Continental embarked on a digital transformation initiative to modernize its tooling operations. In collaboration with eMoldino, the company introduced an innovative digital tooling management solution across multiple global facilities. This initiative yielded substantial financial returns and operational improvements within a short period, ultimately reducing costs by approximately $2 million.
Background and Challenges
Continental’s manufacturing facilities operate on a large scale, spanning in-house and outsourced locations. Before the transformation, several challenges were evident:
Inefficient Tooling Asset Management: Tools were rarely tracked in real-time, leading to difficulties pinpointing their location and condition, particularly in outsourced environments.
Paper-Based Data Collection: Manual data entry procedures slowed down maintenance workflows, limited visibility, and contributed to inaccuracies.
Limited Supplier Visibility: Vendors lacked a streamlined method to share data, resulting in inconsistent communication and production delays.
Unplanned Downtime: Maintenance practices were reactive, often only addressing equipment breakdowns after they occurred, causing higher repair costs and longer downtimes.
Recognizing the urgent need to modernize and monitor tooling assets more effectively, Continental sought our technology to deliver immediate, data-driven insights.
Partner Selection and Pilot Launch
Continental discovered eMoldino through a government-sponsored competition that recognized innovative industrial solutions. Among various vendors, we offered real-time data collection, rapid data processing, and robust supplier integration features.
The partnership began with a pilot program in Brazil, involving 47 tools installed with smart sensors at both Continental’s facilities and select supplier sites. Within this pilot:
- Preventive maintenance compliance soared to 100%.
- Quality-related costs dropped by 9%.
- Production performance increased by 8%.
- Maintenance teams saved approximately 30 hours per week.
Global Implementation Strategy
Following the promising pilot in Brazil, Continental implemented a phased global rollout strategy:
Regional Readiness: Each region underwent an assessment to determine readiness and resource allocation. Factors such as existing tooling workflows, supplier partnerships, and local regulatory considerations guided the rollout schedule.
Commodity-Based Deployment: The team strategically deployed sensors and systems based on commodity types—such as plastic injection and stamping—to standardize and streamline implementation.
Change Management and Training: Continental implemented robust change management strategies to address potential resistance from suppliers and internal teams. These included transparent data-sharing protocols, role-based user access controls, and targeted training programs to equip operators with the skills needed to use the new system effectively.
Over time, these measures helped build trust, alleviate security concerns, and demonstrate the value of real-time data for all stakeholders.
Technology Infrastructure
Continental’s transformation relied on our robust technological foundation, which comprises smart sensors, a unified data collection framework, and seamless integration with existing systems.
Smart Sensor Deployment
We deployed our wireless IoT sensors across Continental’s in-house plants, supplier facilities, and injection machines to continuously monitor critical production metrics such as shot counts, cycle times, and temperature data. For instance, 16 sensors were installed at in-house plants, 31 at supplier facilities, and 16 on injection machines. This deployment ensured comprehensive real-time monitoring across the production network.
数据收集框架
The data collection framework centralized sensor outputs, enabling real-time tracking of key parameters. This included monitoring production quality through shot counts and cycle times, maintaining optimal tool performance via temperature tracking, and automating preventive maintenance scheduling based on usage patterns.
与现有系统集成
The new platform seamlessly integrated with Continental’s legacy Manufacturing Execution Systems (MES), merging real-time sensor data with existing production workflows. It enabled secure, role-based data access for suppliers and in-house teams while automating alerts for maintenance, end-of-life predictions, and process deviations. Dedicated terminals and routers facilitated instantaneous data flow, supporting rapid and informed decision-making across facilities.
Measurable Business Impact
Since adopting our digital tooling solution, Continental has realized tangible cost reductions and performance improvements.
Cost reductions
The comprehensive performance tracking revealed the following gains:

These reductions stem largely from preventive maintenance scheduling, better supplier contracts (due to performance data), and minimized labor hours previously spent on manual processes.
” With eMoldino, our maintenance team gained full visibility of our tools, enabling preventative maintenance,” said Marllon Kopelvski, Supplier Quality Manager at Continental. “The proactive alerts are especially helpful, advising us when and how maintenance should be performed. And having all maintenance details in the system helps us keep track of all maintenance tasks in one place.”
