Introducción
En la fabricación externalizada, la gestión de la chatarra es esencial para mantener la rentabilidad y la eficacia operativa. Unas tasas de residuos elevadas incrementan los costes y ponen de manifiesto ineficiencias que comprometen la calidad del producto, la capacidad y la rentabilidad. Cómo pueden las tecnologías digitales desempeñar un papel fundamental en la reducción de las tasas de residuos, la mejora de la visibilidad operativa y la mejora de la eficiencia de la fabricación?
El papel de la digitalización de herramientas en la reducción de la chatarra
Los sensores IoT de eMoldino desempeñan un papel fundamental al permitir la supervisión y los ajustes en tiempo real de las herramientas de producción. Esto reduce la variabilidad y minimiza los defectos en los procesos de producción. Las transformaciones digitales mejoran toma de decisiones, racionalizar la produccióny reforzar competitividad mediante la integración estratégica de la tecnología. Según McKinsey & Company, estas integraciones pueden dar lugar a reducciones de costes de entre el 5 y el 7 por ciento mensual al aliviar los cuellos de botella de la producción y mejorar la eficiencia general de los procesos. (McKinsey & Company).
Un ejemplo
En mayo de 2022, una empresa líder del sector de la automoción inició un proyecto piloto con expertos en digitalización de utillajes, dirigido a ineficiencias de producción en dos proveedores clave. La atención se centró en la fundición inyectada de aluminio a alta presión (HPDC), un proceso crítico para su fabricación pero plagado de un alto índice de desechos y discrepancias operativas.
En HPDC, la supervisión insuficiente de las temperaturas de calentamiento de los moldes provocó un índice excesivo de piezas desechadas y elevó los costes de producción y la pérdida de capacidad productiva. Los principales retos eran:
- Datos de utillaje insuficientes: Esto significaba que no se detectaban los primeros signos de desgaste de las herramientas ni los fallos inminentes.
- Baja visibilidad: La supervisión de la producción en tiempo real presentaba importantes lagunas, lo que dificultaba la identificación de las desviaciones de las operaciones con respecto a los parámetros establecidos.
- Análisis de la causa raíz: La falta de visibilidad operativa detallada obstaculizaba la capacidad de diagnosticar y abordar eficazmente las causas subyacentes de las ineficiencias.
Para hacer frente a estos retos, la empresa de automoción confió en una solución avanzada de digitalización de utillajes, con sensores especializados que controlan la temperatura exterior de los utillajes, realizando un seguimiento eficaz de los tiempos de calentamiento y las desviaciones de temperatura, proporcionando:
- Mayor visibilidad de la eficiencia de las herramientas: Los datos en tiempo real sobre el rendimiento de las herramientas ayudaron a detectar pérdidas de eficiencia y posibles mejoras.
- Supervisión de la capacidad y la calidad: La supervisión continua de la capacidad de producción y la calidad de las piezas garantizó que las desviaciones se detectaran y corrigieran rápidamente, reduciendo la posibilidad de que se produjeran desechos.
- Información basada en datos: La integración de análisis exhaustivos de datos de herramientas facilitó el mantenimiento proactivo y los ajustes operativos, reduciendo el tiempo de inactividad y mejorando la calidad de la producción.
La implantación de la solución avanzada de digitalización de utillajes reveló que las fluctuaciones diarias de temperatura costaban 5 minutos diarios de producción. Aunque estas fluctuaciones sólo representaban 0.3% del ciclo de producción, produjeron 4.181 piezas defectuosas por herramienta anualmente, de 1.200.000 piezas. Desde el punto de vista económico, esto se tradujo en un coste significativo, ya que cada pieza defectuosa costaba $5, lo que acumulativamente ascendía a 2,5 millones de euros. $20,906 perdidas por herramienta cada año debido a piezas defectuosas. En 3.000 herramientas, este problema culminó en una pérdida anual combinada de 1.000 millones de euros. $62,718,000.
El proyecto piloto logró un importante ahorro de costes al reducir los residuos y reforzó el valor de la supervisión de datos en tiempo real para racionalizar los procesos de fabricación.
