In today’s fast-paced automotive landscape, production disruptions are no longer the exception—they’re the norm. Each vehicle is built with over 30,000 individual components, many sourced from a complex web of global suppliers. This intricate supply chain means that a single point of failure—such as a delayed or malfunctioning tool—can ripple into costly downtime, production delays, and weakened relationships between OEMs and suppliers.
To build resilience, forward-thinking OEMs are turning to tooling digitalization, powered by IoT sensors. By embedding real-time sensors into tooling equipment and capturing operational data from the production floor, OEMs and suppliers alike are gaining the visibility they need to detect risks before they escalate.
Why End-to-End Visibility Matters
Despite its importance, only 17% of manufacturing professionals report having full end-to-end supply chain visibility. This lack of insight means that many OEMs only become aware of supplier-side issues after they’ve impacted production—when it’s already too late to act proactively. The consequences of this fragility became painfully clear during the COVID-19 pandemic. In 2020, U.S. auto production dropped by nearly 19%, primarily due to supplier disruptions. The communication breakdowns from the lack of tooling transparency between suppliers and OEMs often result in:
- Misuse and poor management of tooling assets
- Delayed parts production & increased scrap rate
- Inaccurate capacity planning
The Advantages of Tooling Digitalization
The integration of IoT sensors into tooling equipment provides OEMs and suppliers with real-time insights into tooling health and utilization. These sensors continuously monitor parameters such as shot count, cycle time, and temperature.The data is then centralized in a cloud-based platform, accessible to both OEMs and suppliers, enabling more informed and collaborative decision-making.
This level of visibility drives two key benefits:
1. Predictive Maintenance
By identifying abnormal tooling behavior early—such as fluctuating cycle times and temperature —predictive algorithms can forecast failures before they occur. This allows for scheduled maintenance rather than emergency repairs during critical production runs.
2. Capacity Planning
OEMs gain a real-time view of tooling utilization across supplier sites, ensuring that production plans align with real, available capacity, not just assumptions. This minimizes overbooking and underutilization, making operations more accurate and flexible.
The Road Ahead: Risk Management as a Strategic Advantage
Tooling digitalization does more than prevent disruptions—it reshapes how OEMs and suppliers collaborate. With data-driven insights replacing guesswork, supply chains become more adaptive, efficient, and trustworthy.
eMoldino’s digital tooling solutions empower manufacturers with the visibility they need to stay ahead of disruptions and operate with confidence. By digitizing tooling operations across global supply networks, eMoldino helps OEMs reduce unplanned downtime, improve production capacity, and build lasting resilience.
In an era where supplier visibility is a competitive advantage, tooling digitalization isn’t just a technical upgrade—it’s a strategic necessity.
Über den Autor
eMoldino
eMoldino zielt darauf ab, Ihre Fertigungs- und Lieferkettenprozesse zu digitalisieren, zu rationalisieren und zu transformieren. Wir helfen globalen Herstellern, die Unternehmensinnovationen vorantreiben und gleichzeitig die Grundwerte der Zusammenarbeit und Nachhaltigkeit beibehalten wollen. Sprechen Sie mit uns und erfahren Sie mehr →
Hat Ihnen die Lektüre dieses Artikels gefallen?