Efficiency Improvements
The system’s operational efficiency gains have been remarkable:
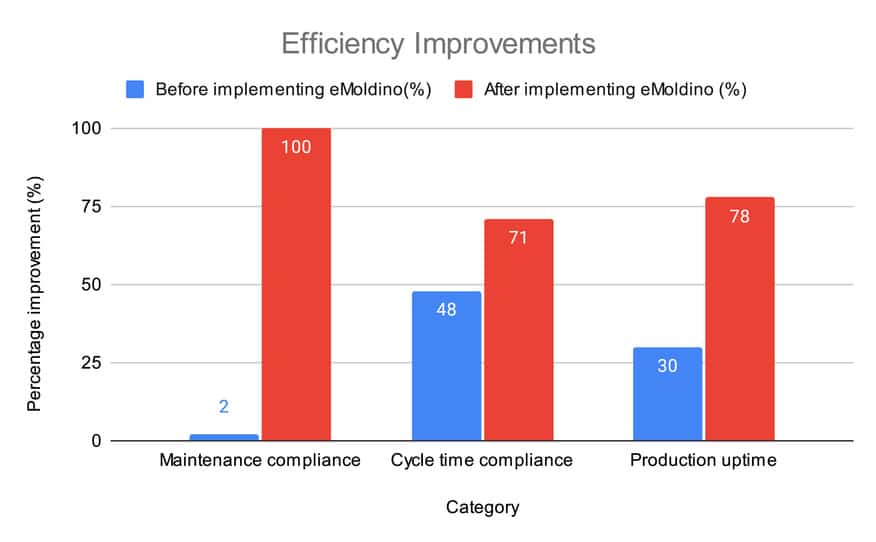
Implementing the system resulted in significant operational gains across multiple metrics, as visualized in the accompanying bar graph. Maintenance compliance surged from 0% to 100%, while cycle time compliance improved from 48% to 71%, reflecting enhanced adherence to production schedules. Injection molding operations achieved a notable production uptime of 77.77%. These improvements helped Continental achieve cost-reduction goals through better resource use and less downtime.
Return on Investment
The company implemented a robust ROI framework that captured direct cost savings and operational value. Key cost savings were achieved through lower maintenance expenses enabled by scheduled upkeep, reduced labor hours for manual data entry and analysis, and more effective supplier negotiations informed by real-time performance data. These measures directly contributed to substantial financial benefits.
Operational improvements further amplified the value, including enhanced machine availability, a 9% reduction in quality-related costs, and an 8% boost in overall production performance. These efforts resulted in an estimated $2 million in cost reductions.
The data-driven system continues to reveal new optimization opportunities, delivering sustained and recurring value over time.
结论
Continental’s digital transformation journey underscores the long-term value of modernizing manufacturing processes through smart digital tooling. By integrating automated sensors, streamlined data collection frameworks, and robust system integrations, the company successfully:
- Achieved a 9% reduction in quality-related costs.
- Improved production performance by 8%.
- Attained 100% preventive maintenance compliance in select facilities.
- Saved 30 hours per week in manual labor, amounting to $34,560 in annual working hours.
- Realized $2 million in cost reductions across global operations.
From a pilot program in Brazil to further expansions in Germany and the Czech Republic, Continental’s measured approach helped refine processes at each stage. The organization monitors 26 injection machines and 450 tools, leveraging real-time insights to schedule maintenance, prevent breakdowns, and fine-tune production settings.
关于作者
eMoldino
eMoldino 致力于数字化、简化和改造您的制造和供应链运营。我们帮助全球制造商推动企业创新,同时保持协作和可持续发展的核心价值。 请与我们联系,了解更多信息 →
您喜欢阅读这篇文章吗?