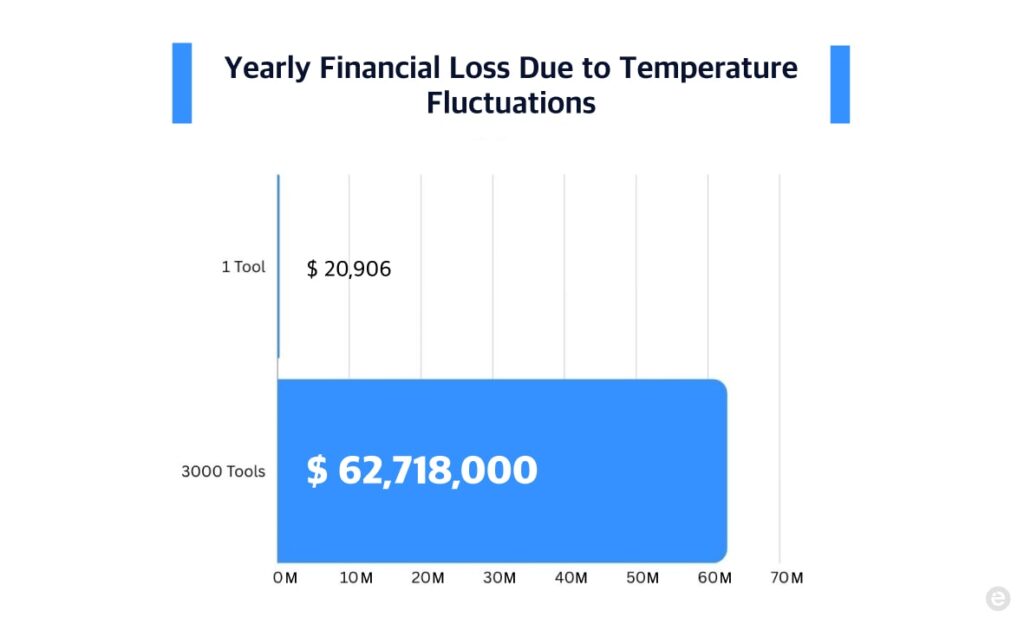
Conclusión
Los líderes manufactureros con visión de futuro no se limitan a ver las tasas de residuos y las ineficiencias de los procesos como obstáculos que hay que superar; ven estos retos como oportunidades de mejora