0 / 5 Auszählung der Stimmen: 0
Entdecken Sie unsere neuesten Beiträge
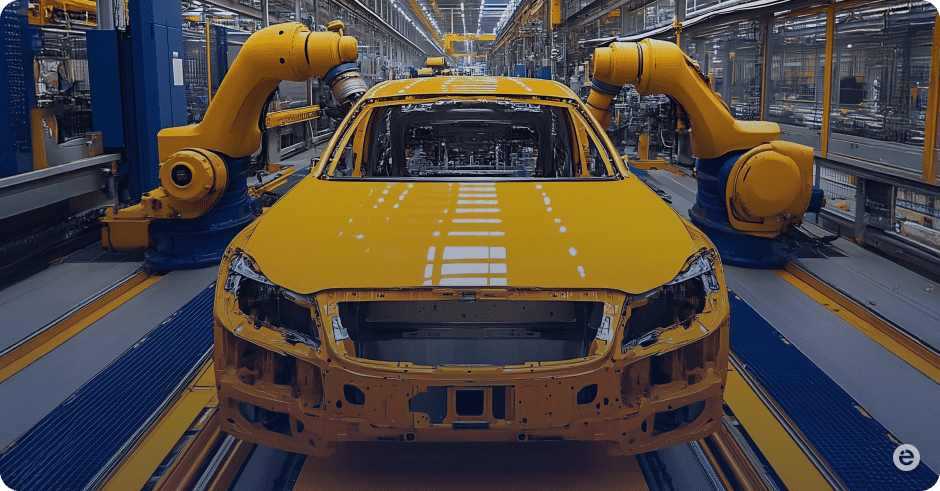
