AUTOMOCIÓN
2023.12.19 | Actualizado: 2023-12.29
Convergencia de la digitalización de herramientas y la fabricación sostenible
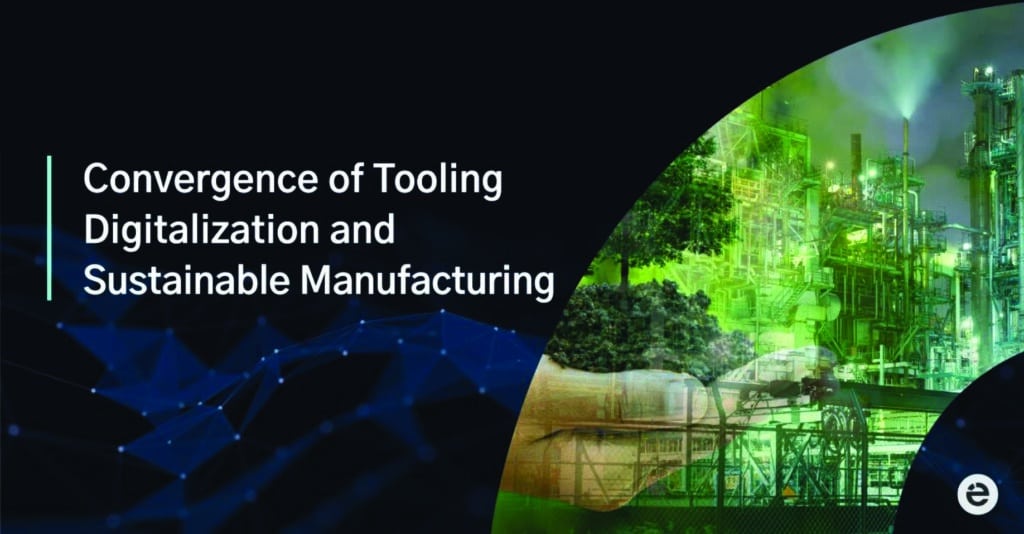
Con la creciente preocupación por los problemas medioambientales, varias industrias, incluido el sector de la automoción, están dando prioridad a la fabricación sostenible para reducir su huella de carbono y mantener la competitividad. Un enfoque prometedor que está cobrando impulso es la convergencia de la digitalización de las herramientas con las prácticas sostenibles. Este cambio tiene implicaciones significativas para una industria que se esfuerza por mejorar sus iniciativas de sostenibilidad. Este artículo explora el potencial transformador de dicha convergencia presentando una solución de vanguardia para la industria del automóvil, que avanza hacia la excelencia operativa y un mayor compromiso con la responsabilidad medioambiental.
El poder de la convergencia: Integración de tecnología y sostenibilidad
La digitalización es un elemento esencial para fomentar un entorno de fabricación sostenible
La convergencia de la digitalización de las herramientas y la fabricación sostenible ofrece una oportunidad transformadora para la industria del automóvil. La incorporación de tecnología avanzada y digitalización se ha convertido en un factor crucial para lograr la sostenibilidad en la fabricación, fomentando la mejora de la productividad, la gestión de residuos y la ventaja competitiva. Aprovechando la analítica impulsada por IA, se pueden racionalizar los procesos, minimizar los residuos y optimizar los recursos, todo ello al tiempo que se obtiene una mayor visibilidad de las operaciones de producción. Con estos datos, las organizaciones pueden optimizar la producción y mejorar el mantenimiento predictivo, reduciendo el consumo de energía.
Para los principales fabricantes de equipos originales (OEM) que subcontratan su fabricación a proveedores de todo el mundo, la integración perfecta de sensores IoT, inteligencia artificial y análisis de datos proporciona información en tiempo real sobre el rendimiento de las herramientas subcontratadas y la eficiencia de la producción. Este enfoque basado en datos impulsa la excelencia operativa y aumenta el impacto de los esfuerzos de sostenibilidad, permitiendo la reducción de residuos, el uso preciso de materiales y el mantenimiento proactivo.