sustancial y diferenciación estratégica. En lugar de limitarse a mitigar las ineficiencias, las empresas visionarias aprovechan estos tiempos para implementar profundas transformaciones digitales. ¿Está preparada su empresa para adoptar la digitalización de herramientas y el análisis de datos en tiempo real para mejorar su resistencia operativa?
Sobre el autor
eMoldino
El objetivo de eMoldino es digitalizar, agilizar y transformar sus operaciones de fabricación y cadena de suministro. Ayudamos a los fabricantes globales que desean impulsar la innovación corporativa manteniendo los valores fundamentales de colaboración y sostenibilidad. Hable con nosotros para saber más →
¿Le ha gustado leer este artículo?
4 / 5. Recuento de votos: 1
Explore nuestras últimas publicaciones
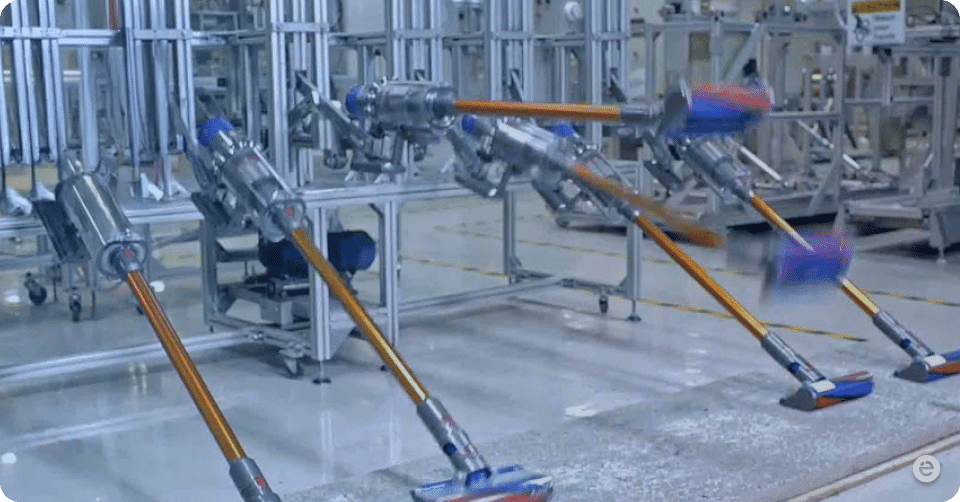
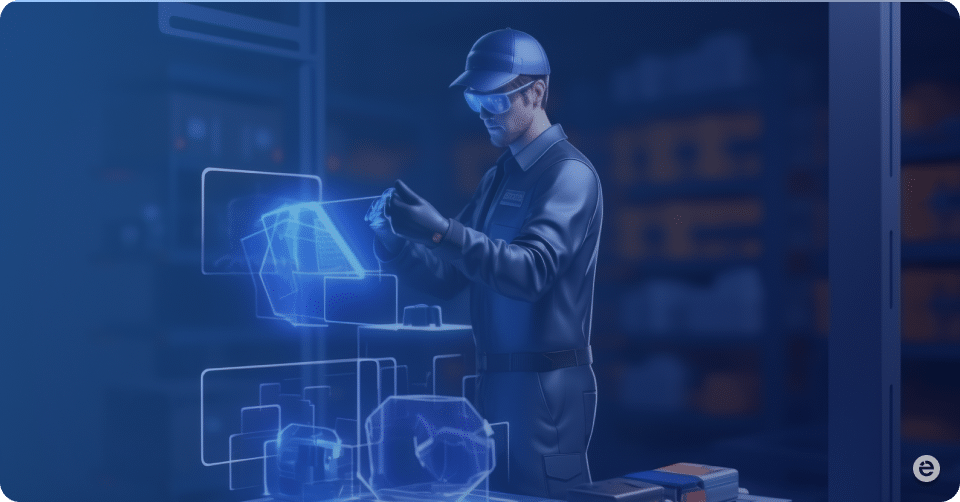
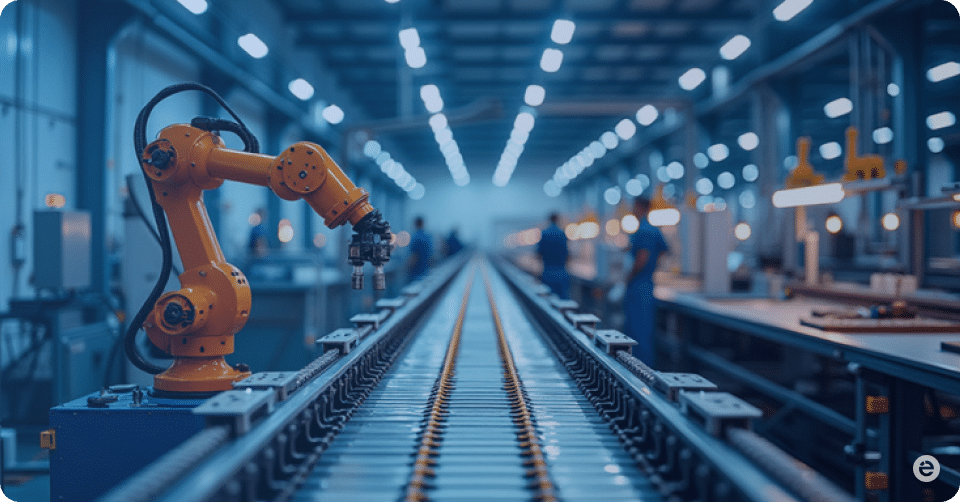
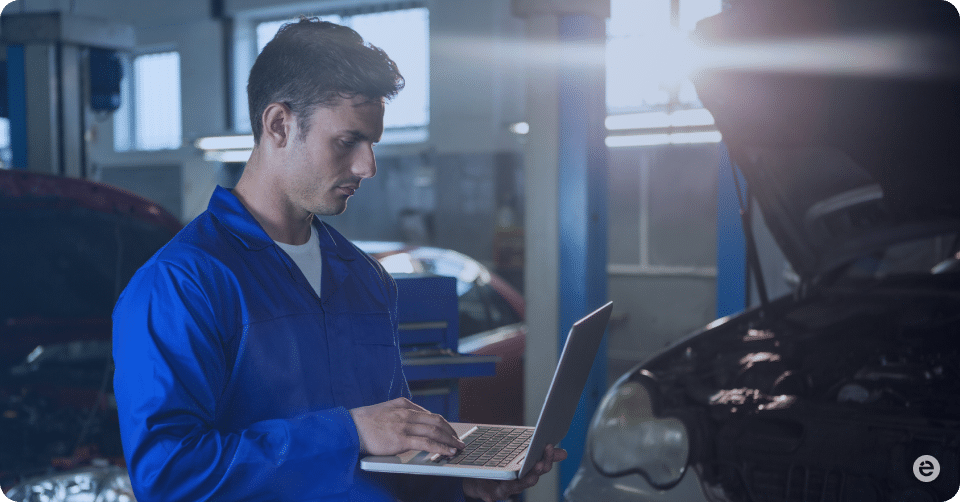
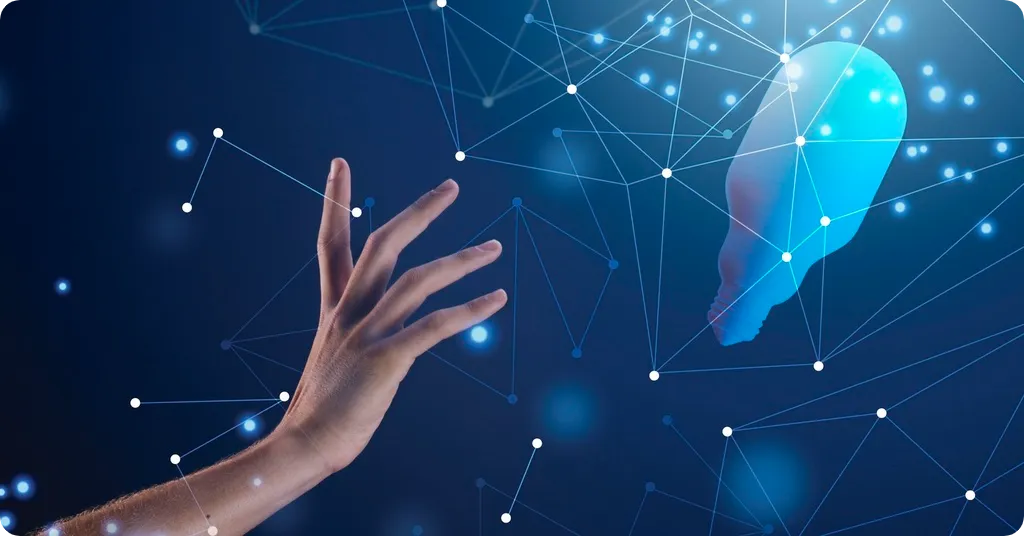
Eaton ahorra millones con la solución de