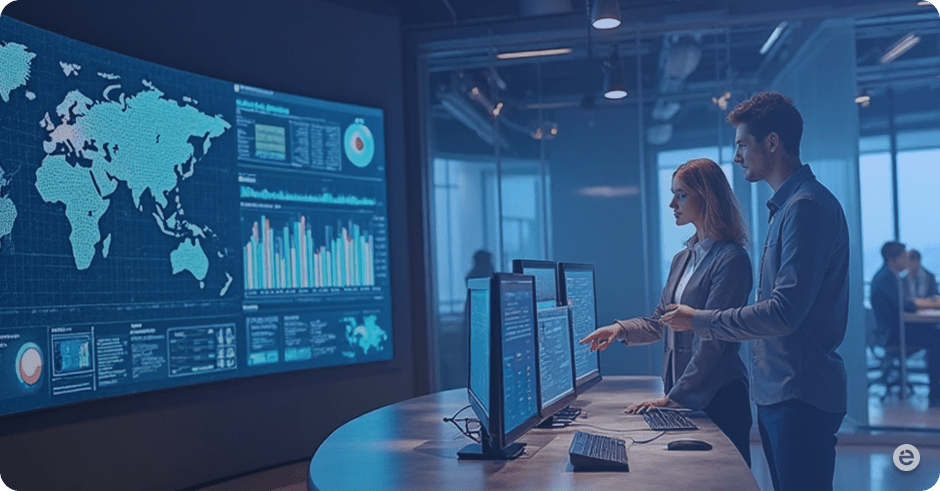

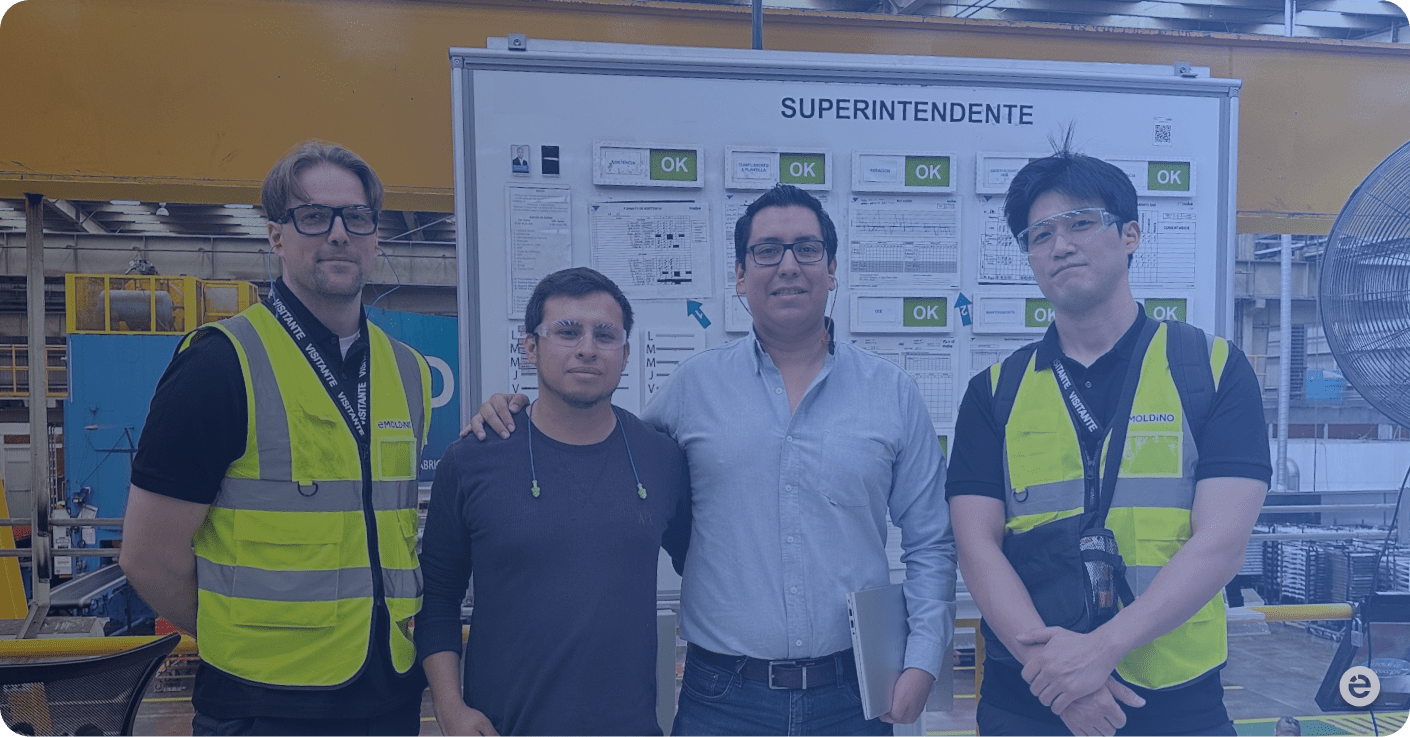
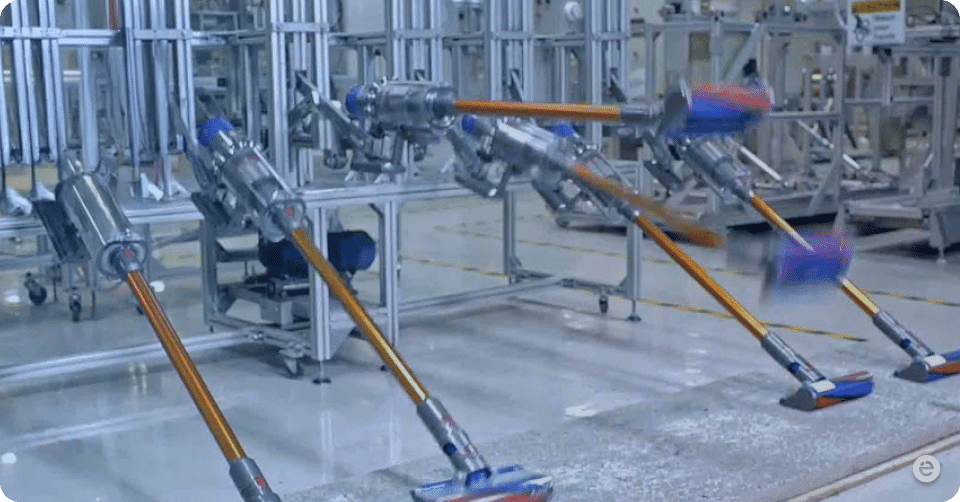
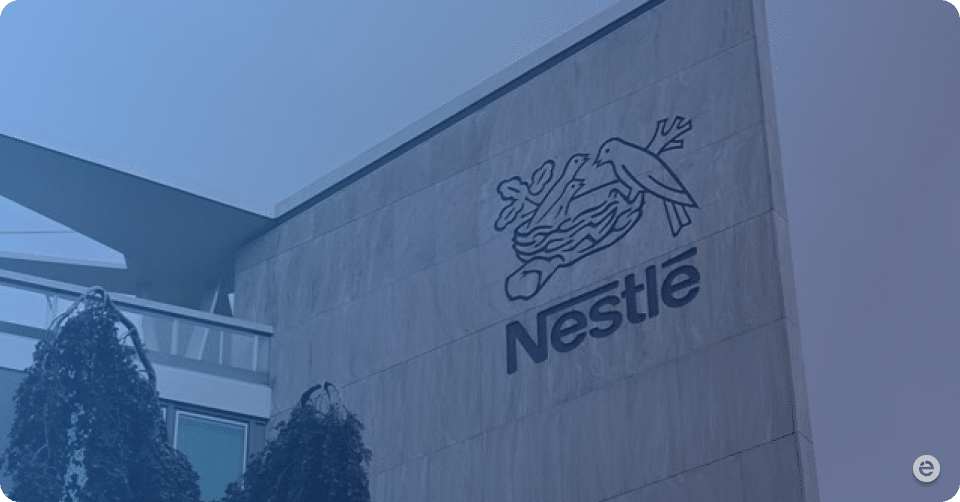