El abastecimiento responsable también emerge como un elemento crítico en la promoción de prácticas sostenibles. Los ejecutivos del sector de la automoción obtienen información valiosa sobre el rendimiento y el cumplimiento de los proveedores mediante el empleo de la digitalización de herramientas. Investigación realizada por Capgemini indica que 62% de las organizaciones automovilísticas priorizan ahora estrategias de sostenibilidad globales con objetivos y metas bien definidos, lo que subraya la creciente importancia del abastecimiento sostenible en la industria. Dar prioridad a las asociaciones con proveedores concienciados con el medio ambiente permite a las empresas automovilísticas alinear sus prácticas de abastecimiento con iniciativas de responsabilidad social y objetivos de sostenibilidad, fomentando un futuro más ecológico y socialmente responsable.
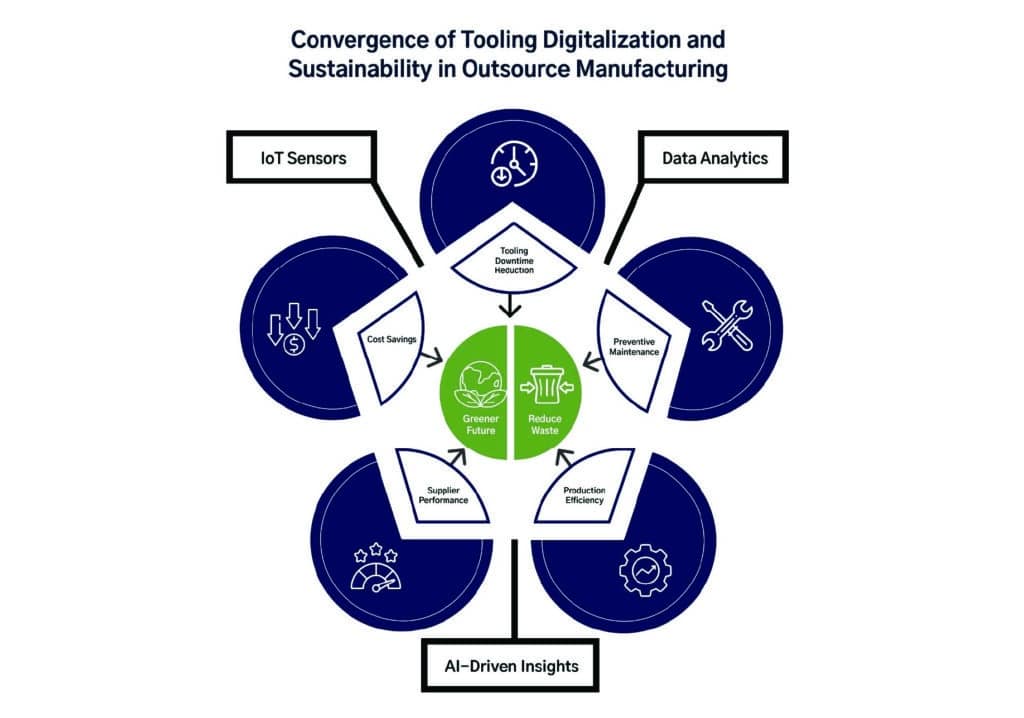
Historia real de éxito
La digitalización de las herramientas impulsa la fabricación sostenible en la industria del automóvil
Las principales empresas de automoción que adoptan este enfoque transformador ya han sido testigos de resultados cuantificables, lo que confirma la viabilidad de la sinergia entre la digitalización de herramientas y la fabricación sostenible. Una de estas empresas es una destacada multinacional alemana fabricante de piezas de automoción, que ejemplifica este éxito con avances significativos en la digitalización de herramientas y la sostenibilidad. Lograron resultados notables integrando tecnologías avanzadas y conocimientos basados en datos, optimizando las operaciones y avanzando hacia un futuro más ecológico.