0 /5.计票: 0
浏览我们的最新文章
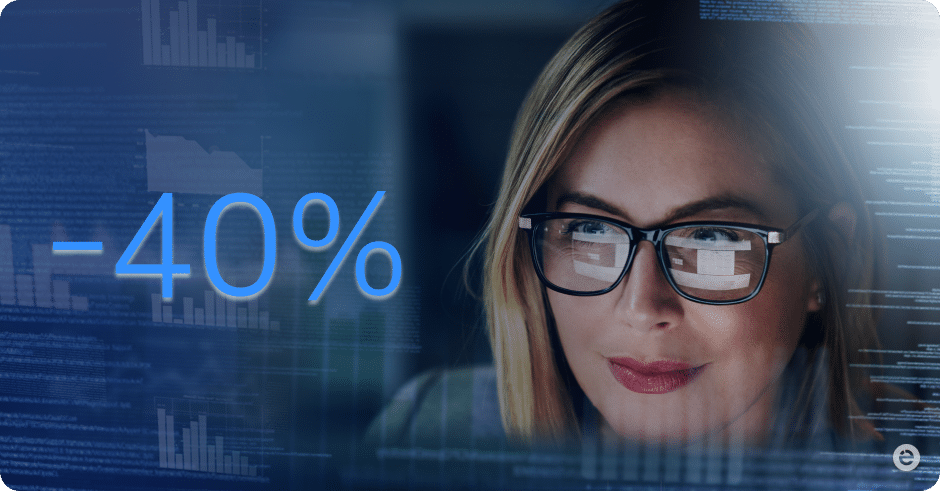
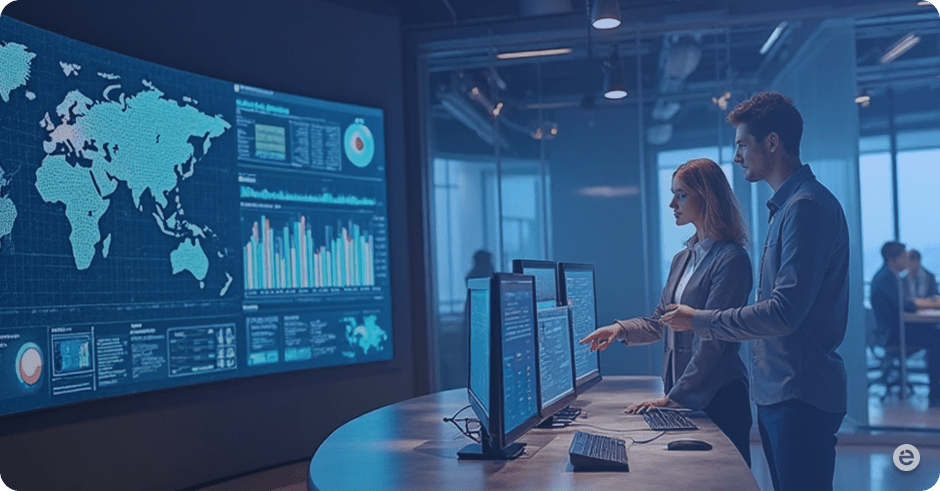