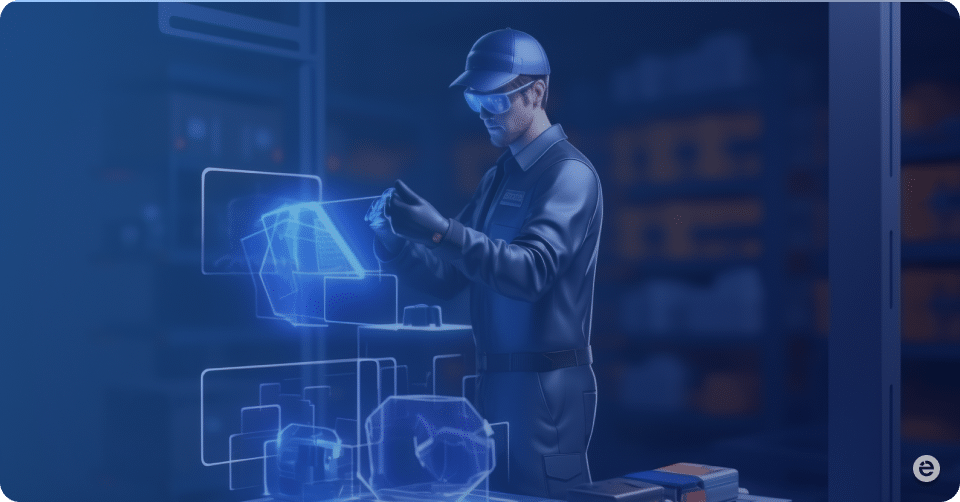
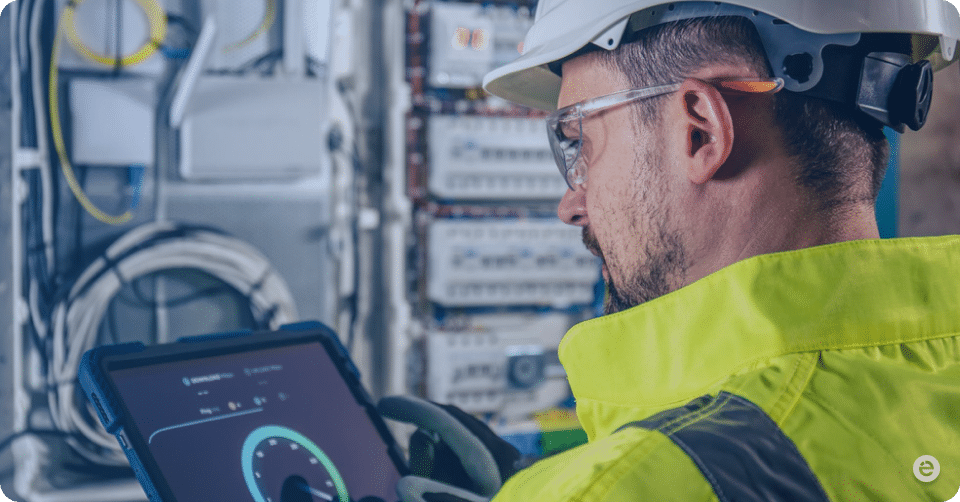
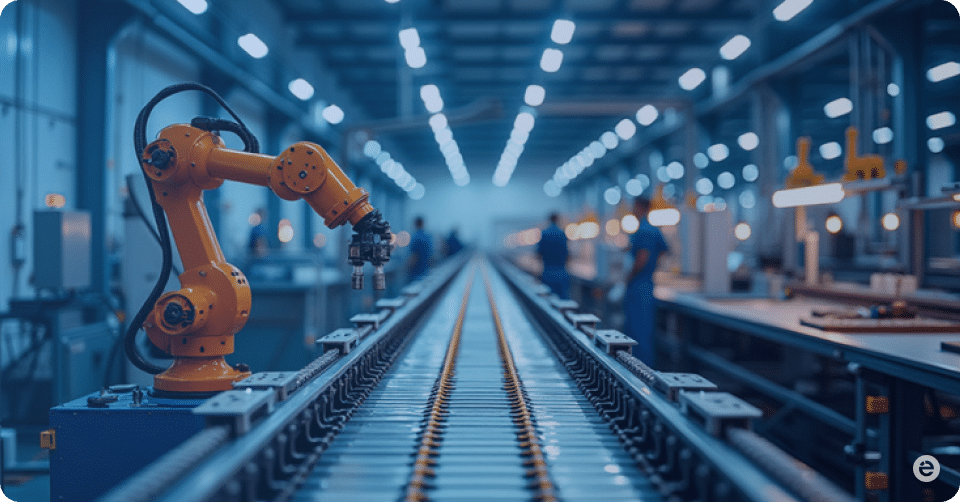
