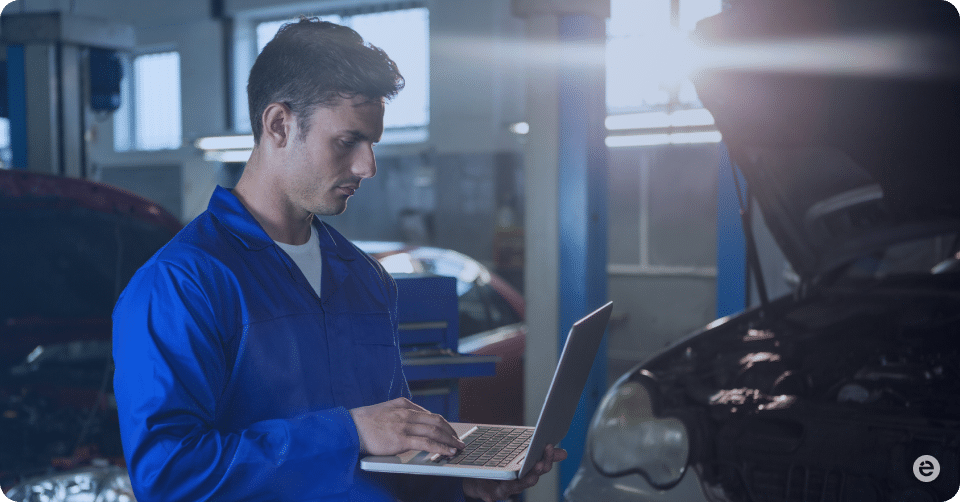