Gracias a la digitalización del utillaje, el equipo de mantenimiento de la empresa obtuvo una visibilidad sin precedentes del mantenimiento preventivo, lo que les permitió disponer de datos en tiempo real y alertas oportunas para tomar medidas proactivas. Este enfoque redujo sustancialmente el tiempo de inactividad de las herramientas, mejorando la productividad y el ahorro de costes. Además, el enfoque de mantenimiento proactivo de la empresa condujo a una reducción sustancial de los costes relacionados con problemas de calidad, ya que las intervenciones oportunas y la preservación de la integridad del utillaje redujeron los defectos de los productos y las costosas repeticiones, elevando la calidad general del producto. La empresa pudo perfeccionar sus procesos de fabricación analizando datos históricos y tendencias de rendimiento, reduciendo la probabilidad de errores y defectos en la línea de producción. Este enfoque de mantenimiento basado en datos optimizó el rendimiento de las herramientas y contribuyó a la reducción de residuos y recursos, alineándose perfectamente con la gestión responsable de residuos y los objetivos de sostenibilidad más amplios.
Además, el compromiso de la empresa con la digitalización de las herramientas se tradujo en una mayor eficiencia energética durante los procesos de fabricación. Gracias a las funciones de mantenimiento predictivo de la solución, los utillajes se mantienen y revisan adecuadamente con antelación, evitando averías. Este enfoque proactivo minimiza los tiempos de inactividad imprevistos, que de otro modo provocarían un derroche de energía durante los periodos de inactividad. Como resultado, la empresa consiguió reducir el consumo de energía y las emisiones de carbono asociadas, contribuyendo significativamente a sus esfuerzos por minimizar su