digitalización de herramientas de eMoldino
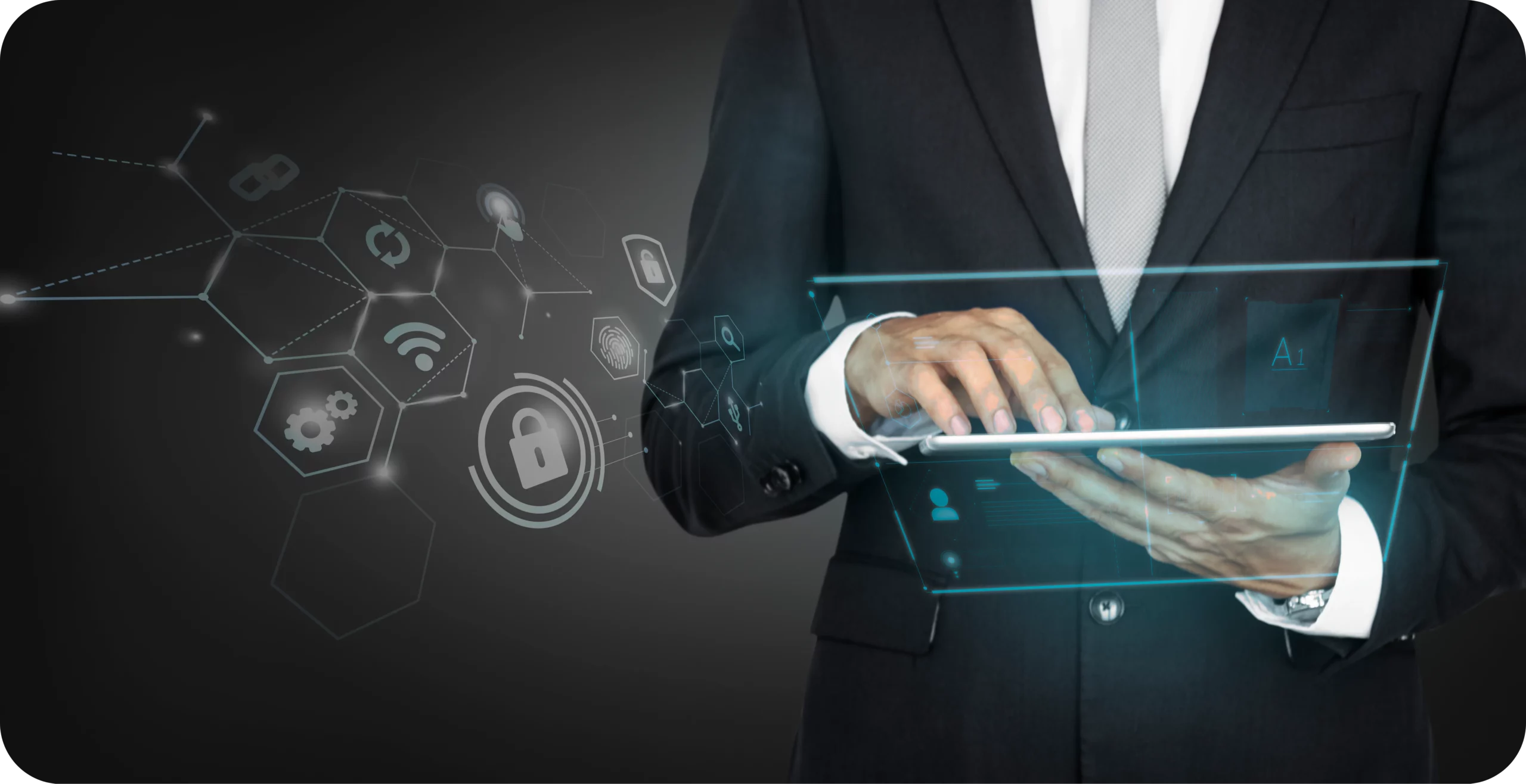
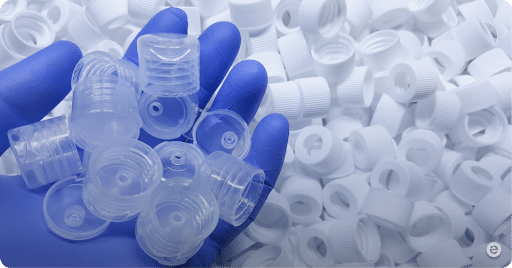
Revolucionar la fabricación de plásticos con IoT y análisis de datos
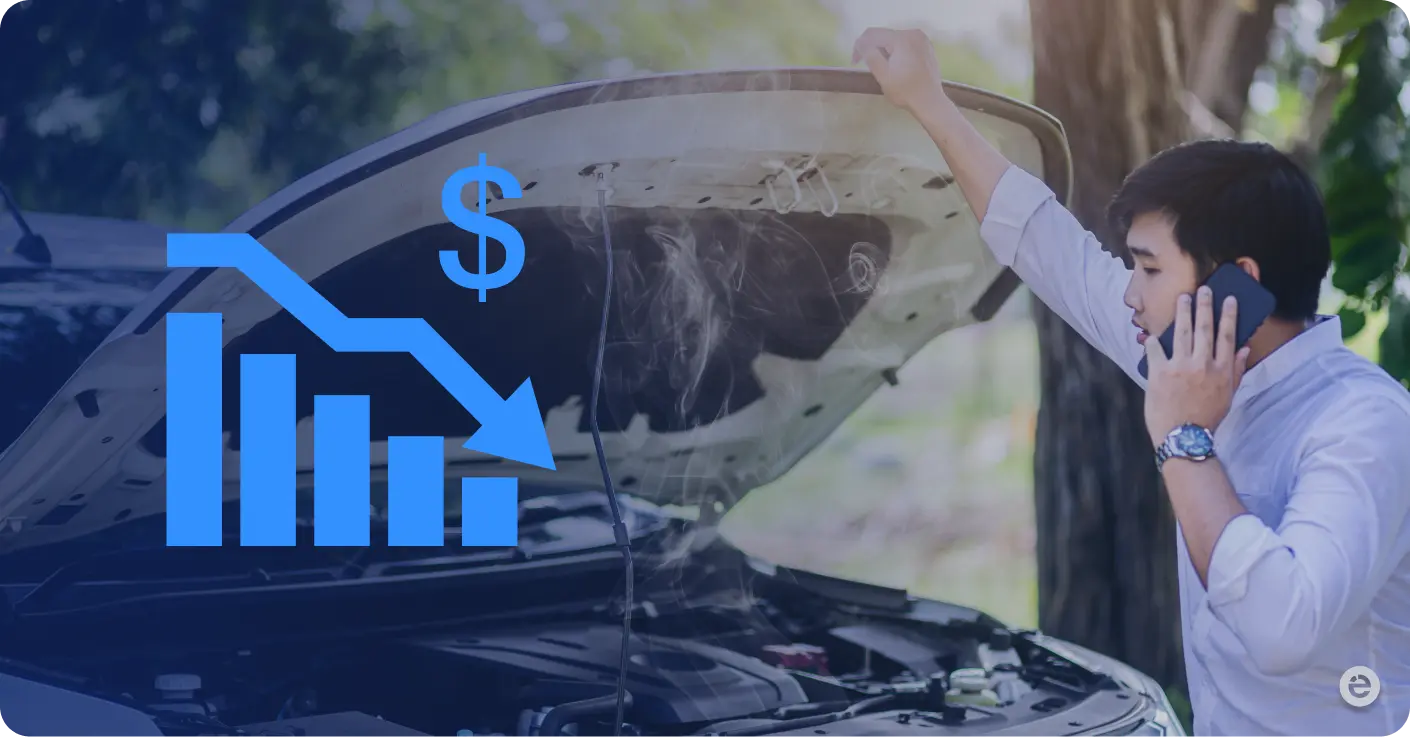
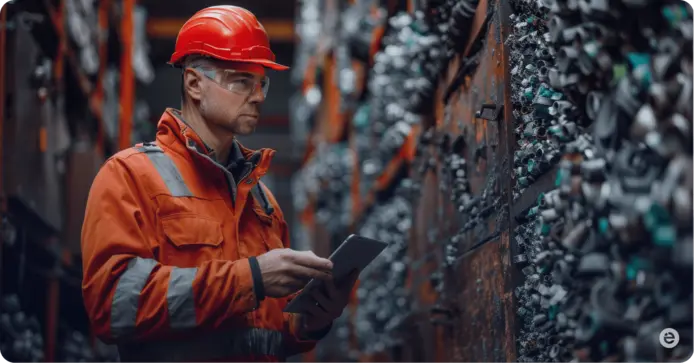