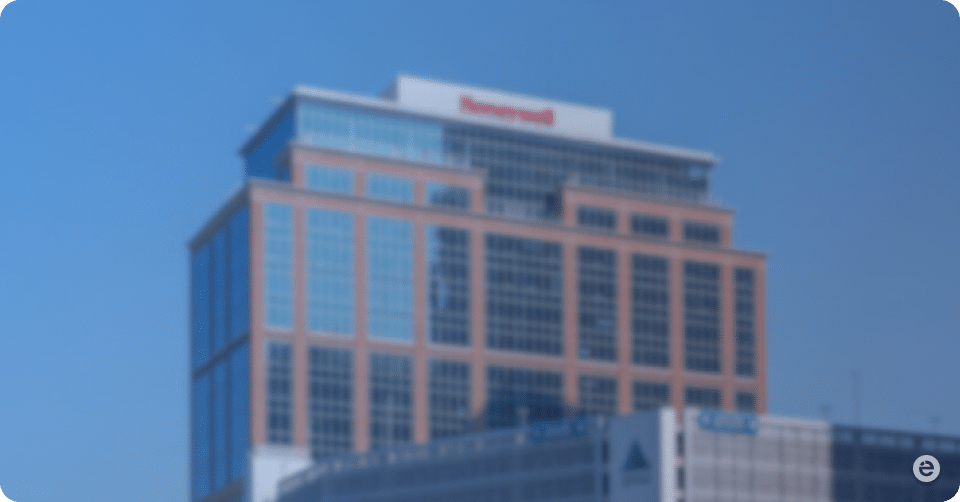
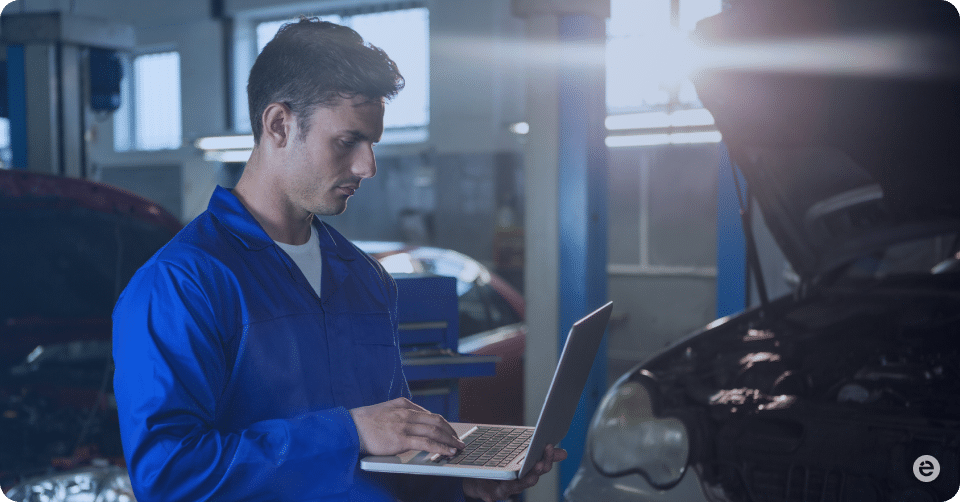
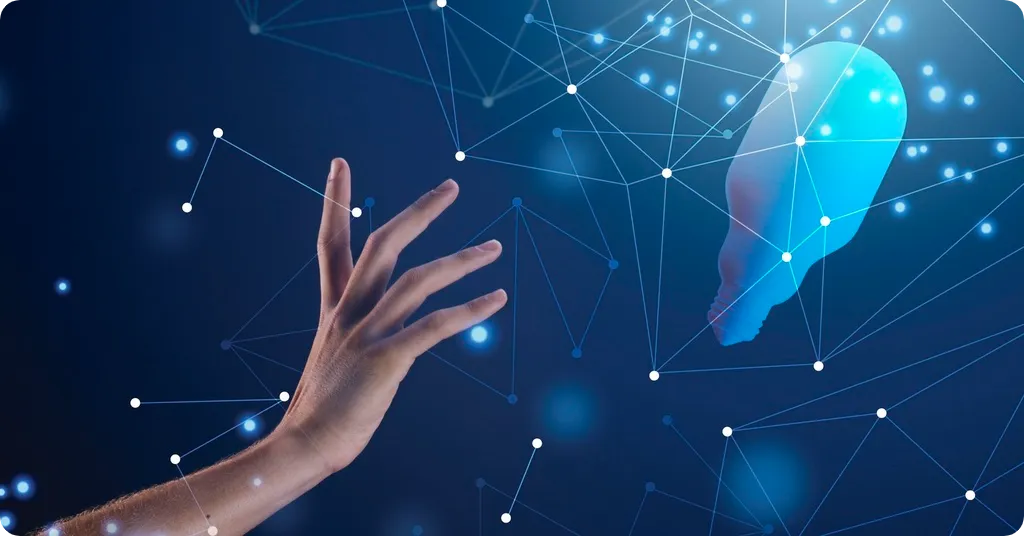