huella de carbono. Al liberar todo el potencial de sus moldes mediante la digitalización, la empresa demostró su firme dedicación a la reducción del impacto medioambiental y a la adopción de un cambio transformador, consolidando aún más su camino hacia la fabricación sostenible.
Explore nuestras publicaciones relacionadas
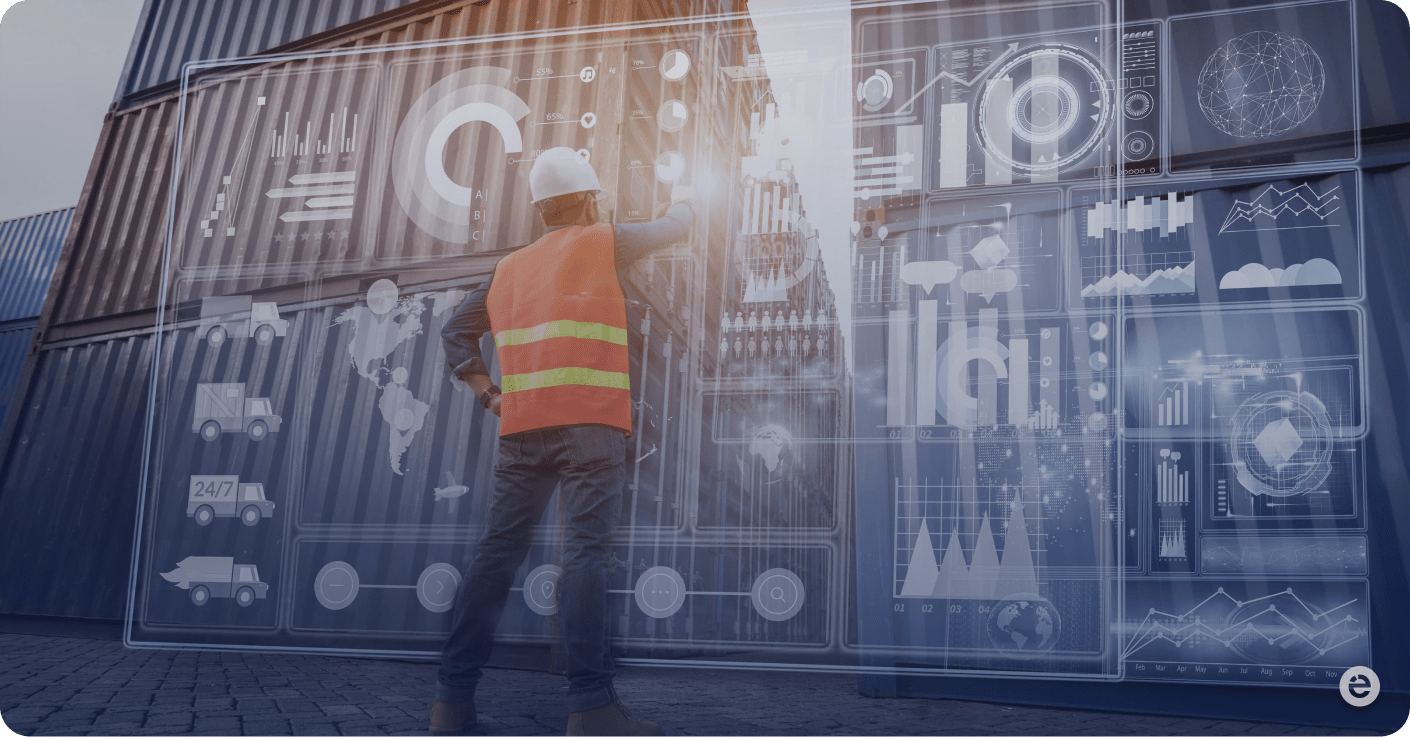
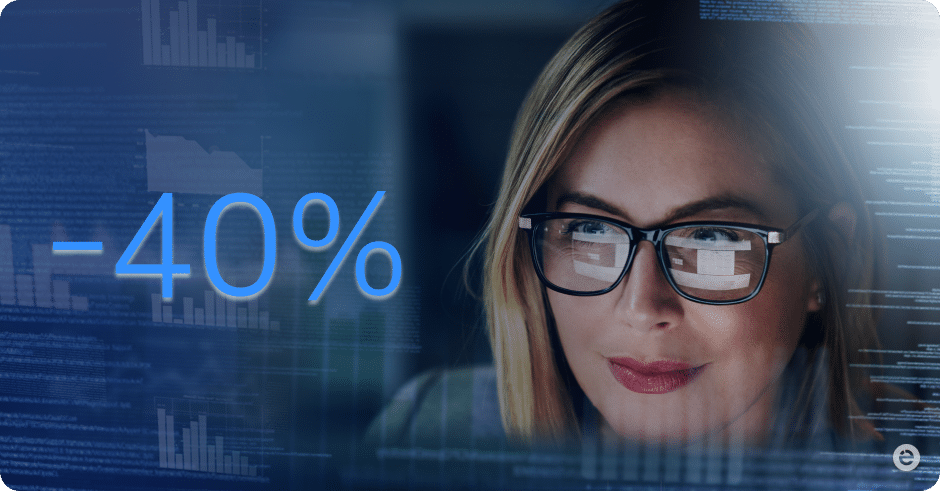
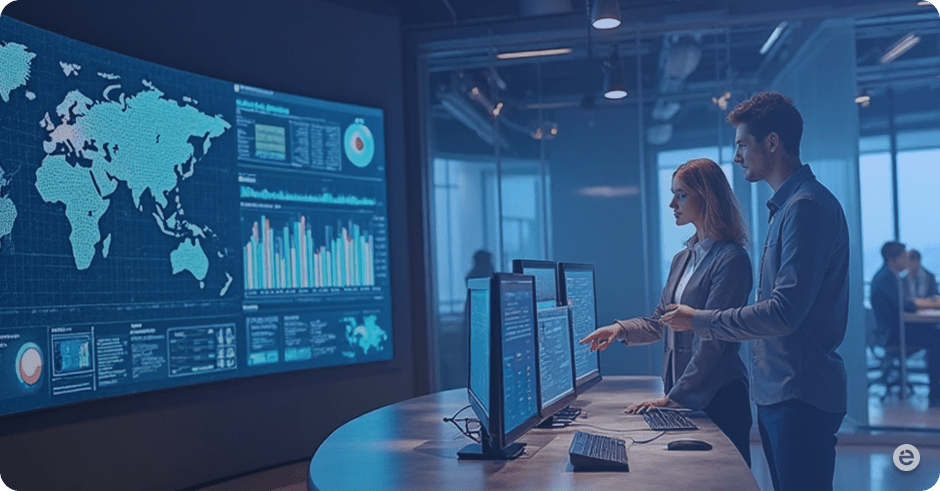

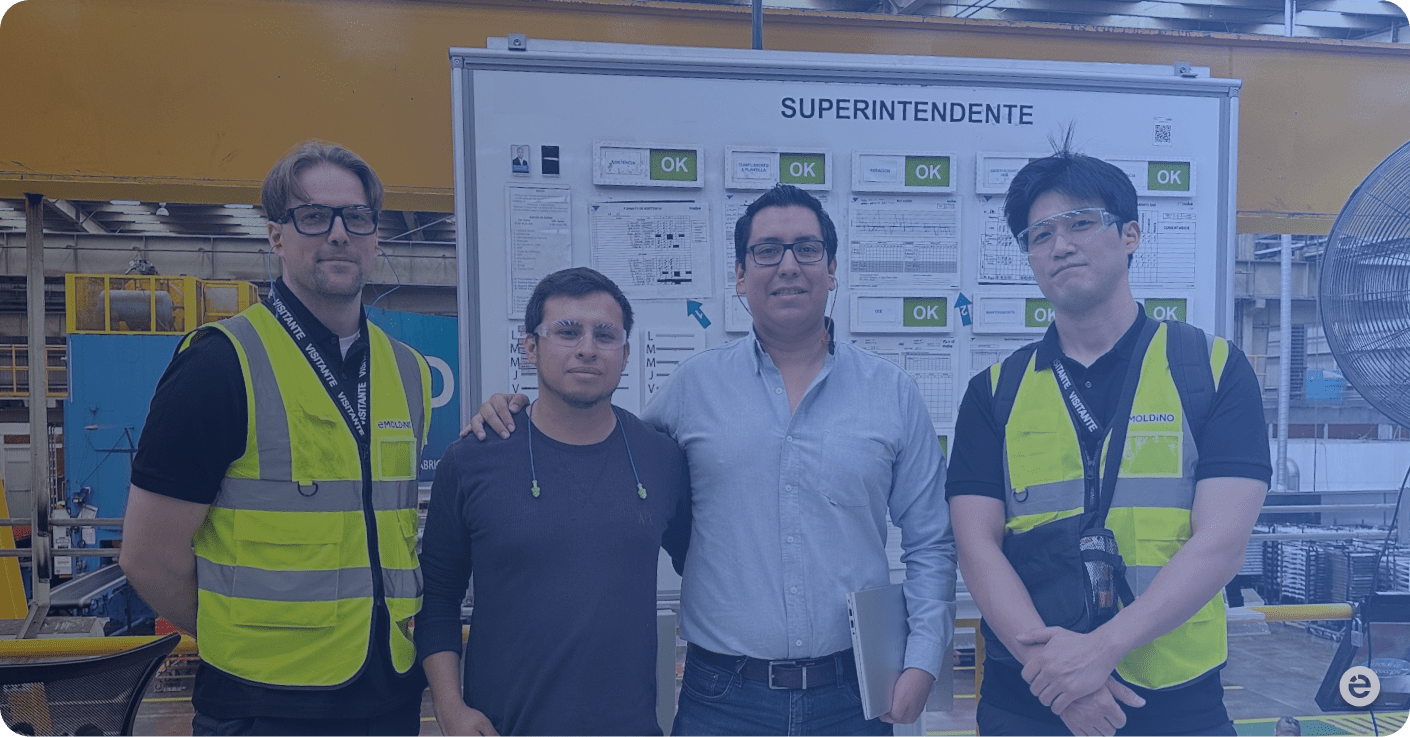
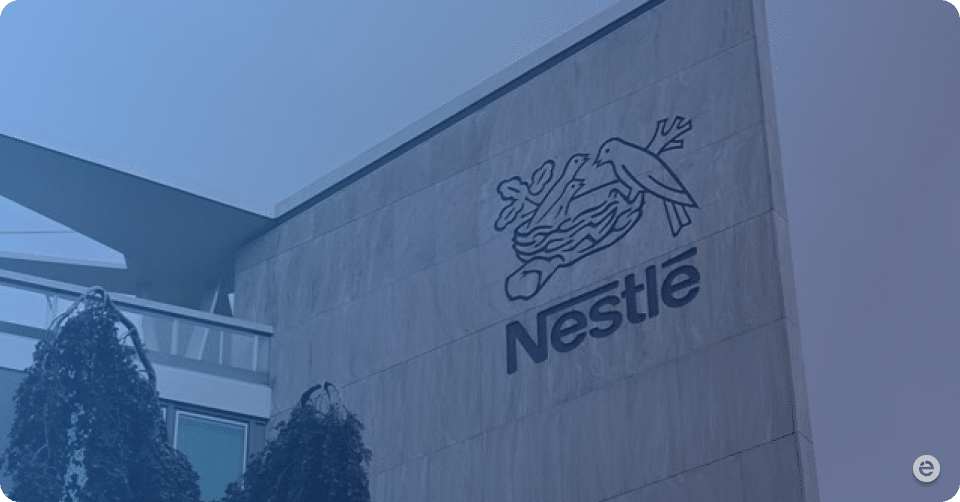
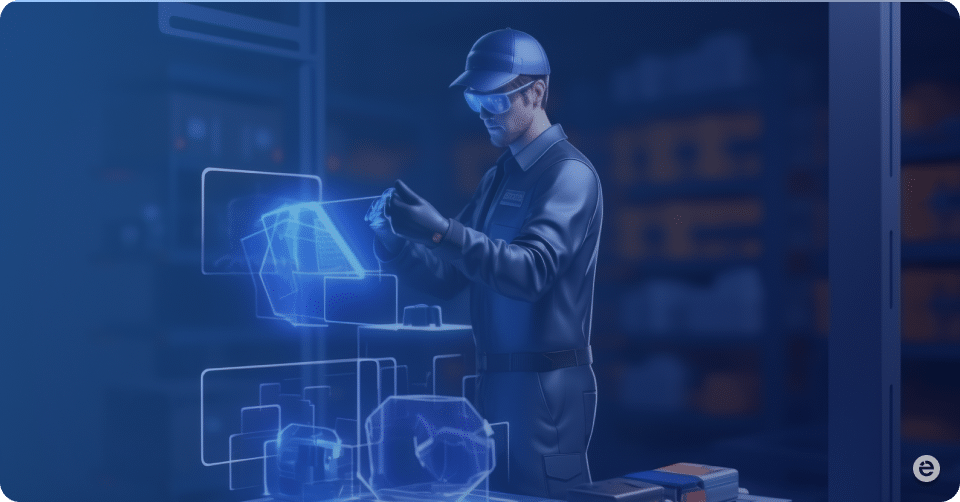
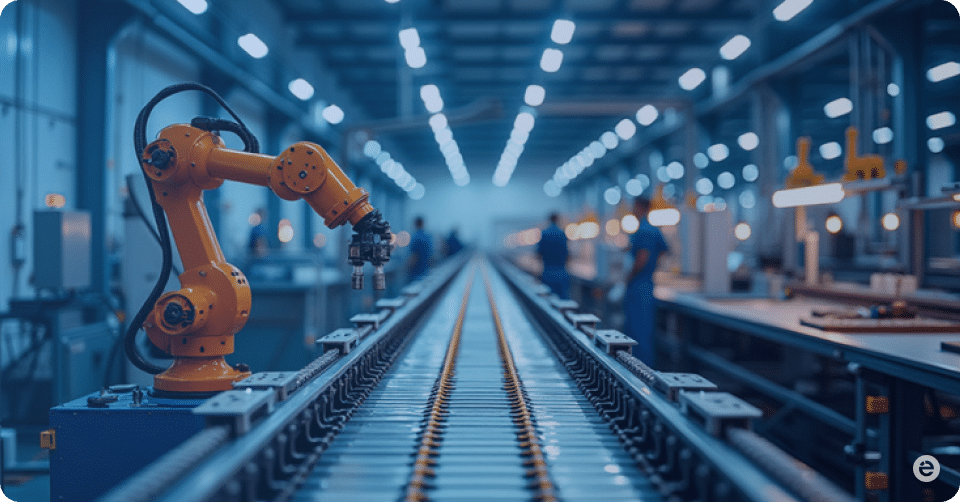