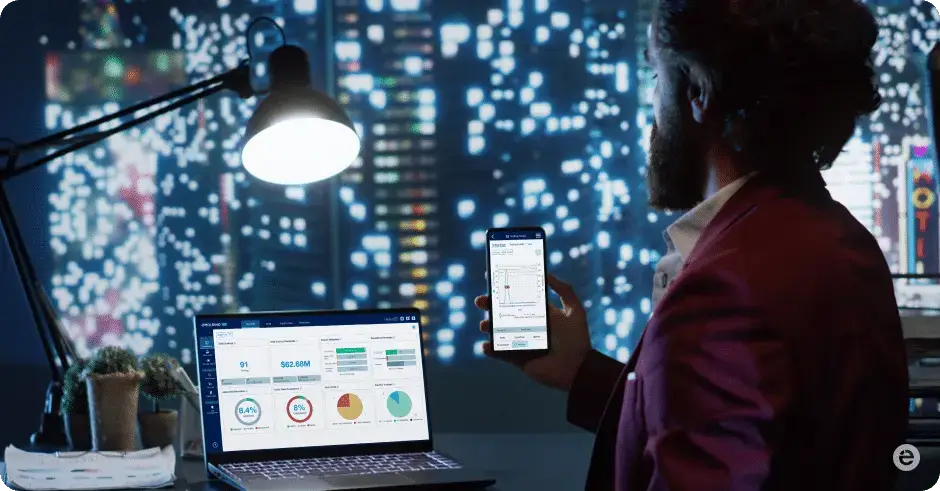
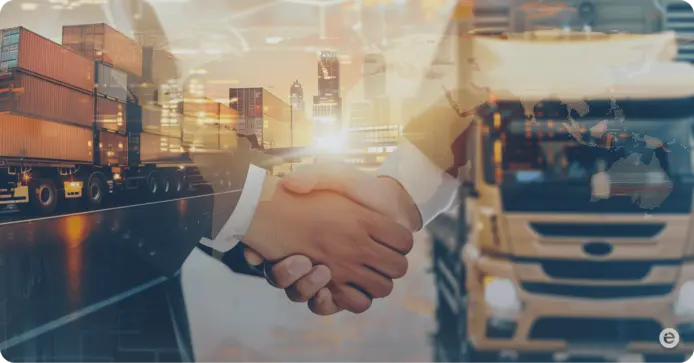
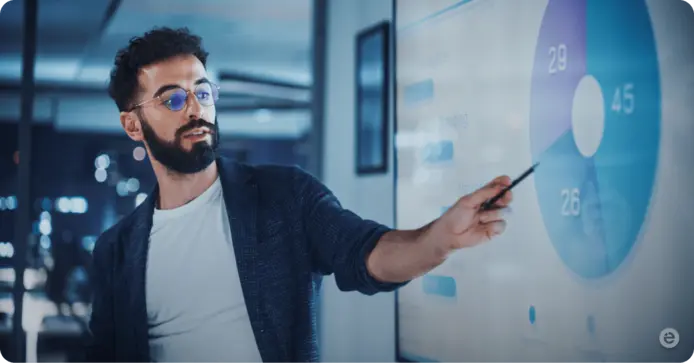
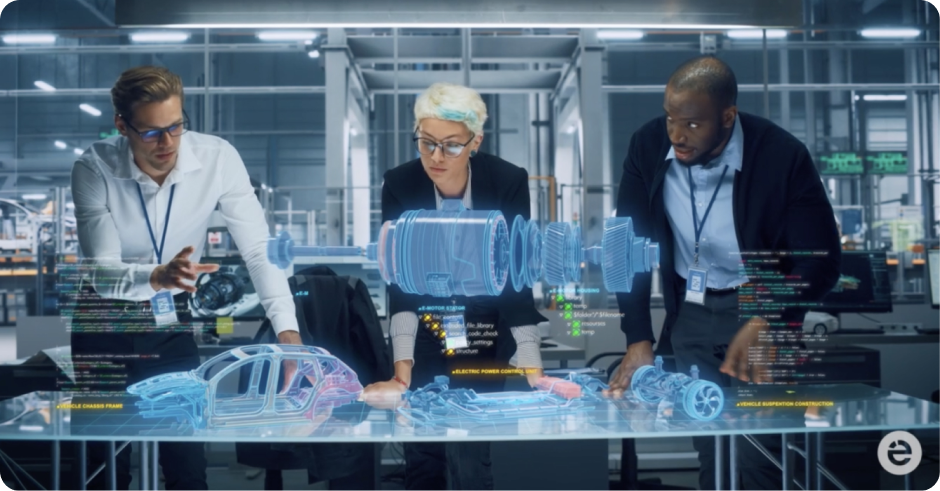
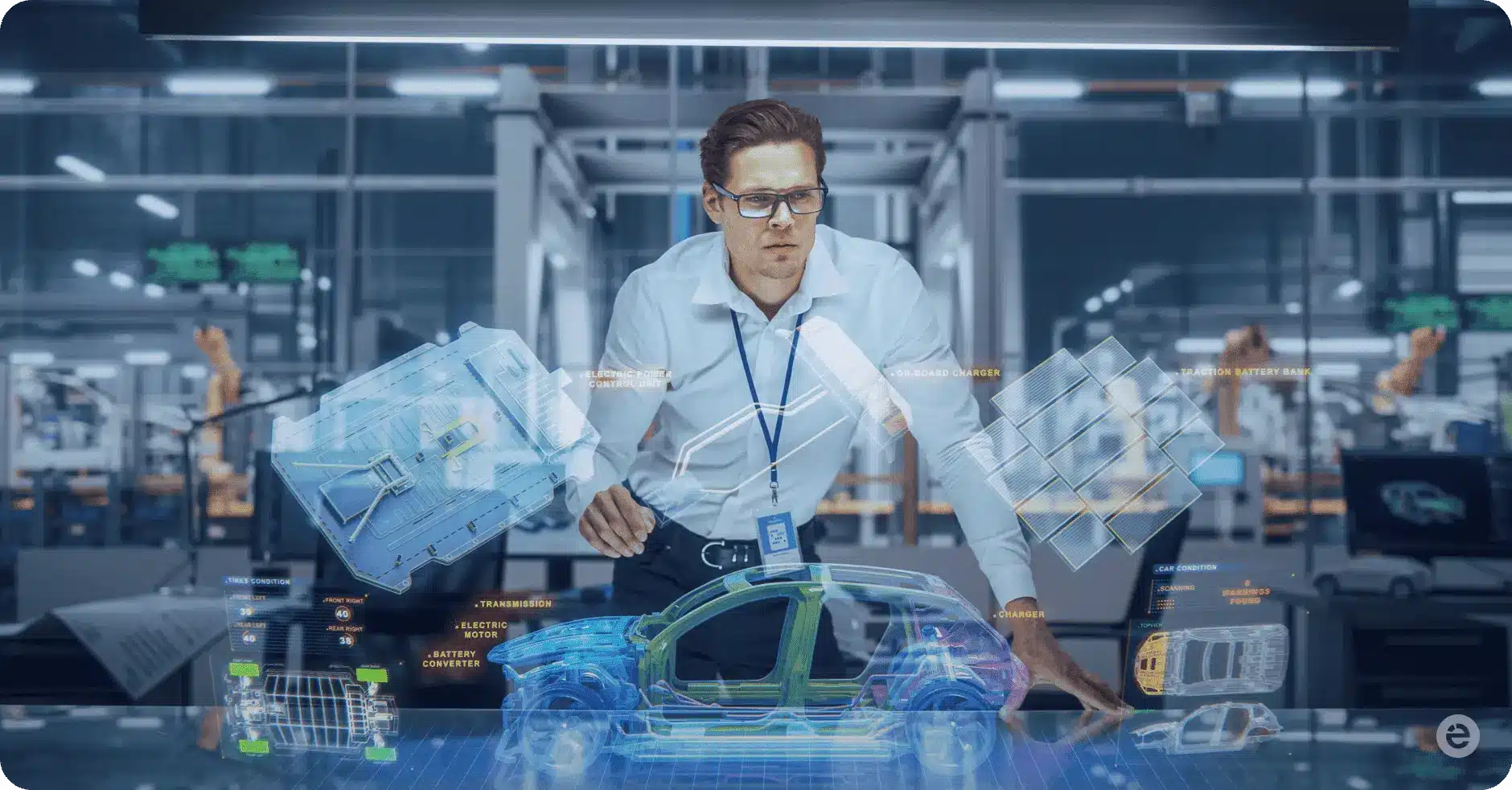
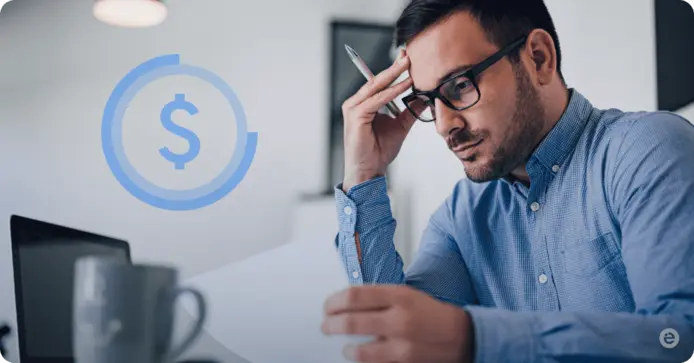