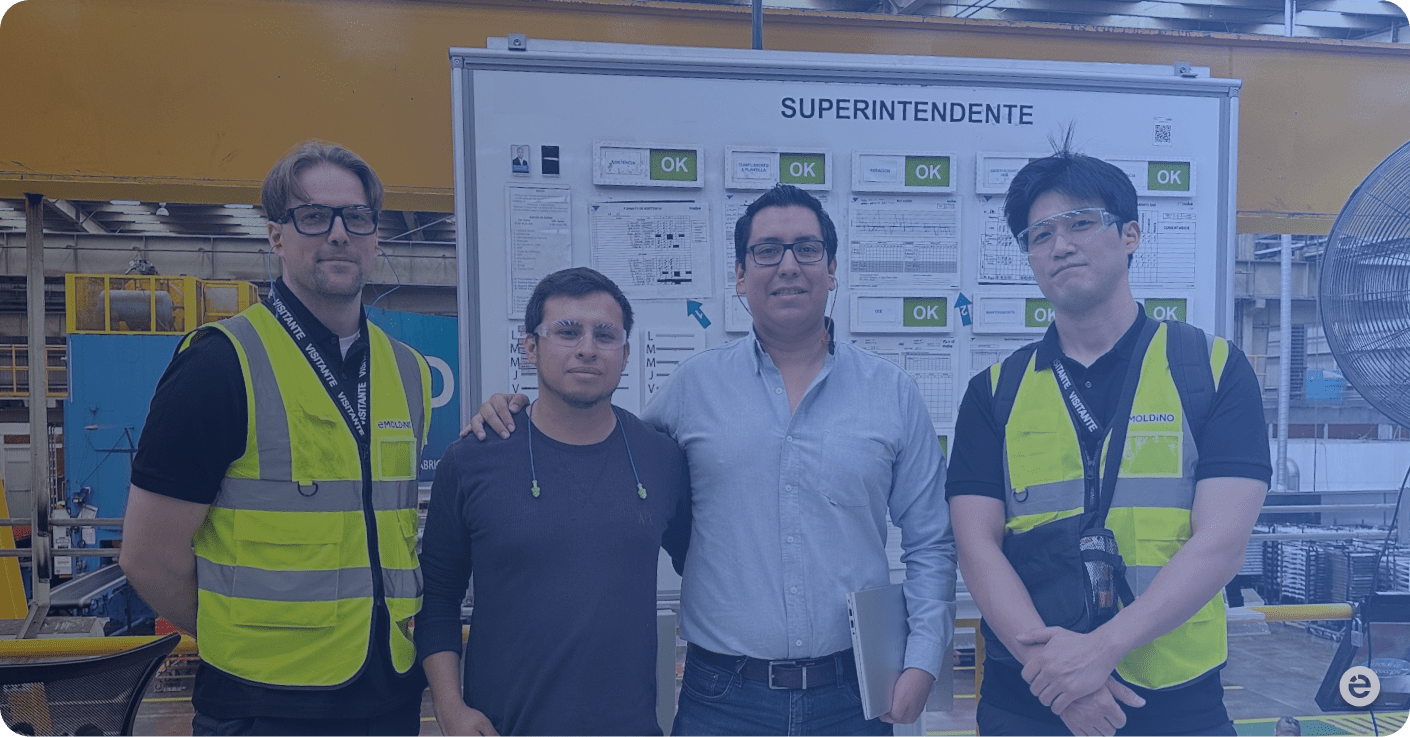
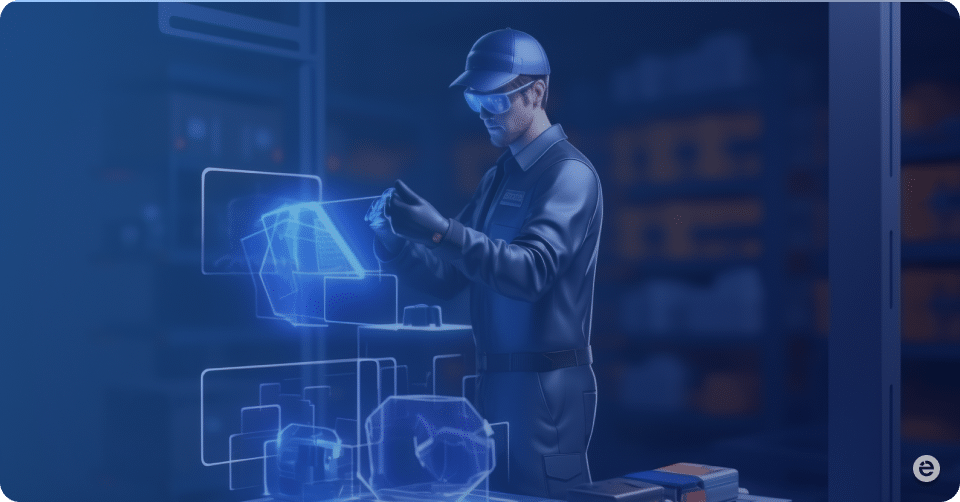
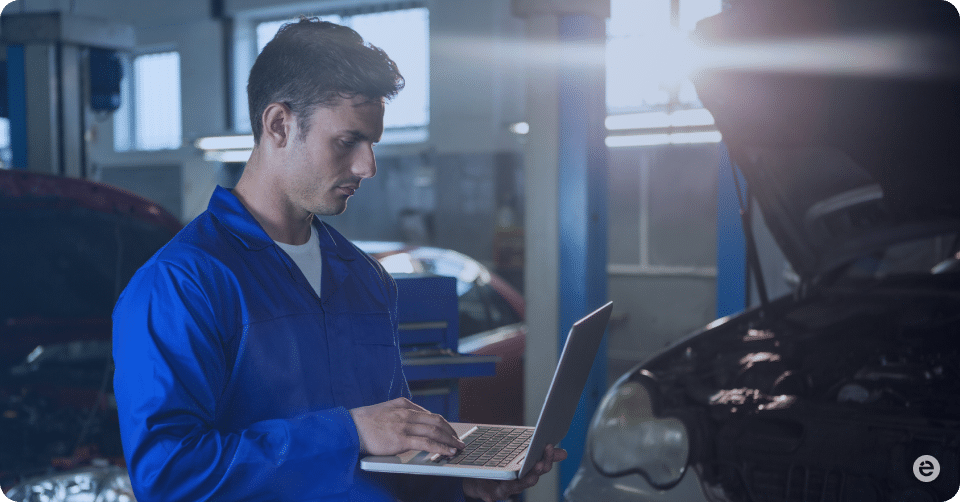